Each tanker gets 25 safety cheeks
Page 51
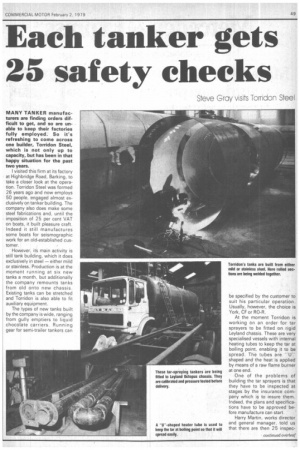
Page 52
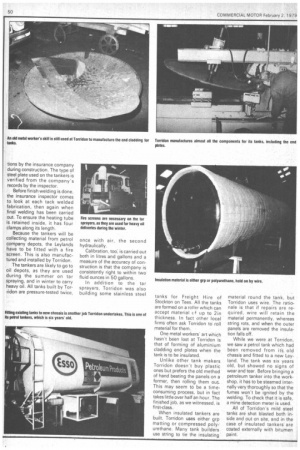
If you've noticed an error in this article please click here to report it so we can fix it.
MANY TANKER manufacturers are finding orders difficult to get, and so are unable to keep their factories fully employed. So it's refreshing to come across one builder, Torridon Steel, which is not only up to capacity, but has been in that happy situation for the past two years.
I visited this firm at its factory at Highbridge Road, Barking, to take a closer look at the operation. Torridon Steel was formed 26 years ago and now employs 50 people, engaged almost exclusively on tanker building. The company also does make some steel fabrications and, until the imposition of 25 per cent VAT on boats, it built pleasure craft. Indeed it still manufactures some boats for seismographic work for an old-established customer.
However, its main activity is still tank building, which it does exclusively in steel — either mild or stainless. Production is at the moment running at six new tanks a month, but additionally the company remounts tanks from old onto new chassis. Existing tanks can be stretched and Torridon is also able to fit auxiliary equipment.
The types of new tanks built by the company is wide, ranging from gully emptiers to liquid chocolate carriers. Running gear for semi-trailer tankers can be specified by the customer to suit his particular operation. Usually, however, the choice is York, CF or RO-R.
At the moment Torridon is working on an order for tar sprayers to be fitted on rigid Leyland chassis, These are very specialised vessels with internal heating tubes to keep the tar at boiling point, enabling it to be spread. The tubes are shaped and the heat is applied by means of a raw flame burner at one end.
One of the problems of building the tar sprayers is that they have to be inspected at stages by the insurance company which is to insure them. Indeed, the plans and specifications have to be approved before manufacture can start.
Harry Martin, works director and general manager, told us that there are then 25 inspec tions by the insurance company during construction. The type of steel plate used on the tankers is verified from the company's records by the inspector.
Before finish welding is done, the insurance inspector comes to look at each tack welded fabrication, then again when final welding has been carried Out. To ensure the heating tube is retained inside, it has four clamps along its length.
Because the tankers will be collecting material from petrol company depots, the Leylands have to be fitted with a fire screen. This is also manufactured and installed by Torridon.
The tankers are likely to go to oil depots, as they are used during the summer on tar spraying, and in winter to carry heavy oil. All tanks built by Tornclon are pressure-tested twice,
once with air, the second hydraulically.
Calibration, too; is carried out both in litres and gallons and a measure of the accuracy of construction is that the company is consistently right to within two fluid ounces in 50 gallons.
In addition to the tar sprayers, Torridon was also building some stainless steel tanks for Freight Hire of Stockton on Tees. All the tanks are formed on a roller which can accept material cf up to 2in thickness. In fact other local firms often ask Torridon to roll material for them.
One metal workers art which hasn't been lost at Torridon is that of forming of aluminium cladding end plates when the tank is to be insulated.
Unlike other tank makers Torridon doesn't buy plastic ones but prefers the old method of hand beating the panels on a former, then rolling them out. This may seem to be a timeconsuming process, but in fact takes little over half an hour, The finished job, as we witnessed, is first-class.
When insulated tankers are built, Torridon uses either grp matting or compressed polyurethane. Many tank builders use string to tie the insulating material round the tank, but Torridon uses wire. The rationale is that if repairs are required, wire will retain the material permanently, whereas string rots, and when the outer panels are removed the insulation falls off.
While we were at Torridon, we saw a petrol tank which had been removed from it old chassis and fitted to a new Leyland. The tank was six years old, but showed no signs of wear and tear. Before bringing a petroleum tanker into the workshop, it has to be steamed internally very thoroughly so that the fumes won't be ignited by the welding. To check that it is safe, a mine detection meter is used.
All of Torridon's mild steel tanks are shot blasted both inside and out on site, and in the case of insulated tankers are coated externally with bitumen paint.