management matters
Page 74
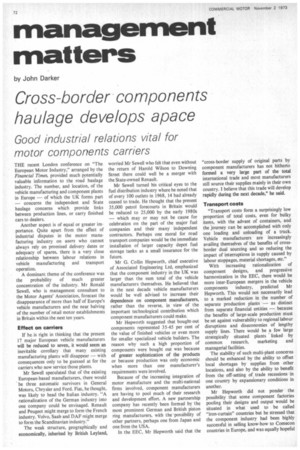
Page 75
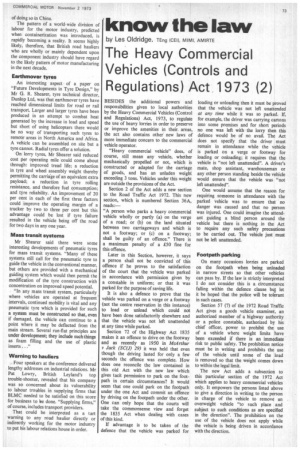
If you've noticed an error in this article please click here to report it so we can fix it.
by John Darker Cross-border-components
haulage develops apace
Good industrial relations vital for motor components carriers
THE recent London conference on "The European Motor Industry," arranged by the Financial Times, provided much potentially valuable information to the road haulage industry. The number, and location, of the vehicle manufacturing and component plants in Europe — of which the UK forms part — concerns the independent and State haulage concerns which provide links between production lines, or carry finished cars to dealers.
Another aspect is of equal or greater importance. Quite apart from the effect of industrial disputes in the motor manufacturing industry on users who cannot always rely on promised delivery dates or adequacy of spares, there is a very close relationship between labour relations in vehicle manufacturing and transport operation.
A dominant theme of the conference was the probability of much greater concentration of the industry. Mr Ronald Sewell. who is management consultant to the Motor Agents' Association, forecast the disappearance of more than half of Europe's vehicle manufacturers and the near halving of the number of retail motor establishments in Britain within the next ten years.
Effect on carriers
If he is right in thinking that the present 17 major European vehicle manufacturers will be reduced to seven, it would seem an inevitable corollary that many existing manufacturing plants will disappear — with consequences only to be guessed at for the carriers who now service those plants.
Mr Sewell speculated that of the existing European-based manufacturers, there would be three automatic survivors in General Motors, Chrysler and Ford. Fiat, he thought, was likely to head the Italian industry. "A rationalization of the German industry into one company could be envisaged. Renault and Peugeot might merge to form the French industry. Volvo. Saab and DAF might merge to form the Scandinavian industry."
The weak structure, geographically and economically, inherited by British Leyland, worried Mr Sewell who felt that even without the return of Harold Wilson to Downing Street there could well be a merger with the State-owned Renault.
Mr Sewell turned his critical eyes to the fuel distribution industry where he noted that of every 100 outlets in 1968, 14 had already ceased to trade. He thought that the present 35,000 petrol forecourts in Britain would be reduced to 25,000 by the early 1980s — which may or may not be cause for celebration on the part of the major fuel companies and their many independent contractors. Perhaps one moral for road transport companies would be the immediate installation of larger capacity depot fuel storage tanks as a small insurance for the future.
Mr G. Collin Hepworth, chief executive of Associated Engineering Ltd, emphasized that the component industry in the UK was larger than the sum total of the vehicle manufacturers themselves. He believed that in the next decade vehicle manufacturers would be well advised to increase their dependence on component manufacturers, rather than the reverse, in view of the important technological contribution which component manufacturers could make.
Mr Hepworth suggested that bought-out components represented 35-45 per cent of the value of finished vehicles or even more for smaller specialized vehicle builders. The reason why such a high proportion of components were bought out was because of greater sophistication of the products or because production was only economic when more than one manufacturer's requirements were involved.
Because of the increasing integration of motor manufacture and the multi-national firms involved, component manufacturers are having to pool much of their research and development effort. A new partnership company has recently been formed by the most prominent German and British piston ring manufacturers, with the 'possibility of other partners, perhaps one from Japan and one from the USA.
In the EEC, Mr Hepworth said that the "cross-border supply of original parts by component manufacturers has not hitherto formed a very large part of the total international trade and most manufacturers still source their supplies mainly in their own country. I believe that this trade will develop rapidly during the next decade," he said.
Transport costs "Transport costs form a surprisingly low proportion of total costs, even for bulky items, with the advent of containers, and the journey can be accomplished with only one loading and unloading of a truck. Vehicle manufacturers are increasingly availing themselves of the benefits of crossborder dual sourcing and so reducing the impact of interruptions in supply caused by labour stoppages, material shortages, etc."
With increasing rationalization of component designs, and progressive harmonization in the EEC, there would be more inter-European mergers in the vehicle components industry, predicted Mr Hepworth. This would not necessarily lead to a marked reduction in the number of separate production plants — as distinct from separate financial entities — because the benefits of large-scale production must be set against vulnerability to regional labour disruptions and diseconomies of lengthy supply lines. There would be a few large strategically situated plants linked by common research, marketing and managerial facilities.
The stability of such multi-plant concerns should be enhanced by the ability to offset local shortages by supplies from other locations, and also by the ability to benefit from the off-setting of trade recessions in one country by expansionary conditions in another.
Mr Hepworth did not ponder the possibility that some component factories pooling their designs and output would be situated in what used to be called "iron-curtain" countries but he stressed that the component industry had been highly successful in selling know-how to Comecon countries in Europe, and was equally hopeful of doing so in China.
The pattern of a world-wide division of labour for the motor industry, predicted when containerization was introduced, is rapidly becoming a reality. It seems highly likely, therefore, that British road hauliers who are wholly or mainly dependent upon the component industry should have regard to the likely pattern of motor manufacturing in the next decade.
Earthmover tyres An interesting aspect of a paper on "Future Developments in Tyre Design," by Mr G. R. Shearer, tyre technical director, Dunlop Ltd, was that earthmover tyres have reached dimensional limits for road or rail transport. Larger and larger tyres have been produced in an attempt to combat heat generated by the increase in load and speed but short of using helicopters there would be no way of transporting such tyres to remote areas in North America and Africa. A vehicle can be assembled on site but a tyre cannot. Radial tyres offer a solution.
On lorry tyres, Mr Shearer said reduced cost per operating mile could come about through: improved tread life; a reduction in tyre and wheel assembly weight thereby permitting the carriage of an equivalent extra payload; a reduction in tyre rolling resistance, and therefore fuel consumption; and tyre reliability. An improvement of 20 per cent in each of the first three factors could improve the operating margin of a trucker by two to three per cent but this advantage could be lost if tyre failure resulted in the vehicle being off the road for two days in any one year.
Mass transit systems Mr Shearer said there were some interesting developments of pneumatic tyres for mass transit systems. "Many of these systems still call for the pneumatic tyre to guide the vehicle in the conventional manner, but others are provided with a mechanical guiding system which would then permit the modification of the tyre construction with concentration on improved speed potential.
"In any mass transit system, particularly where vehicles are operated at frequent intervals, continued mobility is vital and any pneumatic tyre which is provided for such a system must be constructed so that, even if damaged, the vehicle can continue to a point where it may be deflected from the main stream. Several run-flat principles are under development; they include such things as foam filling and the use of plastic inserts ..."
Warning to hauliers Four speakers at the conference delivered lengthy addresses on industrial relations. Mr Pat Lowry, British Leyland's top trouble-shooter, revealed that his company was so concerned about its vulnerability to labour troubles in supplying firms that BLMC needed to be satisfied on this score for business to be done. "Supplying firms," of course, includes transport providers.
That could be interpreted as a tart warning to any road haulier directly or indirectly working for the motor industry to put his labour relations house in order.