Injection pressures of more than 2.000 bar put big demands
Page 60
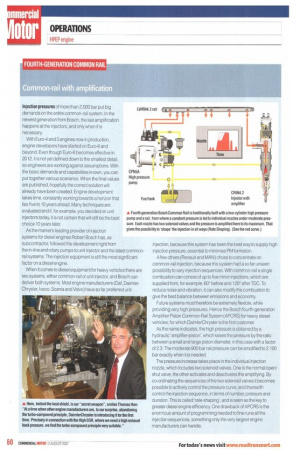
If you've noticed an error in this article please click here to report it so we can fix it.
on the entire common-rail system. In the newest generation from Bosch, the last amplification happens at the injectors, and only when it is necessary.
With Euro-4 and 5 engines now in production, engine developers have started on Euro-6 and beyond. Even though Euro-6 becomes effective in 2012, it is not yet defined down to the smallest detail. so engineers are working against assumptions. With the basic demands and capabilities known, you can put together various scenarios. When the final values are published, hopefully the correct solution will already have been created. Engine development takes time, constantly working towards a horizon that lies five to 10 years ahead. Many techniques are evaluated and if, for example, you decided on unit injectors today, it is not certain that will still be the best choice 10 years later.
As the market's leading provider of injection systems for diesel engines Robert Bosch has, as subcontractor, followed the development right from the in-line and rotary pumps to unit injector and the latest commonrail systems. The injection equipment is still the most significant factor on a diesel engine.
When it comes to diesel equipment for heavy vehicles there are two systems, either common-rail or unit injector, and Bosch can deliver both systems. Most engine manufacturers (Daf, DaimlerChrysler, Iveco, Scania and Volvo) have so far preferred unit injection, because this system has been the best way to supply high injection pressure, essential to minimise PM formation.
A few others (Renault and MAN) chose to concentrate on common-rail injection, because this system had a so far unseen possibility to vary injection sequences. With common-rail a single combustion can consist of up to five minor injections, which are supplied from, for example, 60° before and 120' after TDC. To reduce noise and vibration, it can also modify the combustion to give the best balance between emissions and economy.
Future systems must therefore be extremely flexible, while providing very high pressures. Hence the Bosch fourth-generation Amplifier Piston Common-Rail System (APCRS) for heavy diesel vehicles, for which DaimlerChrysler is the first customer.
As the name indicates, the high pressure is obtained by a hydraulic 'amplifier-piston', which raises the pressure by the ratio between a small and large piston diameter, in this case with a factor of 2.3. The moderate 900 bar rail pressure can be amplified to 2,100 bar exactly when it is needed.
The pressure increase takes place in the individual injection nozzle, which includes two solenoid valves. One is the normal open/ shut valve, the other activates and deactivates the amplifying. By co-ordinating the sequences of the two solenoid valves it becomes possible to actively control the pressure curve, and therewith control the injection sequence, in terms of number, pressure and duration. This is called 'rate-shaping', and is seen as the key to greater diesel engine efficiency. One drawback of APCRS is the enormous amount of programming needed to fine-tune all the injection sequences, something only the very largest engine manufacturers can handle.