WORKSHOP CONFERENCE REPORT
Page 20
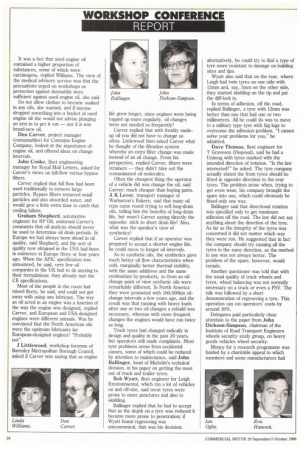
If you've noticed an error in this article please click here to report it so we can fix it.
It was a fact that used engine oil contained a higher proportion of substances, some of which were carcinogens, replied Williams. The view of the medical advisory service was that the precuations urged on workshops as protection against dermatitis were sufficient against used engine oil, she said.
Do not allow clothes to become soaked in any oils, she warned, and if anyone dropped something into a bucket of used engine oil she would not advise plunging an arm in to get it out — nor if it was brand-new oil.
Don Carver, project manager (consumables) for Cummins Engine Company, looked at the importance of engine oil, and offered ideas on change intervals.
John Cooke, fleet engineering manager for Royal Mail Letters, asked for Carver's views on full-flow versus bypass filters.
Carver replied that full flow had been used traditionally to remove large particles. Bypass filters removed small particles and also absorded water, and would give a little extra time to catch that cooling failure.
Graham Shepherd, automotive engineer for BP Oil, endorsed Carver's comments that oil analysis should never be used to determine oil drain periods. In Europe we had always been ahead in oil quality, said Shepherd, and the sort of quality now obtained in the USA had been in existence in Europe three or four years ago. When the APIC specification was announced, he said, very few oil companies in the UK had to do anyting to their formulations: they already met the CE specifications.
Most of the people in the room had mixed fleets, he said, and could not get away with using one lubricant. The way an oil acted in an engine was a function of the way the engine was designed, replied Carver, and European and USA-designed engines were different animals. Was he convinced that the North American oils were the optimum lubricants for European-designed engines? "Probably not".
Littlewood, workshop foreman of Barnsley Metropolitan Borough Council, asked if Carver was saying that as engine
life grew longer, since engines were being topped up more regularly, oil changes were not needed so frequently?
Carver replied that with freshly madeup oil you did not have to change so often. Littlewood then asked Carver what he thought of the filtration system whereby an extra filter change was made instead of an oil change. From his perspective, replied Carver, filters were strainers — they didn't take out the contaminated oil molecules.
Often the cheapest thing the operator of a vehicle did was change the oil, said Carver: much cheaper than buying parts. A K Lever, transport manager of Warburton's Bakery, said that many oil reps came round trying to sell long-drain oils, telling him the benefits of long drain life, but wasn't Carver saying directly the opposite: stick to short drain life? Also, what was the speaker's view of synthetics?
Carver replied that if an operator was prepared to accept a shorter engine life, he could move to longer oil intervals.
As to synthetic oils, the synthetics gave much better oil flow characteristics when cold, marginally better thermal stability, with the same additives and the same combustion by-products, so from an oilchange point of view synthetic oils were remarkably different. In North America they were promoted with 160,000km oilchange intervals a few years ago, and the result was that running with heavy loads after one or two oil changes a rebuild was necessary, whereas with more frequent changes the engines would have run twice as long.
Truck tyres had changed radically in design and quality in the past 20 years, but operators still made complaints. Most tyre problems arose from accidental causes, some of which could be reduced by attention to maintenance, said John Ballinger, head of Michelin's technical division, in his paper on getting the most out of truck and trailer tyres.
Bob Wyatt, fleet engineer for Leigh Environmental, which ran a lot of vehicles on and off-site, said recut tyres were prone to more punctures and also to skidding.
Ballinger replied that he had to accept that as the depth on a tyre was reduced it became more prone to penetration; if Wyatt found regrooving was uneconomical, that was his decision: alternatively, he could try to find a type of tyre more resistant to damage on building sites and tips.
Wyatt also said that on the rear, where Leigh had twin tyres on one side with 12inm and, say, 5mm on the other side, they started skidding on the tip and put the diff-lock in.
In terms of adhesion, off the road, replied Ballinger, a tyre with 12mm was better than one that had one or two millimetres. All he could do was to move to a military type tyre with big lugs to overcome the adhesion problem. "I cannot solve your problems for you," he admitted.
Dave Thomas, fleet engineer for T Graveson (Disposal), said he had a Unimog with tyres marked with the intended direction of rotation. "Is the law interested?" he asked. The tyre company actually stated the front tyres should be fitted in opposite direction to the rear tyres. The problem arose when, trying to get even wear, his company brought the spare into use, which could obviously be fitted only one way.
Ballinger said that directional rotation was specified only to get maximum adhesion off the road. The taw did not say anything about the direction of the tyre. As far as the integrity of the tyres was concerned it did not matter which way they were run. He suggested that in fact the company should try running all the tyres in the same direction, as the method in use was not always better. The problem of the spare, however, would remain.
Another questioner was told that with the usual quality of truck wheels and tyres, wheel balancing was not normally necessary on a truck or even a PSV. The talk was followed by a short demonstration of regrooving a tyre. This operation can cut operators' costs by around 30%.
Delegates paid particularly close attention to the paper from John Dickson-Simpson, chairman of the Institute of Road Transport Engineers wheels security study group, on heavy goods vehicles wheel security.
Money for a research programme was funded by a charitable appeal to which members and some manufacturers had