by a special correspondent
Page 96
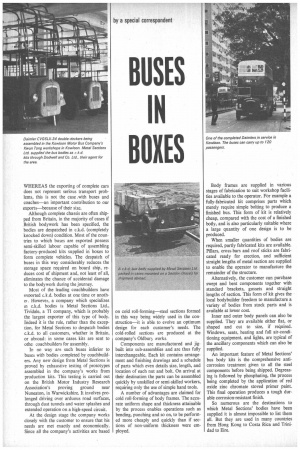
If you've noticed an error in this article please click here to report it so we can fix it.
BUSES IN BOXES
WHEREAS the exporting of complete cars does not represent serious transport problems, this is not the case .with buses and coaches—an important contribution to our exports—because of their size.
Although complete chassis are often shipped from Britain, in the majority of cases if British bodywork has been specified, the bodies are despatched in c.k.d. (completely knocked down) condition. Most of the countries to which buses are exported possess semi-skilled labour capable of assembling factory-produced kits supplied in boxes to form complete vehicles. The despatch of buses in this way considerably reduces the storage space required on board ship, reduces cost of shipment and, not least of all, eliminates the chance of accidental damage to the bodywork during the journey.
Most of the leading coachbuilders have exported c.k.d. bodies at one time or another. However, a company which specializes in c.k.d. bodies is Metal Sections Ltd., Tividale, a TI company, which is probably the largest exporter of this type of body. Indeed it is the rule, rather than the exception, for Metal Sections to despatch bodies c.k.d. to all customers, whether in Britain, or abroad: in some cases kits are sent to othe coachbuilders for assembly.
In no way are such buses inferior to buses with bodies completed by coachbuilders. Any new design from Metal Sections is proved by exhaustive testing of prototypes assembled in the company's works from production kits. This testing is carried out on the British Motor Industry Research Association's proving ground near Nuneaton, in Warwickshire. It involves prolonged driving over arduous road surfaces, through dust tunnels and water splashes and extended operation on a high-speed circuit.
At the design stage the company works closely with the customer to ensure that his needs are met exactly and economically. Since all the company's activities are based on cold roll-forming—steel sections formed in this way being widely used in the construction—it is able to evolve an optimum design for each customer's needs. The cold-rolled sections are produced at the company's Oldbury works.
Components are manufactured and jigbuilt into sub-assemblies and are thus fully interchangeable. Each kit contains arrangement and finishing drawings and a schedule of parts which even details size, length, and location of each nut and bolt. On arrival at their destination the parts can be assembled quickly by unskilled or semi-skilled workers, requiring only the use of simple hand tools.
A number of advantages are claimed for cold roll-forming of body frames. The accurate uniform shape and thickness attainable by the process enables operations such as bending, punching and so on, to be performed more cheaply and quickly than if sections of non-uniform thickness were employed. Body frames are supplied in various stages of fabrication to suit workshop facilities available to the operator. For example a fully-fabricated kit comprises parts which merely require simple bolting to produce a finished bus. This form of kit is relatively cheap, compared with the cost of a finished body, and is also particularly suitable where a large quantity of one design is to be produced.
When smaller quantities of bodies are required, partly fabricated kits are available. Pillars, cross-bars and roof sticks are fabricated ready for erection, and sufficient straight lengths of metal section are supplied to enable the operator to manufacture the remainder of the structure.
Alternatively, the customer can purchase swept and bent components together with standard brackets, gussets and straight lengths of section. This form of kit gives the local bodybuilder freedom to manufacture a variety of bodies from stock parts and is available at lower cost.
Inner and outer body panels can also be supplied. They are available either flat, or shaped and cut to size, if required. Windows, seats, heating and full air-conditioning equipment, and lights, are typical of the ancillary components which can also be supplied.
An important feature of Metal Sections' bus body kits is the comprehensive anticorrosion treatment given to all the steel components before being shipped. Degreasing is followed by phosphating, the process being completed by the application of red oxide zinc chromate staved primer paint. This final operation produces a tough durable corrosion-resistant finish.
So numerous are the destinations to which Metal Sections' bodies have been supplied it is almost impossible to list them all. But they are used in many countries from Hong Kong to Costa Rica and Trinidad to Eire.