Tippers travel a rocky road
Page 46
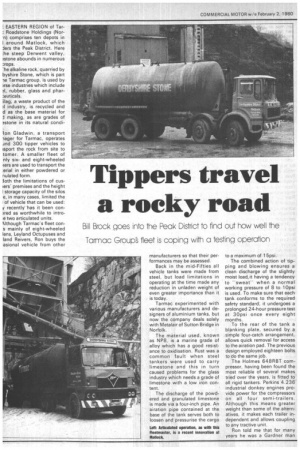
Page 47
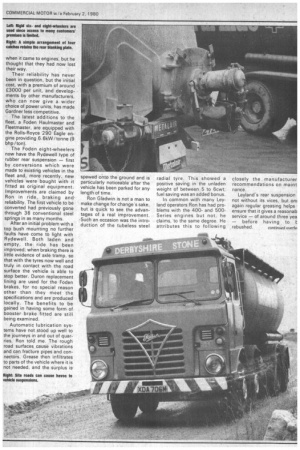
Page 48
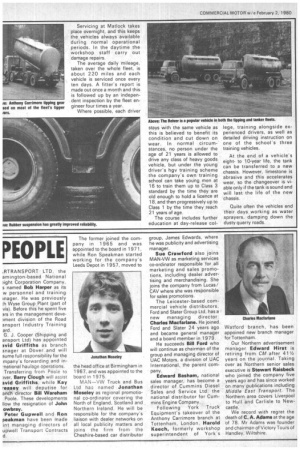
If you've noticed an error in this article please click here to report it so we can fix it.
Bill Brock goes into ne Peak District to find out now well Tarmac Group fleet is coping wH a testing operation
EASTERN REGION of TarRoadstone Holdings (Norn) comprises ten depots in I around Matlock, which Jers the Peak District. Here he steep Derwent valley, ;stone abounds in numerous 3rops.
The alkaline rock, quarried by byshire Stone, which is part le Tarmac group, is used by ;rse industries which include ;l, rubber, glass and phar;euticals.
ilag, a waste product of the ;I industry, is recycled and d as the base material for J making, as are grades of .stone in its natural condi ion Gladwin, a transport lager for Tarmac, operates _Ind 300 tipper vehicles to isport the rock from site to tomer. A smaller fleet of nly sixand eight-wheeled 3oth the limitations of cusiers" premises and the height I storage capacity of the silos e, in many cases, limited the of vehicle that can be used: recently has it been con;red as worthwhile to intro:e two articulated units. Ithough Tarmac's fleet cons mainly of eight-wheeled lens, Leyland Octupuses and land Reivers, Ron buys the asional vehicle from other manufacturers so that their performances may be assessed. Back in the mid-Fifties all vehicle tanks were made from steel, but load limitations in operating at the time made any reduction in unladen weight of even greater importance than it is today. Tarmac experimented with various manufacturers and designers of aluminium tanks, but now the company deals solely with Metalair of Sutton Bridge in Norfolk. The material used, known as NP8, is a marine grade of alloy which has a good resistance to oxidisation. Rust was a common fault when steel tankers were used to carry limestone and this in turn caused problems for the glass industry which needs a grade of limestone with a low iron content. The discharge of the powdered and granulated limestone is made via a four-inch pipe. An airation pipe contained at the base of the tank serves both to loosen and pressurise the cargo to a maximum of 15psi. The combined action of tipping and blowing ensures a clean discharge of the slightly moist load, it having a tendency to "sweat'' when a normal working pressure of 8 to 10psi is used. To make sure that each tank conforms to the required safety standard, it undergoes a prolonged 24-hour pressure test at 30psi once every eight months. To the rear of the tank a blanking plate, secured by a simple four-catch arrangement, allows quick removal for access to the airation pad. The previous design employed eighteen bolts to do the same job. The Holmes 648RBT compressor, having been found the most reliable of several makes tried over the years, is fitted to all rigid tankers. Perkins 4.236 industrial donkey engines provide power for the compressors on all four semi-trailers. Although this means greater weight than some of the alternatives, it makes each trailer independent and allows coupling to any tractive unit. Ron told me that for many years he was a Gardner man when it came to engines, but he thought that they had now lost their way. Their reliability has never been in question, but the initial cost, with a premium of around, £3000 per unit, and developments by other manufacturers, who can now give a wider choice of power units, has made Gardner less competitive. The latest additions to the fleet, a Foden Haulmaster and Fleetmaster, are equipped with the Rolls-Royce 290 Eagle engine providing 6.6kW/tonne (9 bhp/ton). The Foden eight-wheelers now have the Rydewell type of rubber rear suspension — first by conversions which were made to existing vehicles in the fleet and, more recently, new vehicles were bought with it fitted as original equipment. Improvements are claimed by Ron in ride, braking and reliability. The first vehicle to be converted had previously gone through 36 conventional steel springs in as many months. After an initial problem with a top bush mounting no further faults have come to light with Rydewell. Both laden and empty, the ride has been improved; when braking there is little evidence of axle tramp, so that with the tyres now well and truly in contact with the road surface the vehicle is able to stop better. Duron replacement lining are used for the Foden brakes, for no special reason other than they meet the specifications and are produced locally. The benefits to be gained in having some form of booster brake fitted are still being examined. Automatic lubrication systems have not stood up well to the journeys in and out of quarries, Ron told me. The rough road surfaces cause vibrations and can fracture pipes and connectors. Grease then infiltrates to parts of the vehicle where it is not needed, and the surplus is spewed onto the ground and is particularly noticeable after the vehicle has been parked for any length of time. Ron Gladwin is not a man to make change for change's sake, but is quick to see the advantages of a real improvement. -Such an occasion was the introduction of the tubeless steel radial tyre. This showed a positive saving in the unladen weight of between 5 to 6cwt; fuel saving was an added bonus. In common with many Leyland operators Ron has had problems with the 400and 500Series engines but not, he claims, to the same degree. He attributes this to following closely the manufacturer recommendations on maint nance. Leyland's rear suspension not without its vices, but on again regular greasing helps • ensure that it gives a reasonab service — of around three yea — before having to t rebushed. continued overie. Servicing at Matlock takes place overnight, and this keeps the vehicles always available during normal operational periods. In the daytime the workshop staff carry out damage repairs. The average daily mileage, taken over the whole fleet, is about 220 miles and each vehicle is serviced once every ten days. A fitter's report is made out once a month and this is followed up by an independent inspection by the fleet engineer four times a year. Where possible, each driver stays with the same vehicle as this is believed to benefit its condition and cut down on wear. In normal circumstances, no person under the age of 21 years is allowed to drive any class of heavy goods vehicle, but under the young driver's hgv training scheme the company's own training school can take young men at 16 to train them up to Class 3 standard by the time they are old enough to hold a licence at 18, and then progressively up to Class 1 by the time they reach 21 years of age. The course includes further education at day-release col lege, training alongside experienced drivers, as well as detailed driving instruction on one of the school's three training vehicles. At the end of a vehicle's eightto 10-year life, the tank can be transferred to a new chassis. However, limestone is abrasive and this accelerates wear, so the changeover is viable only if the tank is sound and will last the life of the new chassis. Quite often the vehicles end their days working as water sprayers, damping down the dusty quarry roads.