Washing money down the drain
Page 147
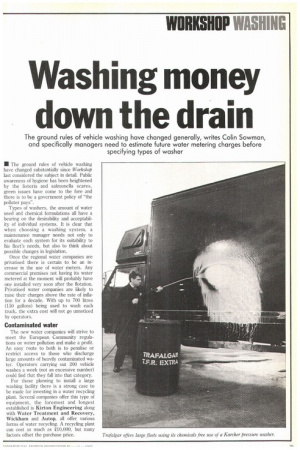
Page 148
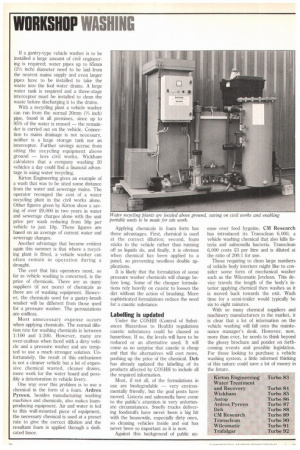
If you've noticed an error in this article please click here to report it so we can fix it.
• The ground rules of vehicle washing have changed substantially since Workshop last considered the subject in detail. Public awareness of hygiene has been heightened by the listeria and salmonella scares, green issues have come to the fore and there is to be a government policy of "the polluter pays".
Types of washers, the amount of water used and chemical formulations all have a bearing on the desirability and acceptability of individual systems. It is clear that when choosing a washing system, a maintenance manager needs not only to evaluate each system for its suitability to his fleet's needs, but also to think about possible changes in legislation.
Once the regional water companies are privatised there is certain to be an increase in the use of water meters. Any commercial premises not having its water metered at the moment will probably have one installed very soon after the flotation. Privatised water companies are likely to raise their charges above the rate of inflation for a decade. With up to 700 litres (150 gallons) being used to wash each truck, the extra cost will not go unnoticed by operators.
Contaminated water
The new water companies will strive to meet the European Community regulations on water pollution and make a profit. An easy route to both is to penalise or restrict access to those who discharge large amounts of heavily contaminated water. Operators carrying out 200 vehicle washes a week (not an excessive number) could find that they fall into that category.
For those planning to install a large washing facility there is a strong case to be made for investing in a water recycling plant. Several companies offer this type of equipment, the foremost and longest established is Kirton Engineering along with Water Treatment and Recovery, Wickham and Autop, all offer various forms of water recycling. A recycling plant can cost as much as £10,000, but many factors offset the purchase price.
If a gantry-type vehicle washer is to be installed a large amount of civil engineering is required; water pipes up to 65min (21/2 inch) diameter need to be laid from the nearest mains supply and even larger pipes have to be installed to take the waste into the foul water drains. A large water tank is required and a three-stage interceptor must be installed to clean the waste before discharging it to the drains.
With a recycling plant a vehicle washer can run from the normal 20mm (3/4 inch) pipe, found in all premises, since up to 95% of the water is reused — the remainder is carried out on the vehicle. Connection to mains drainage is not necessary, neither is a large storage tank nor an interceptor. Further savings accrue from siting the recycling equipment above ground — less civil works. Wickham calculates that a company washing 20 vehicles a day could find a financial advantage in using water recycling.
Kirton Engineering gives an example of a wash that was to be sited some distance from the water and sewerage mains. The operator recouped the cost of a water recycling plant in the civil works alone. Other figures given by Kirton show a saving of over £9,000 in two years in water and sewerage charges alone with the unit price per wash reducing from 56p per vehicle to just 10p. These figures are based on an average of current water and sewerage charges.
Another advantage that became evident again this summer is that where a recycling plant is fitted, a vehicle washer can often remain in operation during a drought.
The cost that hits operators most, so far as vehicle washing is concerned, is the price of chemicals. There are as many suppliers (if not more) of chemicals as there are of washing equipment. However, the chemicals used for a gantry-brush washer will be different from those used for a pressure washer. The permutations are endless.
Most unnecessary expense occurs when applying chemicals. The normal dilution rate for washing chemicals is between 1:100 and 1:200. However, many are over-zealous when faced with a dirty vehicle and a pressure washer and are tempted to use a much stronger solution. Unfortunately, the result of this enthusiasm is not a cleaner vehicle but a lot of expensive chemical wasted, cleaner drains, more work for the water board and possibly a deterioration in vehicle livery.
One way over this problem is to use a chemical in the form of a foam. Ardrox Pyreen, besides manufacturing washing machines and chemicals, also makes foamproducing equipment. Air and water is fed to this wall-mounted piece of equipment, the necessary chemical is used at a preset rate to give the correct dilution and the resultant foam is applied through a dedicated lance. Applying chemicals in foam form has three advantages. First, chemical is used at the correct dilution; second, foam sticks to the vehicle rather than running off as liquids do, and finally, it is obvious when chemical has been applied to a panel, so preventing needless double applications.
It is likely that the formulation of some pressure washer chemicals will change before long. Some of the cheaper formulations rely heavily on caustic to loosen the dirt without the action of brushing. More sophisticated formulations reduce the need for a caustic substance.
Labelling is updated
Under the COSHH (Control of Substances Hazardous to Health) regulations caustic substances could be classed as hazardous. If so, the levels will have to be reduced or an alternative used. It will come as no surprise that caustic is cheap and that the alternatives will cost more, pushing up the price of the chemical. Deb has already updated the labelling of its products affected by COSHH to include all the required information.
Most, if not all, of the formulations in use are biodegradable — very environmentally friendly, but the goal posts have moved. Listeria and salmonella have come to the public's attention in very unfortunate circumstances. Smelly trucks delivering foodstuffs have never been a big hit with the housewife, especially dirty ones, so cleaning vehicles inside and out has never been so important as it is now.
Against this background of public un
ease over food hygeine, CM Research has introduced its Transclean 6,000, a vehicle washing chemical that also kills listeria and salmonella bacteria. Transclean 6,000 costs 23 per litre and is diluted at the ratio of 200:1 for use.
Those requiring to clean large numbers of vehicle body interiors might like to consider some form of mechanical washer such as the Wilcomatic Jetclean. This device travels the length of the body's interior applying chemical then washes as it is moved back towards the exit. Wash time for a semi-trailer would typically be six to eight minutes.
With so many chemical suppliers and machinery manufacturers in the market, it is clear that a lot of information on the vehicle washing will fall onto the maintenance manager's desk. However, now, more than ever, he needs to think beyond the glossy brochure and ponder on forthcoming events and possible legislation. For those looking to purchase a vehicle washing system, a little informed thinking of this nature could save a lot of money in the future.