Sherpa first for springs
Page 21
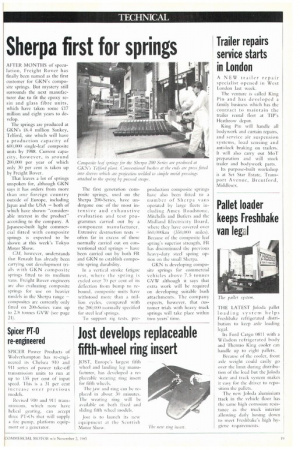
If you've noticed an error in this article please click here to report it so we can fix it.
AFTER MONTHS of speculation, Freight Rover has finally been named as the first customer for GKN's composite springs. But mystery still surrounds the next manufacturer due to tit the epoxy resin and glass fibre units, which have taken some £.17 million and eight years to develop.
The springs are produced at GKN's £6.4 million Sankey, Telford, site which will have a production capacity of
600,000 composite units by 1958. Current capa.city,•however, is around 200,000 per year of which only 30 per cent is taken up by Freight Rover.
That leaves a lot of springs unspoken for, although GKN says it has orders from more than one foreign co Ulltry outside of Europe, including Japan and the USA — hoth of . which have shown "considerable interest in the product-. according to the company. A Japanese-built light commercial fitted with composite springs is expected to be shown at this week's Tokyo Motor Show..
CM, however, understands that Renault has already been carrying out development trials with GKN composite springs fitted to its medium vans. Freight Rover engineers are also evaluating composite springs for use on heavier models in the Sherpa range — composites arc currently only fitted on 200-Series vans up to 2.8 tonnes GVW (see page 21).
The first generation composite springs, used on the Sherpa 200-Series, have undergone one of the most intensive and exhaustive evaluation and test programmes carried out by a component m mu fa cturer. Extensive destruction tests — often far in excess of those normally carried out on conventional steel springs — have been carried out by both FR and GKN to establish composite spring durability.
In a vertical stroke fatigue test, where the spring is cycled over 70 per cent of its deflection from bump to rebound, composite units have withstood more than a million cycles, compared with the 211) ,0(10.normally specified for steel leaf springs.
To support rig tests. pre production composite springs have also been fitted to a number of Sherpa vans operated by large fleets including Amey Roads tone. Mitchells and Butlers and the Midland Electricity Board, where they have covered over 560,1M0km (350,1)00 miles). Because of the composite leaf spring's superior strength, FR has discontinued the previous heavy-duty steel spring option on the small Sherpa.
GKN is developing composite springs for commercial vehicles above 7.5 tonnes GVW although it says that extra work will be required on developing suitable bush attachments. The company expects, however, that customer trials with heavy truck springs will take place within two years' time.