"Do it Yourself" Handling
Page 69
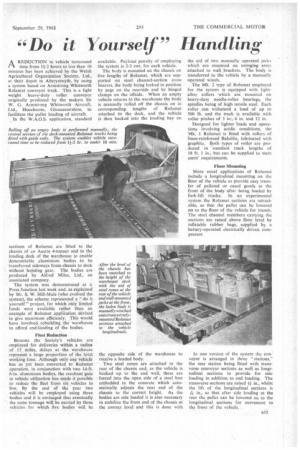
If you've noticed an error in this article please click here to report it so we can fix it.
AREDUCTION in vehicle turnround time from 1:1-2 hours to less than 10 minutes has been achieved by the Welsh Agricultural Organization Society, Ltd., at their depot in Aberystwyth, by using a system based on Armstrong Whitworth Rolamat conveyor track. This is a light weight heavy-duty roller conveyor originally produced by the makers Sir W. G. Armstrong Whitworth Aircraft, Ltd., Hucclecote, Gloucestershire, to facilitate the pallet loading of aircraft.
In the W.AD.S. application, standard sections of Rolamat are fitted to the chassis of an Austin 4-tonner and to the loading deck of the warehouse to enable demountable aluminium bodies to be transferred sideways from.chassis to deck without hoisting gear. The bodies are produced by Alfred Miles, Ltd., an associated company.
The system was demonstrated at a Press function laSt week and, as explained by Mr. S. W. Hill-Male (who evolved the system), the scheme represented a "do it. yourself " project, for which ohlY limited funds were available rather than an example of Rolamat application devised to give maximum efficiency. This would have involved_ rebuilding, the warehouse to afford end-loading of the bodies.
Fleet Reduction Because the Society's vehicles are employed for deliveries within a radius of 15 miles, delays at the warehouse represent a large proportion of the total working time. Although only one vehicle has as yet been converted to Rolamat operation, in conjunction with two 14-ft. 6-in, aluminium bodies, the resultant gain in vehicle utilization has made it possible to reduce the fleet from six vehicles to five. By the end of the year two vehicles will be employed using three bodies and it is envisaged that eventually the same tonnage will be carried by three vehicles for which five bodies will be available. Payload penalty of employing the system is 2-3 cwt. for each vehicle.
The body is mounted on the chassis on five lengths of Rolamat, which are supported on steel channel-section cross hearers, the body being locked in position by pegs on the nearside and by hinged clamps on the offside. When an empty vehicle returns to the warehouse the body is manually rolled off the chassis on to corresponding lengths of Rolamat attached to the deck, and the vehicle is then backed into the loading bay on the opposite side of the warehouse to receive a loaded body.
Two steel cones are attached to the rear of the chassis and, as the vehicle is hacked up to the end wall, these are forced into the open side of a steel box embedded in the concrete which automatically adjusts the rear end of the chassis to the correct height. As the bodies are side loaded it is also necessary to stabilize the front end of the chassis at the correct level and this is done with the aid of two manually operated jacks which are mounted on swinging arms attached to wall, brackets. The body is transferred to the vehicle by a manually operated winch.
The Mk. 2 type of Rolamat employed for the system is equipped with lightalloy rollers which are mounted on heavy-duty needle-roller bearings, the spindles being of high tensile steel. Each roller . can withstand a load of up to 500 lb. and the track is available with roller pitches of 3 in:, 6 in. and 12 in.
Designed for lighter loads and operations involving acidic conditions, the Mk. 1 Rolamat is fitted with rollers of linen-reinforced Bakelite, lubricated with graphite. Both types of roller are produced in standard track lengths of 18 ft. 1 in., but can be supplied to meet users' requirements.
Floor Mounting
More usual applications of Rolamat include a longitudinal mounting on the floor of the vehicle to provide easy transfer of palleted or cased goods to the front of the body after being loaded by fork-lift trucks. In an experimental system the Rolamat sections are retractable, so that the pallet cart be lowered on to the floor of the vehicle for transit. The steel channel members carrying the sections. are raised above floor level by inflatable rubber bags, supplied by a battery-operated electrically driven compressor.
In one version of the system the conveyor is arranged in three "stations," the rear station being fitted with transverse conveyor sections as well as longitudinal sections to provide for side loading in addition to end loading. The transverse sections are raised 1-} in., whilst the lift of the longitudinal sections is ik in., so that after side loading at the rear the pallet can be lowered on to the longitudinal sections for movement to the front of the vehicle.