Is AUTOMATIC
Page 28
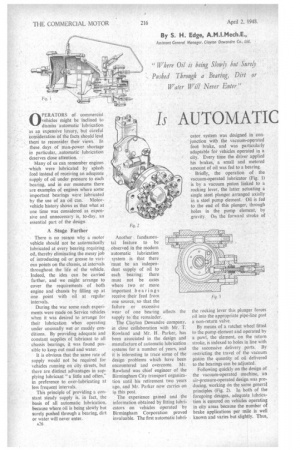
Page 29
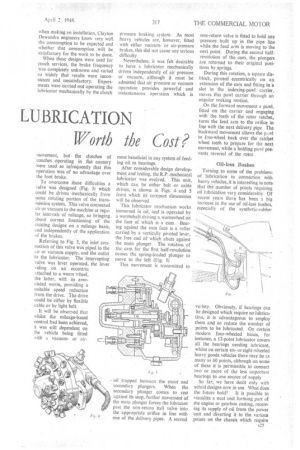
Page 30
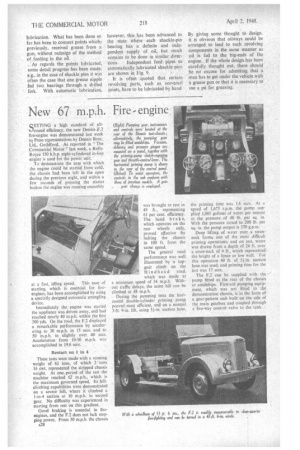
If you've noticed an error in this article please click here to report it so we can fix it.
LUBRICATION
Vorth the Cost?
OPERATORS of commercial vehicles might be inclined to dismiss automatic lubrication as an expensive luxury, but careful consideration Of the facts should lead thern to reconsider their views.. In these. days of man-power shortage• in particular, ,automatic lubrication deserves close attention.
• Many of us can remember engines .which were lubricated by splash feed instead of receiving an adequate supply of oil under pressure to each bearing, and in our museums there are examples of engines where some important bearings were lubricated
by the use of an oil can. Motorvehicle history shows us that what at one time was considered as expensive and unnecessary is, to-day, an essential part of the design.
A Stage Farther
There is no reason why a motor vehicle should not be automatically lubricated at every bearing requiring oil, thereby eliminating the messy job of introducing oil or grease to various points on the chassis, at intervals throughout the life of the vehicle. Indeed, the idea can be carried farther, and we might arrange to cover the requirements of both engine and chassis by filling up at one point with oil at regular intervals.
During the war some such experiments were made on Service vehicles when it was desired to arrange for their lubrication when operating under unusually wet or muddy conditions. By providing adequate and constant supplies of lubricant to all chassis bearings, it was found pos.sible to keep out mud and water.
It is obvious that the same rate of supply would not be required for vehicles running on city streets, but there are distinct advantages in supplying lubricant "a little and often," in preference to over-lubricating at less frequent intervals.
This principle of providing a constant steady supply is, in fact, the basis of all automatic lubrication. because where oil is being slowly but surely pushed through a bearing, dirt or water will never enter.
A26
Another fundamental feature to be observed in the modern automatic lubrication system is that there 'must be an -independent supply of oil to each bearing; there must not be cases where two or more important bearings receive their feed from one source, so that the failure or excessive wear of one bearing affects the supply to the remainder.
The Clayton Dewandre company, in close collaboration with Mr. T. Rowland and Mr. H. Parker, has been associated in the design and manufacture of automatic lubrication systems for a number of years, and it is interesting to trace some of the design problems which have been encountered and overcome. Mr. Rowland was chief engineer of the Birmingham City transport organization until his retirement two years ago, and Mr. Parker now carries on in this post.
The experience gained and the information obtained by fitting lubricators on vehicles operated by Birmingham Corporation proved invaluable. The first automatic lubri cator system was designed in conjunction with the vacuum-operated foot brake, and was particularly adaptable for vehicles operated in a city. Every time the driver applied his brakes, a small and metered amount of oil was fed to a bearing.
Briefly, the operation of the vacuum-operated lubricator (Fig. 1) is by a vacuu.m piston linked to a rocking lever, the latter actuating a single steel plunger arranged axially in a steel pump element. Oil is fed to the end of this plunger, through holes in the pump element, by gravity. On the forward stroke of the rocking lever this plunger forces oil into the appropriate pipe-line past a non-return valve.
By means_ of a ratchet wheel fitted to the pump element and operated by a pawl, the element, on the return stroke, is indexed to holes in line with the • successive delivery ports. By restricting the travel of the vacuum piston the quantity of oil delivered to the bearings can be adjusted.
Following quickly on the design of the vacuum-operated machine, an air-pressure-operated design was producing, working On the same general principles (Fig. 2). In both of the foregoing designs, adequate lubrication is ensured on vehicles operating in city areas because the number of brake applications per mile is well known and varies but slightly. Thus,
when making an installation, Clayton Dewandre engineers know very well the consumption to be expected and whether that consumption will be, satisfactory for the work to be done.
When these designs were used for coach services, the brake frequency was completely unknown and varied so widely that results were inconsistent and unsatisfactory. Experiments were carried out operating the lubricator mechanically by the clutch 'movement, but the clutches of coaches operating in flat country were used so infrequently that this operation was of no advantage over the foot brake.
To overcome these difficulties a valve was designed (Fig. 3) which could be driven mechanically from some rotating portion of the transMission system. This valve connected air or vacuum to the machine at regular intervals of mileage, so bringing about correct functioning of the existing designs on a mileage basis, and independently of the application of the brakes.
Referring to Fig. 3, the inlet connection of this valve was piped to the air or vacuum supply, and the outlet to the lubricator, The interrupting valve was lever operated, the lever iding on an eccentric attached to a worm wheel, the latter, with its associated worm, providing a suitable speed reduction from the drive. The drive could be either by flexible cable or by light belt.
It will be observed that whilst the mileage-based control had been achieved, it was still dependent on the vehicle being fitted with a vacuumor air
pressure braking system. As most heavy vehicles are, however, fitted with either vacuumor air-pressure brakes, this did not cause any serious d ifficulty Nevertheless, it was felt desirable to have a lubricator mechanically driven independently of air pressure or vacuum, although it Must be admitted that air pressure or vacuum operation provides powerful and instantaneous operation which is most beneficial in any system of feeding oil to bearings.
After considerable design development and testing, the R.P. mechanical lubricator was evolved. This unit, which can be either belt or cable driven, is shown in Figs. 4 and 5 from which its compact dimensions will be observed This lubricator mechanism works immersed in oil, and is operated by a wormshaft driving a wormwheel on the face of which is a cam. • Bearing against the cam face is a roller carried by a vertically pivoted lever, the free end of which abuts against the main plunger. The rotation of the cam for the first half-revolution causes the spring-loaded plunger to move to the left (Fig. 5) This movement is transmitted to
oil trapped between the mainand secondary plungers. When the secondary plunger comes to rest against its stop, further movement of the main plunger forces the lubricant past the non-return ball valve into the appropriate orifice in line with one of the delivery pipes. A Second
non-return valve is fitted to hold any pressure built up in the pipe line while the -feed arm is moving to the next point. During the second halfrevolution of the cam, the plungers are returned to their Original positions by springs.
During this rotation, a square die block, pivoted eccentrically on an extension of the cam and fitting in a slot in the indexing-pawl carrier, moves this pawl carrier through an angular rocking motion.
On the forward movement a pawl, fitted on the carrier and engaging with the teeth of the rotor ratchet, turns the feed arm to the orifice in line with the next delivery pipe The backward movement allows the pi,w1 to free-wheel back over the ratekiet wheel teeth to prepare for the next movement, while a holding pawl prevents reversal of the rotor.
Oil-less Bushes
Turning to some of the problems of lubrication in connection with heavy vehicles, it is interesting to note that the number of points requiring oil lubrication vary considerably. Of recent years there has been a big increase in the use of oil-less bushes, especially of the synthetic-rubber
variety. Obviously, if bearings can be designed which require no lubrication, it is advantageous to employ them and so reduce the number of points to be lubricated On certain modern four-wheeled buses, for instance, a 12-point lubricator covers all the bearings needing lubricant, whilst on certain sixor eight-wheeled heavy goods vehicles there may be as many as 60 points, although on some of these it is permissible to connect two or more of the less important bearings to one source of supply So far, we have dealt only with actual designs now in use. What does the future hold? It is possible to visualize a neat unit forming part of the engine or gearbox casting, receiving its supply of oil from the power unit and diverting it to the various points on the chassis which require lubrication. What has been done so far has been to connect points which; previously, received grease from a gun, without redesign of the method of. feeding in the oil.
,..As regards the points lubricated, some detail progress has been made; e.g., in the case of shackle pins it was often the case that one grease nipple fed two bearings through a drilled link. With automatic lubrication. however, this has been advanced to the state. where each shackle-pin bearing has a definite and independent supply of oil, but much 'mains to be done in similar direc tions.Independent feed pipes to automatically lubricated shackle pins are shown in Fig. 9.
It is often quoted that certain revolving parts, such as 'universal joints, have to be lubricated by hand. By giving some thought to design. it is obvious that oilways could be arranged to lead to such revolving components in the same manner as oil is fed to the big-ends of the engine. If the whole design has been carefully thought out, there should be no excuse for admitting that a man has to get under the vehicle with a grease gun or that it is necessary to use a pit for greasing.