Winning the war against rust
Page 22
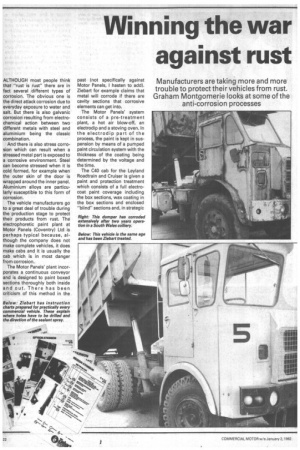
Page 23
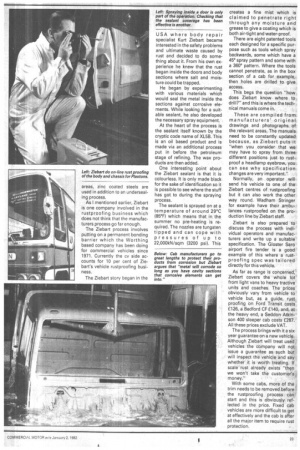
If you've noticed an error in this article please click here to report it so we can fix it.
Manufacturers are taking more and more trouble to protect their vehicles from rust. Graham Montgomerie looks at some of the anti-corrosion processes
ALTHOUGH most people think that "rust is rust" there are in fact several different types of corrosion. The obvious one is the direct attack corrosion due to everyday exposure to water and salt. But there is also galvanic corrosion resulting from electrochemical action between two different metals with steel and aluminium being the classic combination.
And there is also stress corrosion which can result when a stressed metal part is exposed to a corrosive environment. Steel can become stressed when it is cold formed, for example when the outer skin of the door is wrapped around the inner panel. Aluminium alloys are particularly susceptible to this form of corrosion.
The vehicle manufacturers go to a great deal of trouble during the production stage to protect their products from rust. The electrophoretic paint plant at Motor Panels (Coventry) Ltd is perhaps typical because, although the company does not make complete vehicles, it does make cabs and it is usually the cab which is in most danger from corrosion.
The Motor Panels' plant incorporates a continuous conveyor and is designed to paint boxed sections thoroughly both inside and out. There has been criticism of this method in the past (not specifically against Motor Panels, I hasten to add). Ziebart for example claims that metal will corrode if there are cavity sections that corrosive elements can get into.
The Motor Panels' system consists of a pre-treatment plant, a hot air blow-off, an electrodip and a stoving oven. In the electrodip part of the process, the paint is kept in suspension by means of a pumped paint circulation system with the thickness of the coating being determined by the voltage and the time.
The C40 cab for the Leyland Roadtrain and Cruiser is given a paint and protection treatment which consists of a full electrocoat paint coverage including the box sections, wax coating in the box sections and enclosed "blind" sections and, in strategic areas, zinc coated steels are used in addition to an undersealing process.
As I mentioned earlier, Ziebart is one company involved in the rustproofing business which does not think that the manufacturers process go far enough.
The Ziebart process involves putting on a permanent bonding barrier which the Worthing based company has been doing for commercial vehicles since 1971. Currently the cv side accounts for 10 per cent of Ziebart's vehicle rustp roofing business.
The Ziebart story began in the USA where body repair specialist Kurt Ziebart became interested in the safety problems and ultimate waste caused by rust and decided to do something about it. From his own experience he knew that the rust began inside the doors and body sections where salt and moisture could be trapped.
He began by experimenting with various materials which would seal the metal inside the sections against corrosive elements. While looking for a suitable sealant, he also developed the necessary spray equipment.
At the heart of the process is the sealant itself known by the cryptic code name of XL5B. This is an oil based product and is made via an additional process put in before the petroleum stage of refining. The wax products are then added.
One interesting point about the Ziebart sealant is that it is colourless. It is only made black for the sake of identification so it is possible to see where the stuff has got to during the spraying process.
The sealant is sprayed on at a temperature of around 29°C (85°F) which means that in the summer no pre-heating is required. The nozzles are tungsten tipped and can cope with pressures of up to 22,000kN/sqm (3200 psi). This creates a fine mist which is claimed to penetrate right through any moisture and grease to give a coating which is both air-tight and water-proof.
There are eight patented tools each designed for a specific purpose such as tools which spray backwards, some which have a 45° spray pattern and some with a 360° pattern. Where the tools cannot penetrate, as in the box section of a cab for example, then holes are drilled to give access.
This begs the question "how does Ziebart know where to drill?" and this is where the technical manuals come in.
These are compiled from manufacturers' original drawings and photographs of the relevant areas. The manuals need to be constantly updated because, as Ziebart puts it "when you consider that we may have to spray from three different positions just to rustproof a headlamp eyebrow, you can see why specification changes are very important."
Normally, an operator will send his vehicle to one of the Ziebart centres of rustproofing but it can also work the other way round. Wadham Stringer for example have their ambulances rustproofed on the production line by Ziebart staff.
Ziebart is also prepared to discuss the process with individual operators and manufacturers and write up a suitable specification, The Gloster Saro airport fire tender is a good example of this where a rustproofing spec was tailored directly for this vehicle.
As far as range is concerned, Ziebart covers the whole lot from light vans to heavy tractive units and coaches. The prices obviously vary from vehicle to vehicle but, as a guide, rust proofing on Ford Transit costs £126, a Bedford CF £140, and, at the heavy end, a Seddon Atkinson 400 sleeper cab costs £287. All these prices exclude VAT.
The process brings with it a six year guarantee on a new vehicle. Although Ziebart will treat used vehicles the company will not issue a guarantee as such but will inspect the vehicle and say whether it is worth treating. If scale rust already exists "then we won't take the customer's money," With some cabs, more of the trim needs to be removed before the rustproofing process can start and this is obviously reflected in the price. Fixed cab vehicles are more difficult to get at effectively and the cab is after all the major item to require rust protection.