AEC Mercury/Scammel
Page 100
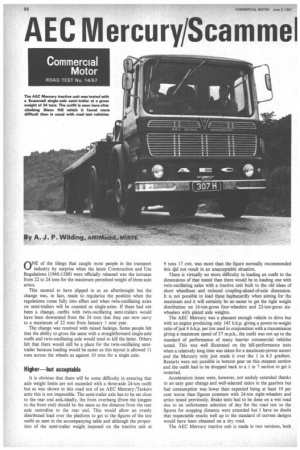
Page 101
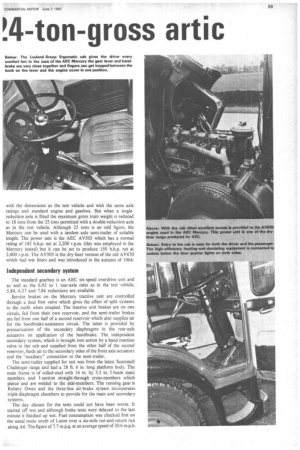
Page 102
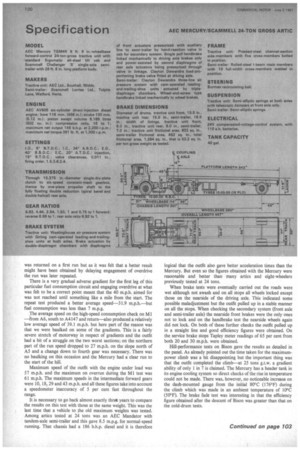
Page 105

If you've noticed an error in this article please click here to report it so we can fix it.
!4-ton-gross artic
ONE of the things that caught most people in the transport industry by surprise when the latest Construction and Use Regulations (1966:1288) were officially released was the increase from 22 to 24 tons for the maximum permitted weight of three-axle attics.
This seemed to have slipped in as an afterthought but the change was, in fact, made to regularize the position when the regulations come fully into effect and when twin-oscillating axles on semi-trailers will be counted as single-axles. If there had not been a change, outfits with twin-oscillating semi-trailers would have been downrated from the 24 tons that they can now carry to a maximum of 22 tons from January 1 next year.
The change was received with mixed feelings. Some people felt that the ability to gross the same with a straightforward single-axle outfit and twin-oscillating axle would tend to kill the latter. Others felt that there would still be a place for the twin-oscillating semitrailer because loading would be easier as this layout is allowed 11 tons across the wheels as against 10 tons for a single axle.
Higher—but acceptable
It is obvious that there will be some difficulty in ensuring that axle weight limits are not exceeded with a three-axle 24-ton outfit but as was shown in this road test of an AEC Mercury /Taskers artic this is not impossible. The semi-trailer axle has to be set close to the rear end and ideally, the front overhang (from the kingpin to the front end) should be the same as the distance from the rear axle centreline to the rear end. This would allow an evenly distributed load over the platform to get to the figures of the test outfit as seen in the accompanying table and although the proportion of the semi-trailer weight imposed on the tractive unit at 9 tons 17 cwt. was more than the figure normally recommended this did not result in an unacceptable situation.
There is virtually no more difficulty in loading an outfit to the dimensions of that tested than there would be in loading one with twin-oscillating axles with a tractive unit built to the old ideas of short wheelbase and reduced coupling-ahead-of-axle dimension. It is not possible to load these haphazardly when aiming for the maximum and it will certainly be no easier to get the right weight distribution on 16-ton-gross four-wheelers and 22-ton-gross sixwheelers with plated axle weights.
The AEC Mercury was a pleasant enough vehicle to drive but with an engine producing only 145 b.h.p. giving a power-to-weight ratio of just 6 b.h.p. per ton used in conjunction with a transmission giving a maximum speed of 57 m.p.h., the outfit was not up to the standard of performance of many heavier commercial vehicles tested. This was well illustrated on the hill-performance tests when a relatively long time was taken for a maximum-power ascent and the Mercury only just made it over the 1 in 6.5 gradient. Restarts were not possible in bottom gear on this steepest section and the outfit had to be dropped back to a 1 in 7 section to get it restarted.
Acceleration times were, however, not unduly extended thanks to an easy gear change and well-selected ratios in the gearbox but fuel consumption was lower than expected being at least 10 per cent worse than figures common with 24-ton eight-wheelers and artics tested previously. Brake tests had to be done on a wet road due to an unfortunate selection of day for the road test so the figures for stopping distance were extended but I have no doubt that respectable results well up to the standard of current designs would have been obtained on a dry road.
The AEC Mercury tractive unit is made in two versions, both with the dimensions as the test vehicle and with the same axle ratings and standard engine and gearbox. But when a singlereduction axle is fitted the maximum gross train weight is reduced to 18 tons from the 25 tons permitted with a double-reduction axle as in the test vehicle. Although 25 tons is an odd figure, the Mercury can be used with a tandem axle semi-trailer of suitable length. The power unit is the AEC AV505 which has a normal rating of 145 b.h.p. net at 2,200 r.p.m. (this was employed in the Mercury tested) but it can be set to produce 150 b.h.p. net at 2,400 r.p.m. The AV505 is the dry-finer version of the old AV470 which had wet liners and was introduced in the autumn of 1964.
Independent secondary system
The standard gearbox is an AEC six-speed overdrive unit and as well as the 6.92 to 1 rear-axle ratio as in the test vehicle, 5.84, 6.27 and 7.84 reductions are available.
Service brakes on the Mercury tractive unit are controlled through a dual foot valve which gives the effect of split systems to the outfit when coupled. The tractive unit brakes are on one circuit, fed from their own reservoir, and the semi-trailer brakes are fed from one half of a second reservoir which also supplies air for the handbrake-assistance circuit. The latter is provided by pressurization of the secondary diaphragms in the rear-axle actuators on application of the handbrake. The independent secondary system, which is brought into action by a hand reaction valve in the cab and supplied from the other half of the second reservoir, feeds air to the secondary sides of the front axle actuators and the "auxiliary" connection to the semi-trailer.
The semi-trailer supplied for test was from the latest Scammell Challenger range and had a 28 ft. 6 in. long platform body. The main frame is of rolled-steel with 16 in. by 5.5 in. I-beam main members and I-section straight-through cross-members which pierce and are welded to the side-members. The running gear is Rubery Owen and the three-line air-brake system incorporates triple-diaphragm chambers to provide for the main and secondary systems.
The day chosen for the tests could not have been worse. It started off wet and although brake tests were delayed to the last minute it finished up wet. Fuel consumption was checked first on the usual route south of Luton over a six-mile out-and-return run along A6. The figure of 7.7 m.p.g. at an average speed of 30.6 m.p.h. was returned on a first run but as it was felt that a better result might have been obtained by delaying engagement of overdrive the run was later repeated.
There is a very gradual adverse gradient for the first leg of this particular fuel consumption circuit and engaging overdrive at what was felt to be a correct point meant that the 40 m.p.h. aimed for was not reached until something like a mile from the start. The repeat test produced a better average speed-31.9 m.p.h.—but fuel consumption was less than 7 m.p.g.
The average speed on the high-speed consumption check on M1 —from A6, south to A4147 and return—also produced a relatively low average speed of 39.1 m.p.h. but here part of the reason was that we were baulked on some of the gradients. This is a fairly severe stretch of motorway in respect of gradients and the outfit had a bit of a struggle on the two worst sections; on the northern part of the run speed dropped to 27 m.p.h. on the slope north of A5 and a change down to fourth gear was necessary. There was no baulking on this occasion and the Mercury had a clear run to the start of the hill.
Maximum speed of the outfit with the engine under load was 57 m.p.h. and the maximum on overrun during the M1 test was 61 m.p.h. The maximum speeds in the intermediate forward gears were 10, 18, 29 and 43 m.p.h. and all these figures take into account a speedometer inaccuracy of 5 per cent fast throughout the range.
It.is necessary to go back almost exactly three years to compare the results on this test with those at the same weight. This was the last time that a vehicle to the old maximum weights was tested. Among attics tested at 24 tons was an AEC Mandator with tandem-axle semi-trailer and this gave 8.5 m.p.g. for normal-speed running, That chassis had a 186 b.h.p. diesel and it is therefore logical that the outfit also gave better acceleration times than the Mercury. But even so the figures obtained with the Mercury were reasonable and better than many attics and eight-wheelers previously tested at 24 tons.
When brake tests were eventually carried out the roads were wet although not awash and on all stops all wheels locked except those on the nearside of the driving axle. This indicated some possible maladjustment but the outfit pulled up in a stable manner on all the stops. When checking the secondary system (front axle and semi-trailer axle) the nearside front brakes were the only ones not to lock and on the handbrake test the nearside wheels again did not lock. On both of these further checks the outfit pulled up in a straight line and good efficiency figures were obtained. On the service brake stops Tapley meter readings of 65 per cent from both 20 and 30 m.p.h. were obtained.
Hill-performance tests on Bison gave the results as detailed in the panel. As already pointed out the time taken for the maximumpower climb was a bit disappointing but the important thing was that the outfit completed the climb—at 25 tons g.t.w. a gradient ability of only 1 in 7 is claimed. The Mercury has a header tank in its engine cooling system so direct checks of the rise in temperature could not be made. There was, however, no noticeable increase on the dash-mounted gauge from the initial 80°C (176°F) during the climb which was made in an ambient temperature of 10°C (50°F). The brake fade test was interesting in that the efficiency figure obtained after the descent of Bison was greater than that on the cold-drum tests.
Apart from the feeling that more power would have been desirable-the Mercury was found to be a pleasant vehicle to drive and very quiet even at maximum speed. Empty tests enabled the advantages of fitting load-proportioning equipment in the brake system to the driving axle to be assessed. This made for much more confidence when braking in the unladen condition but I think that it is desirable to have a light-laden valve at the semitrailer axle as well as at the driving axle. Reducing the brake effort at the driving axle is admittedly more important on the grounds of stability but trailer-axle locking when running light is much more common as evidenced by the marks left by semi-trailer tyres on the roads.
Favourable comments about the standard of comfort and trim in the Ergomatic cab have been published in other road test reports. Experience with the Mercury confirmed these although the clutch and brake felt a little heavy when taking over the vehicle initially. The handbrake lever and gear change knob come very close together in certain positions so a driver has to be careful of his left hand and I found it possible to trap my fingers between the knob and the engine cover in the first and reverse gear positions. Visibility is very good in the Ergomatic cab and now that the mirrors have been repositioned to lie as far forward as possible they pick up only the normal amount of spray in wet weather.
Like other models with the Ergomatic cab, the engine is completely accessible for maintenance when the cab is tilted forward and the time taken to complete the tilt is very small. Routine checks of water and oil can be carried out by raising the interior bonnet.
As tested the AEC Mercury tractive unit costs £3,121, this including the load-sensing valve and semi-trailer coupling and connections. The Scammell semi-trailer has a list price of £1,145 including spare wheel carrier.