WHAT' ONE MORE PROBLEM?
Page 106
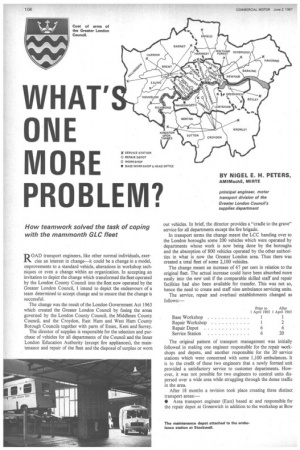
Page 107
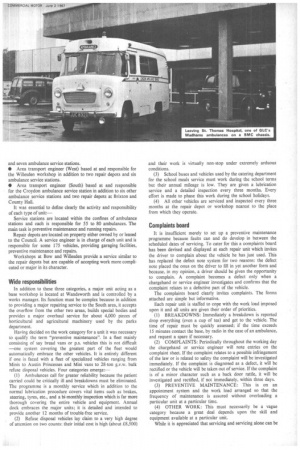
Page 108
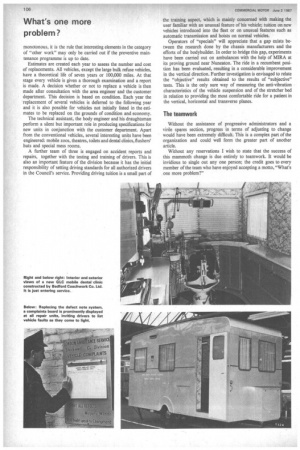
If you've noticed an error in this article please click here to report it so we can fix it.
How teamwork solved the task of coping with the mammonth GLC fleet ROAD transport engineers, like other normal individuals, exercise an interest in change—it could be a change in a model, improvements to a standard vehicle, alterations in workshop techniques or even a change within an organization. In accepting an invitation to depict the change which transformed the fleet operated by the London County Council into the fleet now operated by the Greater London Council, I intend to depict the endeavours of a team determined to accept change and to ensure that the change is successful.
The change was the result of the London Government Act 1963 which created the Greater London Council by fusing the areas governed by the London County Council, the Middlesex County Council, and the Croydon, East Ham and West Ham County Borough Councils together with parts of Essex, Kent and Surrey.
The director of supplies is responsible for the selection and purchase of vehicles for all departments of the Council and the Inner London Education Authority (except fire appliances), the maintenance and repair of the fleet and the disposal of surplus or worn out vehicles. In brief, the director provides a "cradle to the grave" service for all departments except the fire brigade.
In transport terms the change meant the LCC handing over to the London boroughs some 200 vehicles which were operated by departments whose work is now being done by the boroughs and the absorption of 800 vehicles operated by the other authorities in what is now the Greater London area. Thus there was created a total fleet of some 2,100 vehicles.
The change meant an increase of 67 per cent in relation to the original fleet. The actual increase could have been absorbed more easily into the new unit if the comparable skilled staff and repair facilities had also been available for transfer. This was not so, hence the need to create and staff nine ambulance servicing units.
The service, repair and overhaul establishments changed as follows:—
Prior to After
1 April 1965 1 April 1965
Base Workshop 1
Repair Workshop 1 2 Repair Depot 6 6 Service Station 6 20
The original pattern of transport management was initially followed in making one engineer responsible for the repair workshops and depots, and another responsible for the 20 service stations which were concerned with some 1,100 ambulances. It is to the credit of these two engineers that a newly formed unit provided a satisfactory service to customer departments. However, it was not possible for two engineers to control units dispersed over a wide area while struggling through the dense traffic in the area.
After 18 months a revision took place creating three distinct transport areas:— • Area transport engineer (East) based at and responsible for the repair depot at Greenwich in addition to the workshop at Bow and seven ambulance service stations.
• Area transport engineer (West) based at and responsible for the Willesden workshop in addition to two repair depots and six ambulance service stations.
• Area transport engineer (South) based at and responsible for the Croydon ambulance service station in addition to six other ambulance service stations and two repair depots at Brixton and County Hall.
It was essential to define clearly the activity and responsibility of each type of unit:—
Service stations are located within the confines of ambulance stations and each is responsible for 55 to 80 ambulances. The main task is preventive maintenance and running repairs.
Repair depots are located on property either owned by or leased to the Council. A service engineer is in charge of each unit and is responsible for some 175 vehicles, providing garaging facilities, preventive maintenance and repairs.
Workshops at Bow and Willesden provide a service similar to the repair depots but are capable of accepting work more complicated or major in its character.
Wide responsibilities
In addition to these three categories, a major unit acting as a base workshop is located at Wandsworth and is controlled by a works manager. Its function must be complex because in addition to providing a major repairing service to the South area, it accepts the overflow from the other two areas, builds special bodies and provides a major overhaul service for about 4,000 pieces of horticultural and agricultural machinery used by the parks department.
Having decided on the work category for a unit it was necessary to qualify the term "preventive maintenance". In a fleet mainly consisting of say bread vans or p.s. vehicles this is not difficult —one system covering the greatest part of the fleet would automatically embrace the other vehicles. It is entirely different if one is faced with a fleet of specialized vehicles ranging from Minis to Austin Princesses and Mini vans to 28-ton g.v.w. bulk refuse disposal vehicles. Four categories emerge:—
(1) Ambulances call for greater reliability because the patient carried could be critically ill and breakdowns must be eliminated. The programme is a monthly service which in addition to the normal lubrication procedure covers vital items such as brakes, steering, tyres, etc., and a bi-monthly inspection which is far more thorough covering the entire vehicle and equipment. Annual dock embraces the major units; it is detailed and intended to provide another 12 months of trouble-free service.
(2) Refuse disposal vehicles lay claim to a very high degree of attention on two counts: their initial cost is high (about £8,500) and their work is virtually non-stop under extremely arduous conditions.
(3) School buses and vehicles used by the catering department for the school meals service must work during the school terms but their annual mileage is low. They are given a lubrication service and a detailed inspection every three months. Every effort is made to phase this work during the school holidays.
(4) All other vehicles are serviced and inspected every three months at the repair depot or workshop nearest to the place from which they operate.
Complaints board
It is insufficient merely to set up a preventive maintenance programme because faults can and do develop in between the scheduled dates of servicing. To cater for this a complaints board has been devised and displayed at each repair unit which invites the driver to complain about the vehicle he has just used. This has replaced the defect note system for two reasons: the defect note placed the onus on the driver to fill in yet another form and because, in my opinion, a driver should be given the opportunity to complain. A complaint becomes a defect only when a chargehand or service engineer investigates and confirms that the complaint relates to a defective part of the vehicle.
The complaints board clearly invites complaints. The forms attached are simple but informative.
Each repair unit is staffed to cope with the work load imposed upon it and all units are given their order of priorities.
(1) BREAKDOWNS: Immediately a breakdown is reported drop everything (even a cup of tea) and get to the vehicle. The time of repair must be quickly assessed; if the time exceeds 15 minutes contact the base, by radio in the case of an ambulance, and request a spare if necessary.
(2) COMPLAINTS: Periodically throughout the working day the chargehand or service engineer will note entries on the complaint sheet. If the complaint relates to a possible infringement of the law or is related to safety the complaint will be investigated immediately. If the complaint is diagnosed as a defect, it will be rectified or the vehicle will be taken out of service. If the complaint is of a minor character such as a back door rattle, it will be investigated and rectified, if not immediately, within three days.
(3) PREVENTIVE MAINTENANCE: This is on an appointment system and the work load arranged so that the frequency of maintenance is assured without overloading a particular unit at a particular time.
(4) OTHER WORK: This must necessarily be a vague category because a great deal depends upon the skill and equipment available at a particular unit.
While it is appreciated that servicing and servicing alone can be monotonous, it is the rule that interesting elements in the category of "other work" may only be carried out if the preventive maintenance programme is up to date.
Estimates are created each year to assess the number and cost of replacements. All vehicles, except the large bulk refuse vehicles, have a theoretical life of seven years or 100,000 miles. At that stage every vehicle is given a thorough examination and a report is made. A decision whether or not to replace a vehicle is then made after consultation with the area engineer and the customer department. This decision is based on condition. Each year the replacement of several vehicles is deferred to the following year and it is also possible for vehicles not initially listed in the estimates to be replaced on the grounds of condition and economy.
The technical assistant, the body engineer and his draughtsman perform a silent but important role in producing specifications for new units in conjunction with the customer department. Apart from the conventional vehicles, several interesting units have been engineered: mobile zoos, theatres, toilets and dental clinics, flus hers' huts and special mess rooms.
A further team of three is engaged on accident reports and repairs, together with the testing and training of drivers. This is also an important feature of the division because it has the initial responsibility of setting driving standards for all authorized drivers in the Council's service. Providing driving tuition is a small part of the training aspect, which is mainly concerned with making the user familiar with an unusual feature of his vehicle; tuition on new vehicles introduced into the fleet or on unusual features such as automatic transmission and hoists on normal vehicles.
Operators of "specials" will appreciate that a gap exists between the research done by the chassis manufacturers and the efforts of the bodybuilder. In order to bridge this gap, experiments have been carried out on ambulances with the help of MIRA at its proving ground near Nuneaton. The ride in a recumbent position has been evaluated, resulting in a considerable improvement in the vertical direction. Further investigation is envisaged to relate the "objective" results obtained to the results of "subjective" tests. This is the only sure way of measuring the anti-vibration characteristics of the vehicle suspension and of the stretcher bed in relation to providing the most comfortable ride for a patient in the vertical, horizontal and transverse planes.
The teamwork
Without the assistance of progressive administrators and a virile spares section, progress in terms of adjusting to change would have been extremely difficult. This is a complex part of the organization and could well form the greater part of another article.
Without any reservations I wish to state that the success of this mammoth change is due entirely to teamwork. It would be invidious to single out any one person; the credit goes to every member of the team who have enjoyed accepting a motto, "What's one more problem?"