Transport depot design 1
Page 55
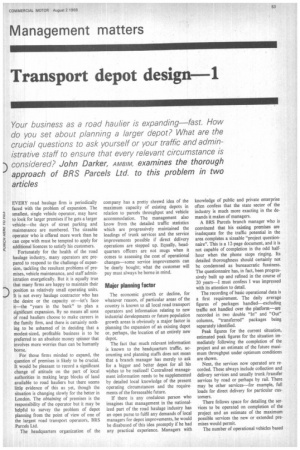
Page 56
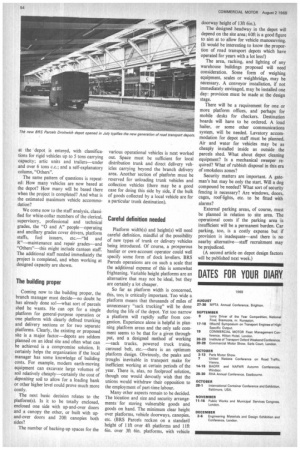
If you've noticed an error in this article please click here to report it so we can fix it.
Your business as a road haulier is expanding fast. How do you set about planning a larger depot? What are the crucial questions to ask yourself or your traffic and administrative staff to ensure that every relevant circumstance is
) considered? John Darker, AMBIM, examines the thorough approach of BRS Parcels Ltd. to this problem in two articles
EVERY road haulage firm is periodically faced with the problem of expansion. The smallest, single vehicle operator, may have to look for larger premises if he gets a larger vehicle—the days of street parking and maintenance are numbered. The sizeable operator who is offered more work than he can cope with must be tempted to apply for additional licences to satisfy his customers.
Fortunately for the health of the road haulage industry, many operators are prepared to respond to the challenge of expansion, tackling the resultant problems of premises, vehicle maintenance, and staff administration energetically. But it is equally true that many 'firms are happy to maintain their position as relatively small operating units. It is not every haulage contractor who has the desire or the capacity or—let's face it—the "years in the bank" to plan a significant expansion. By no means all sons of road hauliers choose to make careers in the family firm, and there is certainly nothing to be ashamed of in deciding that a modest-sized, profitable business is to be preferred to an absolute money spinner that involves more worries than can be humanly borne.
For those firms minded to expand, the question of premises is likely to be crucial. It would be pleasant to record a significant change of attitude on the part of local authorities in making large blocks of land available to road hauliers but there seems little evidence of this as yet, though the situation is changing slowly for the better in London. The obtaining of premises is the responsibility of the operator but it may be helpful to survey the problem of depot planning from the point of view of one of the largest road transport operators, BRS Parcels Ltd.
The headquarters organization of the company has a pretty shrewd idea of the maximum capacity of existing depots in relation to parcels throughput and vehicle accommodation. The management also know from the detailed traffic statistics which are progressively maintained the loadings of trunk services and the service improvements possible if direct delivery operations are stepped up. Equally, headquarters officers are not mugs when it comes to assessing the cost of operational changes—some service improvements can be dearly bought; what the customer will pay must always be borne in mind.
Major planning factor
The economic growth or decline, for whatever reason, of particular areas of the country is known to all local road transport operators and information relating to new industrial developments or future population growth areas is obviously a major factor in planning the expansion of an existing depot or, perhaps, the location of an entirely new depot.
The fact that much relevant information is known to the headquarters traffic, accounting and planning staffs does not mean that a branch manager has merely to ask for a bigger and better depot for all his wishes to be realized! Centralized management information needs to be supplemented by detailed local knowledge of the present operating circumstances and the requirements of the foreseeable future.
If there is any credulous person who imagines that management in the nationalized part of the road haulage industry has an open purse to fulfil any demands of local managers for depot improvements, he would be disabused of this idea promptly if he had any practical experience. Managers with knowledge of public and private enterprise often confess that the state sector of the industry is much more exacting in the demands it makes of managers.
A BRS Parcels branch manager who is convinced that his existing premises are inadequate for the traffic potential in the area completes a sizeable "project questionnaire". This is a 12-page document, and it is not capable of completion in the odd halfhour when the phone stops ringing. Its detailed thoroughness should certainly not be condemned as bureaucratic fussiness. The questionnaire has, in fact, been progressively built up and refined in the course of 20 years—I must confess I was impressed with its attention to detail.
The recording of basic operational data is a first requirement. The daily average figures of packages handled—excluding traffic not handled over the platform—are recorded in two double "In" and "Out" columns, "transferred" packages being separately identified.
Peak figures for the current situation, estimated peak figures for the situation immediately following the completion of the project and an estimate of the future maximum throughput under optimum conditions are shown.
Next, the services now operated are recorded. These always include collection and delivery services and usually trunk /transfer services by road or perhaps by rail. There may be other services—for example, full loads for direct delivery for particular customers.
There follows space for detailing the services to be operated on completion of the project and an estimate of the maximum possible services the new or extended premises would permit.
The number of operational vehicles based at the depot is entered, with classifications for rigid vehicles up to 5 tons carrying capacity; artic units and trailers—under and over 6 tons c.c.; and a self-explanatory column, "Others".
The same pattern of questions is repeated: How many vehicles are now based at the depot? How many will be based there when the project is completed? And what is the estimated maximum vehicle accommodation?
We come now to the staff analysis, classified for white-collar members of the clerical. supervisory, professional and technical grades, the "0 and A" people—operating and ancillary grades cover drivers, platform staffs, fuel issuers, etc.—"M and R"—maintenance and repair grades—and "Others"—this might include canteen staff. The additional staff needed immediately the project is completed, and when working at designed capacity are shown.
The building proper Coming now to the building proper, the branch manager must decide—no doubt he has already done so!—what sort of parcels shed he wants. He can opt for a single platform for general-purpose operation or one platform with clearly defined trun king and delivery sections or for two separate platforms. Clearly, the existing or proposed site is a major factor—depots are seldom planned on an ideal site and often what can be achieved is a compromise solution. It certainly helps the organization if the local manager has some knowledge of building costs. For example, modern earth-moving equipment can excavate large volumes of soil relatively cheaply—certainly the cost of depositing soil to allow for a loading bank or other higher level could prove much more costly.
The next basic decision relates to the platform(s). Is it to be totally enclosed, enclosed one side with up-and-over doors and a canopy the other, or built with up and-over doors and 20ft canopies both sides?
The number of backing-up spaces for the various operational vehicles is next worked out. Space must be sufficient for local distribution trunk and direct delivery vehicles carrying beyond the branch delivery area. Another section of platfoim must be reserved for unloading trunk vehicles and collection vehicles (there may be a good case for doing this side by side, if the bulk of goods collected by a local vehicle are for a particular trunk destination).
Careful definition needed
Platform width(s) and height(s) will need careful definition, mindful of the possibility of new types of trunk or delivery vehicles being introduced. Of course, a prosperous haulier or own-account operator could well specify some form of dock levellers. BRS Parcels operations are on such a scale that the additional expense of this is somewhat frightening. Variable height platforms are an alternative that may not be ideal, but they are certainly a lot cheaper.
So far as platform width is concerned, this, too; is critically important. Too wide a platform means that thousands of miles of unnecessary "sack trucking" will be done during the life of the depot. Yet too narrow a platform will rapidly suffer from congestion. Experience alone is helpful in planning platform areas and the only safe comment seems to be that for a given throughput, and a designed method of working —sack trucks, powered truck trains, carousel belt, etc.—there is an optimum platform design. Obviously, the peaks and troughs inevitable in transport make for inefficient working at certain periods of the year. There is, alas, no foolproof solution, though one would devoutly wish that the unions would withdraw their opposition to the employment of part-time labour.
Many other aspects remain to be decided. The location and size and security arrangements for storing vulnerable goods and goods on hand. The minimum clear height over platforms, vehicle doorways, canopies, etc. (BRS Parcels reckon on a standard height of lift over 4ft platforms and lift 6in. over 3ft 6in. platforms, with vehicle doorway height of I3ft 6in.).
The designed headway in the depot will depend on the site area; 60ft is a good figure to aim at to allow for vehicle manoeuvring. (It would be interesting to know the proportion of road transport depots which have operated for years with a lot less!) The area, racking, and lighting of any warehouse buildings proposed will need consideration. Some form of weighing equipment, scales or weighbridge, may be necessary. A conveyor installation, if not immediately envisaged, may be installed one day: provision must be made at the design stage.
There will be a requirement for one or more platform offices, and perhaps for mobile desks for checkers. Destination boards will have to be ordered. A loud hailer, or some other communications system, will be needed. Lavatory accommodation for depot staff must be planned. Air and water for vehicles may be as cheaply installed inside as outside the parcels shed. What about depot cleaning equipment? Is a mechanical sweeper required? What of rubbish disposal in this era of smokeless zones?
Security matters are important. A gateman's hut may be only the start. Will a dog compound be needed? What sort of security fencing is necessary? Are windows, doors, cages, roof-lights, etc. to be fitted with alarms?
External parking areas, of course, must be planned in relation to site area. The operational costs if the parking area is insufficient will be a permanent burden. Car parking, too, is a costly expense but if provision is inadequate—and there is no nearby alternative—staff recruitment may be prejudiced.
(A second article on depot design factors will be published next week.)