STRESSED B( NES TAKE THE LOAD
Page 46
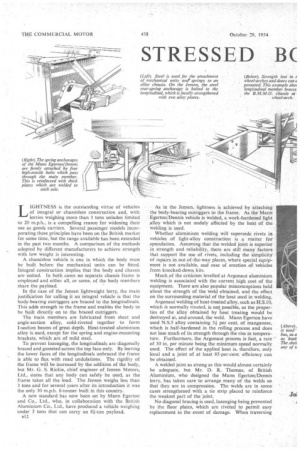
Page 47

Page 48
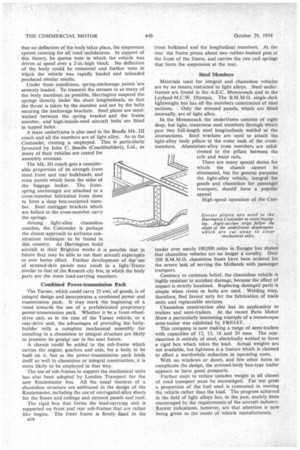
If you've noticed an error in this article please click here to report it so we can fix it.
LIGHTNESS is the outstanding virtue of vehicles of integral or chassisless construction and, with lorries weighing more than 3 tons unladen limited to 20 m.p.h., is a compelling reason for widening their use as goods carriers. Several passenger models incorporating these principles have been on the British market . for some time, but the range available has been extended in the past two months. A comparison of the methods adopted by different manufacturers to achieve strength with low weight is interesting.
A chassisless vehicle is one in which the body must be built before the mechanical units can be fitted. Integral construction implies that the body and chassis are united. In both cases no separate chassis frame is employed and either all, or some, of the body members share the payload.
In the case of the Jensen lightweight lorry, the main justification for calling it an integral vehicle is that the body-bearing outriggers are braced to the longitudinals. This adds strength to the frame and enables the body to be built directly on to the braced outriggers. The 'Main members are fabricated from sheet and angle-section alloy, cold-riveted together to form I-section beams of great depth. Heat-treated aluminium alloy is used, except for the spring and engine-mounting brackets, which are of mild steel.
To prevent lozenging, the longitudinals are diagonally braced and gusseted across the top face only. By leaving the lower faces of the longitudinals unbraced the frame is able to flex with road undulations. The rigidity of the frame will be increased by the addition of the body, but Mr. G. S. Rickie, chief engineer of Jensen Motors, Ltd., states that any body can safely be used, as the frame takes all the load. The Jensen weighs less than 3 tons and for several years after its introduction it was the only 30 m.p.h. 6-tonner built in this country.
A new standard has now been set by Mann Egerton and Co., Ltd., who, in collaboration with the British Aluminium Co., Ltd., have produced a vehicle weighing under 3 tons that can carry an 8i-ton payload. As in the Jensen, lightness is achieved by 'attaching the body-bearing outriggers to the frame. As the Mann " Egerton/Dennis vehicle is welded, a work-hardened light Alloy which is not unduly affected by the heat of the welding is used.
• Whether aluminium welding will supersede rivets in vehicles of light-alloy construction is a matter for .speculation. Assuming that the welded joint is superior in strength and reliability, there are still many factors that support the use of rivets, including the simplicity of repairs in out-of-the-way places, where special equipment is not available, and ease of erection of vehicles from knocked-down kits.
Much of the criticism levelled at Argonaut aluminium welding is associated with the current high cost of the equipment. There are also popular misconceptions held about the strength of the weld obtained, and the effect on the surrounding material of the heat used in welding.
Argonaut welding of heat-treated alloy, such as H.S.10, which is normally riveted, is not possible, as the properties of the alloy obtained by heat treating would be destroyed at, and around, the weld. Mann Egerton have used N.S.5 alloy containing 31 per cent, of manganese, which is half-hardened in the rolling process and does not lose much of its strength through the rise in temperature. Furthermore, the Argonaut process is fast, a rate of 30 in. per minute being the minimum speed normally used. The effect of the applied heat is, therefore, only local and a joint of at least 85-per-cent efficiency can be obtained.
A welded joint as strong as this would almost certainly be adequate, but Mr. D. R. Thomas, of British Aluminium, who designed the Mann Egerton/Dennis lorry, has taken care to arrange many of the welds so that they are in compression. The welds are in some cases strengthened with a tie strip placed to reinforce the weakest part of the joint.
No diagonal bracing is used, lozenging being prevented by the floor plates, which are riveted to permit easy replacement in the event of damage. When traversing uneven roads the structure flexes, thereby transmitting the stresses widely throughout the vehicle. Fatigue failure is not expected by Mr. Thomas, who has calculated that the frame should well outlive the mechanical units.
Integral or chassisless construction has not yet appeared in the field of small goods vehicles, except for the light vans that are modified private cars of the monocoque type. StrOng underframes of pressed steel are employed and the body is usually made of sheet steel, which is attached directly to the underframe, often by welding.
New possibilities have now been opened up by the introduction of the chassisless crew car built by Thomas Harrington, Ltd., for British Overseas Airways Corporation, and the Turner front-drive integral-construction eight-seat bus. Although at the Commercial Motor Show these two models were exhibited as passenger carriers; they could be used equally well for goods.
The Harrington crew car, built to carry 12 people, has an unladen weight of 2 tons 131 cwt. and in van form, for a payload,of 2 tons, it is estimated that the weight would be 2 tons 8 cwt. It is virtually a scaled-down
version of the Harrington Contender 41-seat coach, which was introduced at the Commercial Motor Show in .&2.
The method of construction employed in the Contender and the crew car incorporates a strong underframe which is built up of .six transverse members of varying depths placed to coincide with the main pillars. The transverse members are joined by short longitudinal members to form rectangular sections. Engine and spring-mounting points are fixed to the longitudinals, but stiffness in the length of the vehicle is provided by the body sides, the floor and the roof.
Scientific design is called for in a vehicle in which all the members, including the panelling, carry the load. Before embarking upon the construction of the Contender, Harrington calculated the stresses to be• expected in the various members by treating the body as a tube. Subsequent tests at the Motor Industry Research Association's proving ground indicated that the stresses in the various members corresponded closely to the original calculated figures.
The extreme rigidity of the Contender body is unusual. Mr. K. Langridge, Harrington's chief engineer, claims that no deflection of the body takes place, the suspension system catering for all road undulations. In support of this theory, he quotes tests in which the vehicle was driven at speed over a 2-in.-high block. No deflection of the body cobld be measured and further tests in which the vehicle was rapidly loaded and unloaded produced similar results.
Under these conditions, spring-anchorage points are severely loaded. To transmit the stresses to as many of the body members as possible, Harrington suspend the springs directly under the short longitudinals, so that the thrust is taken by the member and not by the bolts securing the anchorage brackets. Steel plates are sandwiched between the spring bracket and the frame member, and high-tensile-steel aircraft bolts are fitted in lapped holes. A main underframe is also used in the Beadle Mk. III coach and all the members are of light alloy. As in the Contender, riveting is employed. This is particularly favoured by John C. Beadle (Coachbuilders), Ltd., as many of their vehicles are crated for assembly overseas.
The Mk. III coach gets a considerable proportion of its strength from stout front and rear bulkheads, and truss panels which form the sides of the luggage locker. The frontspring anchorages are attached to a cross-member fabricated from sheet to form a deep box-sectioned member. Steel outrigger brackets which are bolted to the cross-member carry the springs.
Among light-alloy chassisless coaches, the Contender is perhaps the closest approach to airframe construction technique to be found in this country. As Harrington build aircraft at their Brighton works it is possible that in future they may be able to use their aircraft experience to ever better effect. Further development of the use of stressed-skin panels may result in a light frame similar to that of the Renault city bus, in which the body parts are the main load-carrying members.
Combined Power-transmission Pack The Turner, which could carry 25 cwt. of goods, is of integral design and incorporates a combined power and transmission pack. It may mark the beginning of a trend towards the use of a prefabricated proprietary power-transmission pack. Whether it be a front-wheeldrive unit, as in the case of the Turner vehicle, or a rear-drive unit, the advantages of providing the bodybuilder with a complete mechanical assembly for installing in a chassisless or integral structure are likely to promote its greater use in the near future.
A chassis -could be added to the sub-frame which carries the engine, gearbox and axle, for a body to be built on it, but as the power-transmission pack lends itself so well to chassisless or integral construction, it is more likely to be employed in that way.
The use of sub-frames to support the mechanical units has also been adopted by London Transport for the new Routemaster bus. All the usual features of a chassisless structure are embraced in the design of the Routemaster, including the use of corrugated-alloy sheets for the floors and ceilings and stressed panels and roof.
The rigid box that forms the load-carrying unit is supported on front and rear sub-frames that are rather like bogies. The front frame is firmly fixed to the front bulkhead and the longitudinal members. At the rear the frame pivots about two rubber-bushed pins at the front of the frame, and carries the two coil springs that form the suspension at the rear.
Steel Members Materials used for integral and chassisless vehicles are by no means restricted to light alloys. Steel underframes are found in the A.E.C. Monocoach and in the Leyland-M.C.W. Olympic. The B.M.M.O. single-deck lightweight bus has all the members constructed of steel sections. Only the stressed panels, which are fitted internally, are of light alloy.
In the Monocoach the underframe consists of eight deep, but light, transverse steel members through which pass two full-length steel longitudinals welded at the intersections. Steel brackets are used to attach the light-alloy body pillars to the outer ends of the crossmembers. Aluminium-alloy truss members are solid . riveted to the pillars between the crib and waist rails.
There are many special duties for which the chassis cannot be eliminated, but for general purposes the light-alloy vehicle, integral for goods and chassisless for passenger transport, should have a popular appeal.
High-speed operation of the Con tender over nearly 100,000 miles in Europe has shown that chassisless vehicles are no longer a novelty. Over 200 B.M.M.O. chassisless buses have been ordered for the severe task of serving the Midlands with passenger transport.
Contrary to common belief, the chassisless vehicle is highly resistant to accident damage, because the effect of impact is strictly localized. Replacing damaged parts is simple when rivets or bolts are used. Welding may, therefore, find favour only for the fabrication of main units and replaceable sections.
Chassisless construction also has its application to trailers and semi-trailers. At the recent Paris Motor Show a particularly interesting example of a monocoque semi-trailer was exhibited by FREJAT.
This company is now making a range of semi-trailers with capacities of 12, 15, 18 and 20 tons. The con stsuction is entirely of steel, electrically welded to form a rigid box which takes the load. Actual weights are not available, but lightness is a feature which is claimed to effect a worthwhile reduction in operating costs. With no windows or doors, and few other items to complicate the design, the stressed-body box-type trailer appears to have good prospects. Further steps to reduce unladen weight in all classek of road transport must be encouraged. Far too great a proportion of the fuel used is consumed in moving the vehicle rather than the load. The progress achieved in the field of light alloys has, in the past, mainly been encouraged by the requirements of the aircraft industry.
Recent indications, however, are that attention is now being given to the needs of vehicle manufacturers.