SPECIALIST LP
Page 32
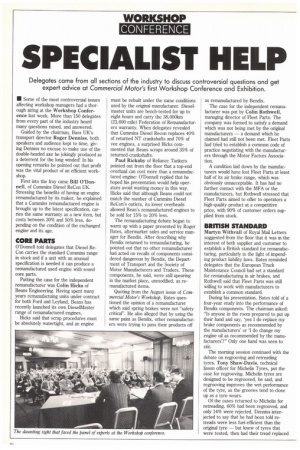
Page 33
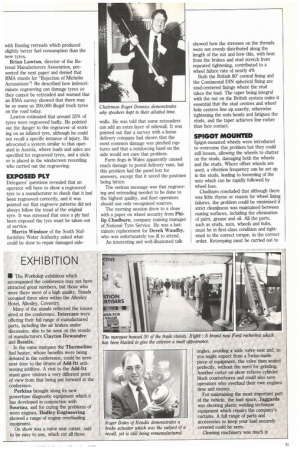
If you've noticed an error in this article please click here to report it so we can fix it.
Delegates came from all sections of the industry to discuss controversial questions and get expert advice at Commercial Motor's first Workshop Conference and Exhibition.
• Some of the most controversial issues affecting workshop managers had a thorough airing at the Workshop Conference last week. More than 150 delegates from every part of the industry heard many questions raised, and answered.
Guided by the chairman, Bass UK's transport director Roger Denniss, both speakers and audience kept to time, giving Denniss no excuse to make use of the double-headed axe he jokingly produced as a deterrent for the long winded! In his opening remarks he pointed out that profit was the vital product of an efficient workshop.
First into the fray came Bill O'Donnell, of Ctunmins Diesel ReCon UK. Stressing the benefits of having an engine remanufactured by its maker, he explained that a Cummins remanufactured engine is brought up to the latest specification, carries the same warranty as a new item, but costs between 30% and 50% less, depending on the condition of the exchanged engine and its age.
CORE PARTS
O'Donnell told delegates that Diesel ReCon carries the standard Cummins range in stock and if a unit with an unusual specification is needed it can produce a remanufactured used engine with sound core parts.
Putting the case for the independent remanufacturer was Colin Hicks of Beans Engineering. Having spent many years remanufactuing units under contract for both Ford and Leyland, Beans has recently launched its own DieselMaster range of remanufactured engines.
Hicks said that scrap procedures must be absolutely watertight, and an engine must be rebuilt under the same conditions used by the original manufacturer. Dieselmaster units are bench-tested for up to eight hours and carry the 38,000km (23,600 mile) Federation of Remanufacturers warranty. When delegates revealed that Currunins Diesel Recon replaces 40% of returned NT crankshafts and 70% of vee engines, a surprised Hicks commented that Beans scraps around 35% of returned crankshafts.
Paul Rickaby of Reliance Tankers pointed out from the floor that a top-end overhaul can cost more than a remanufactured engine: O'Donnell replied that he hoped his presentation would help operators avoid wasting money in this way. Hicks said that although Beans could not match the number of Cummins Diesel ReCon's outlets, its lower overheads allowed Bean's remanufactured engines to be sold for 15% to 20% less.
The remanufacturing debate began to warm up with a paper presented by Roger Bates, afterrnarket sales and service manager for Bendix. After describing why Bendix returned to retnanufacturing, he pointed out that no other remanufacturer had acted on recalls of components considered dangerous by Bendix, the Department of Transport and the Society of Motor Manufacturers and Traders. These components, he said, were still apearing in the market place, unmodified, as remanufactured items.
Quoting from the August issue of Commercial Motor's Workshop, Bates questioned the opinion of a remanufacturer which said spring brakes were not "safety critical". He also alleged that by using the same paint as Bendix, other remanufacturers were trying to pass their products off as remanufactured by Bendix.
The case for. the independent remanufacturer was put by Colin Rothwell, managing director of Fleet Parts. The company was formed to satisfy a demand which was not being met by the original manufacturers — a demand which he claimed had still not been met. Fleet Parts had tried to establish a common code of practice negotiating with the manufacturers through the Motor Factors Association.
A condition laid down by the manufacturers would have lost Fleet Parts at least half of its air brake range, which was obviously tmnacceptable. It has had no further contact with the MFA or the manufacturers, but Rothwell stressed that Fleet Parts aimed to offer to operators a high-quality product at a competitive price, with 90% of customer orders supplied from stock.
BRITISH STANDARD
Martyn Withvall of Royal Mail Letters suggested from the floor that it was in the interest of both supplier and customer to establish a British standard for remanufacturing, particularly in the light of impending product liability laws. Bates reminded delegates that the European Truck Maintenance Council had set a standard for remanufacttuing in air brakes, and Rothwell said that Fleet Parts was still willing to work with manufacturers to establish a common standard.
During his presentation, Bates told of a four-year study into the performance of Bendix components. The chairman asked: "Is anyone in the room prepared to put up their hand and say, 'yes I do replace my brake components as recommended by the manufacturers' or 'I do change my engine oil as recommended by the manufacturers'?" Only one hand was seen to stir.
The morning session continued with the debate on regrooving and retreading tyres. Tony Shaw-Davis, technical liason officer for Michelin Tyres, put the case for regrooving. Michelin tyres are designed to be regrooved, he said, and regrooving improves the wet performance of the tyre, as the grooves tend to close up as a tyre wears.
Of the cases returned to Michelin for retreading, 60% had been regrooved, and only 14% were rejected. Denniss interjected to say that he had been told retreads were less fuel-efficient than the original tyre — but knew of tyres that were tested, then had their tread replaced with Bandag retreads which produced slightly better fuel consumption than the new tyres.
Brian Lawton, director of the Retread Manufacturers Association, presented the next paper and denied that RMA stands for "Rejection of Michelin Accusations"! He described how indescriminate regrooving can damage tyres so they cannot be retreaded and warned that an RMA survey showed that there may be as many as 200,000 illegal truck tyres on the road today.
Lawton estimated that around 35% of tyres were regrooved badly. He pointed out the danger to the regroover of working on an inflated tyre, although he could not recall a specific instance of injury. He advocated a system similar to that operated in Austria, where loads and axles are specified for regrooved tyres, and a sticker is placed in the windscreen recording who carried out the regrooving.
EXPOSED PLY
Delegates' questions revealed that an operator will have to show a regrooved tyre to a manufacturer to check that it had been regrooved correctly, and it was pointed out that regroove patterns did not always follow the tread of the original tyre. It was stressed that once a ply had been exposed the tyre must be taken out of service.
Martin Windsor of the South Staffordshire Water Authority asked what could be done to repair damaged side walls. He was told that some retreaders can add an extra layer of sidewall. It was pointed out that a survey with a home delivery company had shown that the most common damage was pinched niptures and that a reinforcing band on the side would not cure that problem.
Farm dogs in Wales apparently caused much damage to postal delivery vans, but this problem had the panel lost for answers, except that it saved the postmen being bitten.
The serious message was that regrooving and retreading needed to be done to the highest quality, and fleet operators should use only recognised sources.
The morning session drew to a close with a paper on wheel security from Philip Chadburn, company training manager of National Tyre Service. He was a lastminute replacement for Derek Waudby, who was unfortunately too ill to attend.
An interesting and well-illustrated talk showed how the stresses on the threads were not evenly distributed along the length of the nut and how this, with heat from the brakes and stud stretch from repeated tightening, contributed to a wheel failure rate of nearly 4% Both the British 80° conical fixing and the Continental DIN spherical fixing are stud-centered fixings where the stud takes the load. The taper being integral with the nut on the British system make it essential that the stud centres and wheel hole centres line up exactly, otherwise tightening the nuts bends and fatigues the studs, and the taper achieves line rather than face contact.
SPIGOT MOUKISD
Spigot-mounted wheels were introduced to overcome this problem but they could still loosen, allowing the wheels to chatter on the studs, damaging both the wheels and the studs. Where offset wheels are used, a vibration frequency can be set up in the studs, leading to loosening of the nuts which can be rapidly followed by wheel loss.
Chadburn concluded that although there was little rhyme or reason for wheel fixing failures, the problem could be minimised if strict cleanliness was maintained between mating surfaces, including the elimination of paint, grease and oil. All the parts, such as studs, nuts, wheels and hubs, must be in first-class condition and tightened to the correct torque, in the correct order. Retorquing must be carried out to