Bill Brock looks around at the Market Harborough-based heavy trailer and public sector equipment manufacturer
Page 70
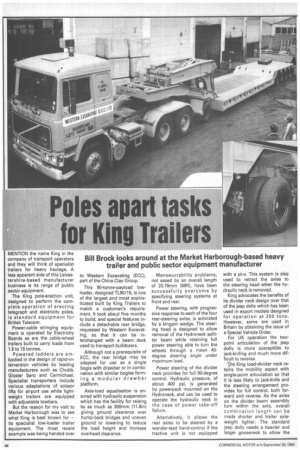
Page 71
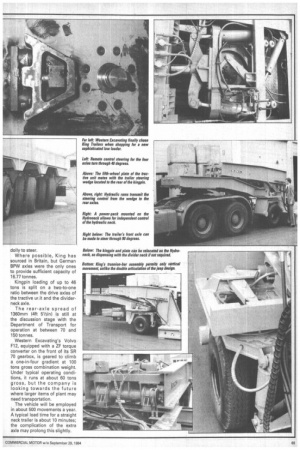
If you've noticed an error in this article please click here to report it so we can fix it.
MENTION the name King in the company of transport operators and they will think of specialist trailers for heavy haulage. A less apparent side of this Leicestershire-based manufacturer business is its range of public sector equipment.
The King pole-erection unit, designed to perform the complete operation of erecting telegraph and electricity poles, is standard equipment for British Telecom.
Power-cable stringing equipment is operated by Electricity Boards as are the cable-wheel trailers built to carry loads from 1.5 to 15 tonnes.
Powered ladders are embodied in the design of rapid-intervention vehicles by leading manufacturers such as Chubb, Gloster Saro and Carmichael. Specialist transporters include various adaptations of scissor lifts for airport use while lightweight trailers are equipped with adjustable towbars.
But the reason for my visit to Market Harborough was to see what King is best known for — its specialist low-loader trailer equipment. The most recent example was being handed over to Western Excavating (ECG), part of the China Clay Group.
This 90-tonne-payload lowloader, designed TL90/15, is one of the largest and most sophisticated built by King Trailers to match a customer's requirement. It took about five months to build, and special features include a detachable rear bridge, requested by Western Excavating, so that it can be interchanged with a beam deck used to transport bulldozers.
Although not a prerequisite of ECC, the rear bridge may be adapted for use as a single bogie with drawbar or in combination with similar bogies forming a modular drawbar platform.
Axle-load equalisation is ensured with hydraulic suspension which has the facility for raising by as much as 300mm (11.8in) giving ground clearance over hump-back bridges and uneven ground or lowering to reduce the load height and increase overhead clearance. Manoeuvrability problems, not eased by an overall length of 20.78mm (68ft), have been successfully overcome by specifying steering systems at front and rear.
Power steering, with progressive response to each of the four rear-steering axles, is activiated by a kingpin wedge. The steering head is designed to allow removal of the Hydroneck splitter beam while retaining full power steering able to turn the wheels through a mean 40degree steering angle under maximum load.
Power steering of the divider neck provides for full 90-degree control. Hydraulic pressure, of about 400 psi, is generated by powerpack mounted on the Hydroneck, and can be used to operate the hydraulic neck in the case of power take-off failure.
Alternatively, it allows the rear axles to be steered by a wander-lead hand-control if the tractive unit is not equipped with a pt-o. This system is also used to retract the axles to the steering head when the hydraulic neck is removed.
King advocates the benefits of its divider neck design over that of the jeep dolly which has been used in export models designed for operation at 200 tons. However, some are used in Britain by obtaining the issue of a Special Vehicle Order.
For UK operation the twopoint articulation of the jeep dolly is more susceptible to jack-knifing and much more difficult to reverse.
The King load-divider neck retains the mobility aspect with single-point articulation so that it is less likely to jack-knife and the steering arrangement provides for full control, both forward and reverse. As the axles on the divider beam assembly turn within the axle, overall combination length can be made shorter and trailer axleweight lighter. The standard jeep dolly needs a heavier and larger gooseneck to allow the dolly to steer.
Where possible, King has sourced in Britain, but German BPW axles were the only ones to provide sufficient capacity of 16.77 tonnes.
Kingpin loading of up to 46 tons is split on a two-to-one ratio between the drive axles of the tractive ur.it and the dividerneck axle.
The rear-axle spread of 1360mm (4ft 51/2in) is still at the discussion stage with the Department of Transport for operation at between 70 and 150 tonnes.
Western Excavating's Volvo F12, equipped with a ZF torque converter on the front of its SR 70 gearbox, is geared to climb a one-in-four gradient at 100 tons gross combination weight. Under typical operating conditions, it runs at about 60 tons gross, but the company is looking towards the future where larger items of plant may need transportation.
The vehicle will be employed in about 500 movements a year. A typical load time for a straight neck trailer is about 10 minutes; the complication of the extra axle may prolong this slightly.