Salt forces rusi into every seam
Page 46
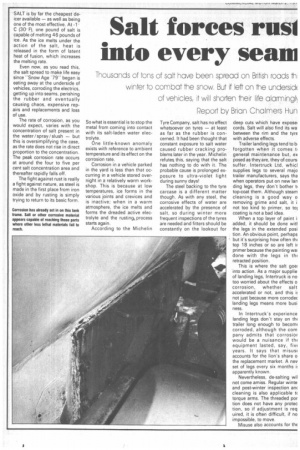
Page 47
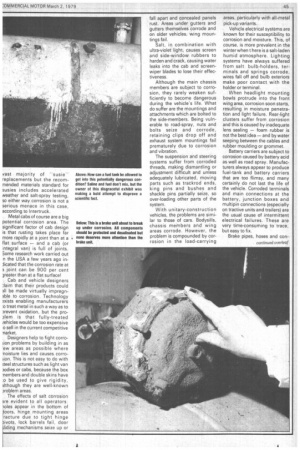
Page 48
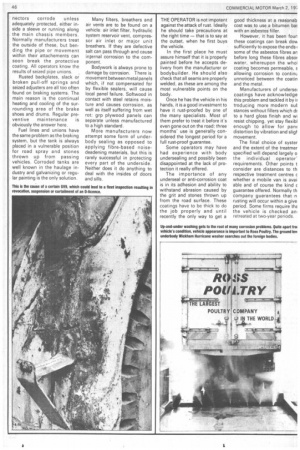
If you've noticed an error in this article please click here to report it so we can fix it.
Thousands of tons of salt have been spread on British roads tin winter to combat ne snow. But if left on ne undersidE of vehicles, t will shorten eir life alarmingl■ Report by Brian Chalmers Hun
SALT is by far the cheapest deicer available — as well as being one of the most effective. At -1 C (30 F), one pound of salt is capable of melting 46 pounds of ice. As the ice melts under the action of the salt, heat is released in the form of latent heat of fusion, which increases the melting rate.
Even now, as you read this, the salt spread to make life easy since -Snow Age '79began is eating away at the underside of vehicles, corroding the electrics, getting up into seams, perishing the rubber and eventually causing chaos, expensive repairs and replacements and loss of use.
The rate of corrosion, as you would expect, varies with the concentration of salt present in the water /spray/slush -but this is oversimplifying the case, as the rate does not rise in direct proportion to the concentration. The peak corrosion rate occurs at around the four to five per cent salt concentration area and thereafter rapidly falls off.
The fight against rust is really a fight against nature, as steel is made in the first place from iron oxide and by rusting is simply trying to return to its basic form. So what is essential is to stop the metal from coming into contact with its salt-laden water electrolyte.
One little-known anomaly exists with reference to ambient temperature and its effect on the corrosion rate.
Corrosion in a vehicle parked in the yard is less than that occurring in a vehicle stored overnight in a relatively warm workshop. This is because at low temperatures, ice forms in the various joints and crevices and is inactive; when in a warm atmosphere, the ice melts and forms the dreaded active electrolyte and the rusting, process starts again.
According to the Michelin Tyre Company, salt has no effect whatsoever on tyres — at least as far as the rubber is concerned. It had been thought that constant exposure to salt water caused rubber cracking problems later in the year. Michelin refutes this, saying that the salt has nothing to do with it, The probable cause is prolonged exposure to ultra-violet light during sunny days!
The steel backing to the tyre carcase is a different matter though. As with any steel, the corrosive effects of water are accelerated by the presence of salt, so during winter more frequent inspections of the tyres are needed and fitters should be constantly on the lookout for deep cuts which have expose: cords. Salt will also find its wa between the rim and the tyre with adverse effects.
Trailer landing legs tend to la forgotten when it comes ti general maintenance but, ex posed as they are, they of cours: suffer. lntertruck Ltd, whicl supplies legs to several majo trailer manufacturers, says tha when operators put on new Ian ding legs, they don't bother ti top-coat them. Although steam cleaning is a good way o removing grime and salt, it i not too kind to primer, so toi coating is not a bad idea.
When a top layer of paint i added, it should be done witl the legs in the extended posi tion. An obvious point, perhaps but it's surprising how often thi top 18 inches or so are left ir primer because the painting wa: done with the legs in thi retracted position.
This is where the salt goei into action. As a major supplie of landing legs, lntertruck is no too worried about the effects o corrosion, whether salt accelerated or not, and this not just because more corrode( landing legs means more busi ness.
In Inter-truck's experience landing legs don't stay on thi trailer long enough to becomr corroded, although the corn pany admits that corrosior would be a nuisance if tilt equipment lasted, say, fivr years. It says that misuso accounts for the lion's share o the replacement market. A nev set of legs every six months apparently known.
Nevertheless, de-salting wil not come amiss. Regular winte and post-winter inspection am cleaning is also applicable tr torque arms. The threaded por tion does not have any protec tion, so if adjustment is req uired, it is often difficult, if no impossible, to move.
Misuse also accounts for th(
vast majority of "susiereplacements but the recommended materials standard for susies includes accelerated iveather and salt-spray testing, 30 either way corrosion is not a serious menace in this case, according to Intertruck.
Metal cabs of course are a big potential corrosion area. The significant factor of cab design is that rusting takes place far more rapidly at a joint than at a Flat surface — and a cab (or .ntegral van) is full of joints. Some research work carried out
n the USA a few years ago inlicated that the corrosion rate at 3 joint can be 900 per cent )reater than at a flat surface!
Cab and vehicle designers laim that their products could 311 be made virtually impregn3ble to corrosion. Technology )xists enabling manufacturers :o treat metal in such a way as to )revent oxidation, but the pro)Iem is that fully-treated iehicles would be too expensive o sell in the current competitive narket.
Designers help to fight corro;ion problems by building in as 'ew areas as possible where noisture lies and causes corro;ion. This is not easy to do with steel structures such as light van )odies or cabs, because the box nembers and double skins have .o be used to give rigidity, 31though they are well-known )roblem areas.
The effects of salt corrosion The effects of salt corrosion
3
re evident to all operators -ioles appear in the bottom of Joors, hinge mounting areas .racture due to tight hinge )ivots, lock barrels fail, door ;liding mechanisms seize up or
fall apart and concealed panels rust. Areas under gutters and gutters themselves corrode and on older vehicles, wing mountings fail.
Salt, in combination with ultra-violet light, causes screen and side-window rubbers to harden and crack, causing water leaks into the cab and screenwiper blades to lose their effectiveness.
Although the main chassis members are subject to corrosion, they rarely weaken sufficiently to become dangerous during the vehicle's life. What do suffer are the mountings and attachments which are bolted to the side-members. Being vulnerable to road-spray, nuts and bolts seize and corrode, retaining clips drop off and exhaust system mountings fail prematurely due to corrosion and vibration.
The suspension and steering systems suffer from corroded threads, making dismantling or adjustment difficult and unless adequately lubricated, moving parts such as trackrod ends, king pins and bushes and shackle pins partially seize, so over-loading other parts of the system.
With unitary-construction vehicles, the problems are similar to those of cars. Bodysills, chassis members and wing areas corrode. However, the problem is compounded by corrosion in the load-carrying areas, particularly with all-metal pick-up variants.
Vehicle electrical systems are known for their susceptibility to corrosion and moisture. This, of course, is more prevalent in the winter when t here is a salt-laden humid atmosphere. Lighting systems have always suffered from salt. bulb-holders, terminals and springs corrode, wires fall off and bulb exteriors make poor contact with the holder or terminal.
When headlight mounting bowls protrude into the front wing area, corrosion soon starts, resulting in moisture penetration and light failure. Rear-light clusters suffer from corrosion and this is caused by inadequate lens sealing — foam rubber is not the best idea — and by water seeping between the cables and rubber moulding or grommet.
Battery carriers are subject to corrosion caused by battery acid as well as road spray. Manufacturers always appear to produce fuel-tank and battery carriers that are too flimsy, and many certainly do not last the life of the vehicle. Corroded terminals and main connections at the battery, junction boxes and multipin connections (especially on tractive units and trailers) are the usual cause of intermittent electrical failures. These are very time-consuming to trace, but easy to fix.
Brake pipes, hoses and concontinued overleaf
nectors corrode unless adequately protected, either inside a sleeve or running along the main chassis members. Normally manufacturers treat the outside of these, but bending the pipe or movement within their attachements can soon break the protective coating. All operators know the results of seized pipe unions. _ Rusted backplates, slack or broken pull-off springs and seized adjusters are all too often found on braking systems. The main reason is the continual heating and cooling of the surrounding area of the brake shoes and drums. Regular pre ventive maintenance is obviously the answer here.
Fuel lines and unions have the same problem as the braking system, but the tank is always placed in a vulnerable position for road spray and stones thrown up from passing vehicles. Corroded tanks are well known in the haulage industry and galvanizing or regular painting is the only solution. Many filters, breathers and air vents are to be found on a vehicle, air inlet filter, hydraulic system reservoir vent, compressor air inlet or major unit breathers. If they are defective salt can pass through and cause internal corrosion to the component.
Bodywork is always prone to damage by corrosion. There is movement between metal panels which, if not compensated for by flexible sealers, will cause local panel failure. Softwood in contact with steel retains moisture and causes corrosion, as well as itself suffering from wet rot; grp plywood panels can separate unless manufactured to a high standard.
More manufacturers now attempt some form of underbody sealing as opposed to applying fibre-based noisedeadening materials, but this is rarely successful in protecting every part of the underside. Neither does it do anything to deal with the insides of doors and sills. THE OPERATOR is not impotent against the attack of rust. Ideally he should take precautions at the right time — that is to say at the outset, when he first buys the vehicle.
In the first place he must assure himself that it is properly painted before he accepts delivery from the manufacturer or bodybuilder. He should also check that all seams are properly welded, as these are among the most vulnerable points on the body.
Once he has the vehicle in his hands, it is a good investment to have it rust-proofed by one of the many specialists. Most of them prefer to treat it before it's even gone out on the road; three months' use is generally considered the longest period for a full rust-proof guarantee.
Some operators may have had experience with body undersealing and possibly been disappointed at the lack of protection it really offered.
The importance of any underseal or anti-corrosion coat is in its adhesion and ability to withstand abrasion caused by the grit and stones thrown up from the road surface. These coatings have to be thick to do the job properly and until recently the only way to get a good thickness at a reaonab cost was to use a bitumen ba with an asbestos filler.
However, it has been four these coatings can break dow sufficiently to expose the ends some of the asbestos fibres an before long these fibres absor water, whereupon the whol coating becomes permeable, s allowing corrosion to continu unnoticed between the coatin and the metal.
Manufacturers of undersei coatings have acknowledge this problem and tackled it by ir troducing more modern silt stances without fillers which dr to a hard gloss finish and wi resist chipping, yet stay flexibl enough to allow for pan( distortion by vibration and sligf movement.
The final choice of syster and the extent of the treatmer specified will depend largely o the individual operator' requirements. Other points t consider are distances to th respective treatment centres c whether a mobile van is avai able and of course the kind c guarantee offered. Normally th company guarantees that n rusting will occur within a give period. Some firms require th2 the vehicle is checked an retreated at two-year periods_