Positive outlook
Page 28
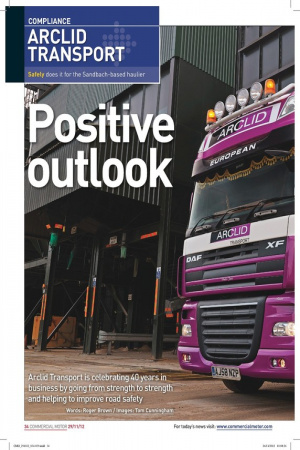
Page 30
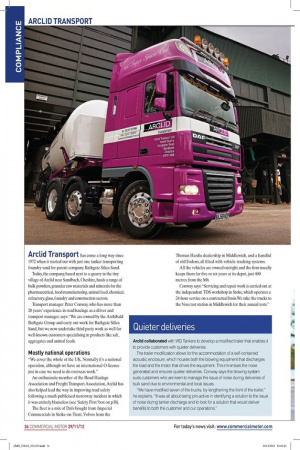
Page 31
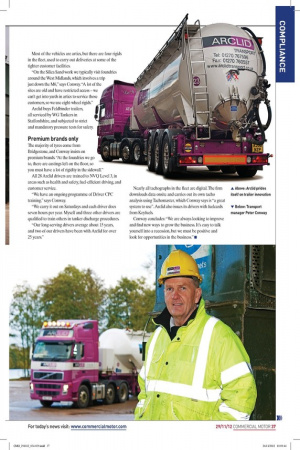
Page 32
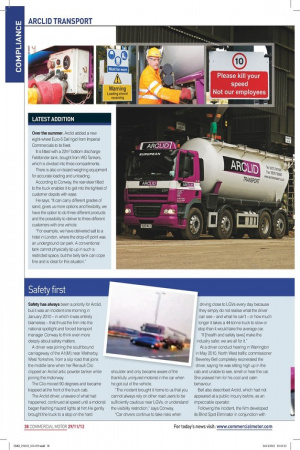
Page 33
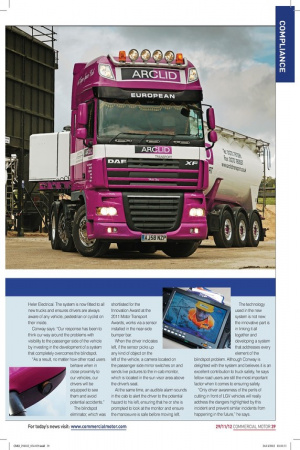
If you've noticed an error in this article please click here to report it so we can fix it.
Arclid Transport is celebrating 40 years in business by going from strength to strength and helping to improve road safety
Words: Roger Brown / Images: Tom Cunningham Arclid Transport has come a long way since 1972 when it started out with just one tanker transporting foundry sand for parent company Bathgate Silica Sand.
Today, the company, based next to a quarry in the tiny village of Arclid near Sandbach, Cheshire, hauls a range of bulk powders, granular raw materials and minerals for the pharmaceutical, food manufacturing, animal feed, chemical, refractory, glass, foundry and construction sectors.
Transport manager Peter Conway, who has more than 20 years’ experience in road haulage as a driver and transport manager, says: “We are owned by the Archibald Bathgate Group and carry out work for Bathgate Silica Sand, but we now undertake third party work as well for well-known customers specialising in products like salt, aggregates and animal feeds.
Mostly national operations
“We cover the whole of the UK. Normally it’s a national operation, although we have an international O-licence just in case we need to do overseas work.” An enthusiastic member of the Road Haulage Association and Freight Transport Association, Arclid has also helped lead the way in improving road safety following a much-publicised motorway incident in which it was entirely blameless (see ‘Safety First’ box on p38).
The fleet is a mix of Dafs bought from Imperial Commercials in Stoke-on-Trent, Volvos from the Thomas Hardie dealership in Middlewich, and a handful of old Fodens, all fitted with vehicle-tracking systems.
All the vehicles are owned outright and the firm usually keeps them for five or six years at its depot, just 400 metres from the M6.
Conway says: “Servicing and repair work is carried out at the independent TDS workshop in Stoke, which operates a 24-hour service on a contractual basis.We take the trucks to the Vosa test station in Middlewich for their annual tests.” Most of the vehicles are artics, but there are four rigids in the fleet, used to carry out deliveries at some of the tighter customer facilities.
“On the Silica Sand work we typically visit foundries around the West Midlands, which involves a trip just down the M6,” says Conway. “A lot of the sites are old and have restricted access – we can’t get into yards in artics to service those customers, so we use eight-wheel rigids.” Arclid buys Feldbinder trailers, all serviced by WG Tankers in Staffordshire, and subjected to strict and mandatory pressure tests for safety.
Premium brands only
The majority of tyres come from Bridgestone, and Conway insists on premium brands. “At the foundries we go to, there are castings left on the floor, so you must have a lot of rigidity in the sidewall.” All 28 Arclid drivers are trained to NVQ Level 3, in areas such as health and safety, fuel-efficient driving, and customer service.
“We have an ongoing programme of Driver CPC training,” says Conway.
“We carry it out on Saturdays and each driver does seven hours per year. Myself and three other drivers are qualified to train others in tanker discharge procedures.
“Our long-serving drivers average about 15 years, and two of our drivers have been with Arclid for over 25 years.” Nearly all tachographs in the fleet are digital. The firm downloads data onsite and carries out its own tacho analysis using Tachomaster, which Conway says is “a great system to use” . Arclid also issues its drivers with fuelcards from Keyfuels.
Conway concludes: “We are always looking to improve and find new ways to grow the business. It’s easy to talk yourself into a recession, but we must be positive and look for opportunities in the business.” n
Quieter deliveries
Arclid collaborated with WG Tankers to develop a modified trailer that enables it to provide customers with quieter deliveries.
The trailer modification allows for the accommodation of a self-contained acoustic enclosure, which houses both the blowing equipment that discharges the load and the motor that drives the equipment. This minimises the noise generated and ensures quieter deliveries. Conway says the blowing system suits customers who are keen to manage the issue of noise during deliveries of bulk sand due to environmental and local issues.
“We have modified seven of the trucks, by lengthening the front of the trailer,” he explains. “It was all about being pro-active in identifying a solution to the issue of noise during tanker discharge and to look for a solution that would deliver benefits to both the customer and our operations.”
LATEST ADDITION
Over the summer, Arclid added a new eight-wheel Euro-5 Daf rigid from Imperial Commercials to its fleet.
It is fitted with a 22m3 bottom discharge Feldbinder tank, bought from WG Tankers, which is divided into three compartments.
There is also on-board weighing equipment for accurate loading and unloading.
According to Conway, the rear-steer fitted to the truck enables it to get into the tightest of customer depots with ease.
He says: “It can carry different grades of sand, gives us more options and flexibility, we have the option to do three different products and the possibility to deliver to three different customers with one vehicle.
“For example, we have delivered salt to a hotel in London, where the drop-off point was an underground car park. A conventional tank cannot physically tip up in such a restricted space, but the belly tank can cope fine and is ideal for this situation.”
Safety first
Safety has always been a priority for Arclid, but it was an incident one morning in January 2010 – in which it was entirely blameless – that thrust the firm into the national spotlight and forced transport manager Conway to think even more deeply about safety matters.
A driver was joining the southbound carriageway of the A1(M) near Wetherby, West Yorkshire, from a slip road that joins the middle lane when her Renault Clio clipped an Arclid artic powder tanker while joining the motorway.
The Clio moved 90 degrees and became trapped at the front of the truck cab.
The Arclid driver, unaware of what had happened, continued at speed until a motorist began flashing hazard lights at him.He gently brought the truck to a stop on the hard shoulder and only became aware of the thankfully uninjured motorist in the car when he got out of the vehicle.
“The incident brought it home to us that you cannot always rely on other road users to be sufficiently cautious near LGVs, or understand the visibility restriction,” says Conway.
“Car drivers continue to take risks when driving close to LGVs every day because they simply do not realise what the driver can see – and what he can’t – or how much longer it takes a 44-tonne truck to slow or stop than it would take the average car.
“If [health and safety laws] make the industry safer, we are all for it.” At a driver conduct hearing in Warrington in May 2010, North West traffic commissioner Beverley Bell completely exonerated the driver, saying he was sitting high up in the cab and unable to see, smell or hear the car. She praised him for his cool and calm behaviour.
Bell also described Arclid, which had not appeared at a public inquiry before, as an impeccable operator.
Following the incident, the firm developed its Blind Spot Eliminator in conjunction with Heler Electrical. The system is now fitted to all new trucks and ensures drivers are always aware of any vehicle, pedestrian or cyclist on their inside.
Conway says: “Our response has been to think our way around the problems with visibility to the passenger side of the vehicle by investing in the development of a system that completely overcomes the blindspot.
“As a result, no matter how other road users behave when in close proximity to our vehicles, our drivers will be equipped to see them and avoid potential accidents.” The blindspot eliminator, which was shortlisted for the Innovation Award at the 2011 Motor Transport Awards, works via a sensor installed in the near-side bumper bar.
When the driver indicates left, if the sensor picks up any kind of object on the left of the vehicle, a camera located on the passenger side mirror switches on and sends live pictures to the in-cab monitor, which is located in the sun visor area above the driver’s seat.
At the same time, an audible alarm sounds in the cab to alert the driver to the potential hazard to his left, ensuring that he or she is prompted to look at the monitor and ensure the manoeuvre is safe before moving left. The technology used in the new system is not new: the innovative part is in linking it all together and developing a system that addresses every element of the blindspot problem. Although Conway is delighted with the system and believes it is an excellent contribution to truck safety, he says fellow road users are still the most important factor when it comes to ensuring safety.
“Only driver awareness of the perils of cutting in front of LGV vehicles will really address the dangers highlighted by this incident and prevent similar incidents from happening in the future,” he says.