Tricks of the trade
Page 105
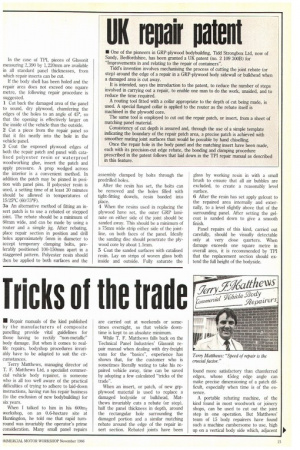
Page 106
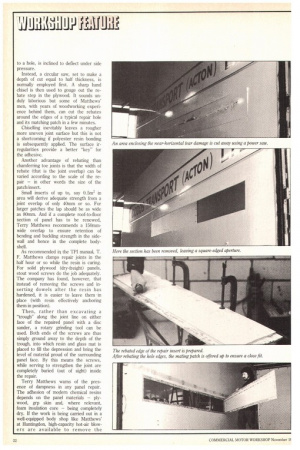
Page 107
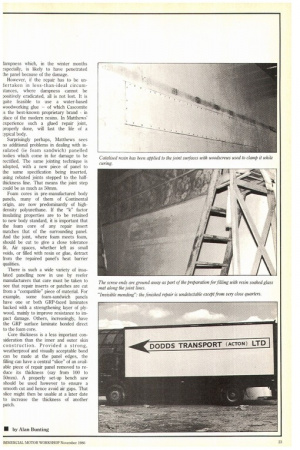
Page 108
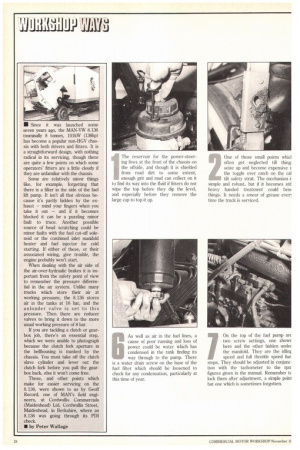
If you've noticed an error in this article please click here to report it so we can fix it.
• Repair manuals of the kind published by the manufacturers of composite panelling provide vital guidelines for those having to rectify "non-metallic" body damage. But when it comes to reallife repairs, bodyshop procedures invariably have to be adapted to suit the circumstances.
Terry Matthews, managing director od T. F. Matthews Ltd, a specialist commercial vehicle body repairer, is someone who is all too well aware of the practical difficulties of trying to adhere to laid-down instructions, having run his repair business (to the exclusion of new bodybuilding) for six years.
When I talked to him in his 600m2 workshop, on an 0.6-hectare site at Huntingdon, he told me that rapid turnround was invariably the operator's prime consideration. Many small panel repairs are carried out at weekends or sometimes overnight, so that vehicle downtime is kept to an absolute minimum.
While T. F. Matthews falls back on the Technical Panel Industries' Glasonit repair manual when dealing with dry-freight vans for the "basics", experience has shown that, for the customer who is sometimes literally wating to take his repaired vehicle away, time can be saved by adopting a few calculated "tricks of the trade".
When an insert, or patch, of new grpplywood material is used to replace a damaged bodyside or bulkhead, Matthews invariably cuts a rebate (or step), half the panel thickness in depth, around the rectangular hole surrounding the damaged portion and a similar matching rebate around the edge of the repair insert section. Rebated joints have been found more satisfactory than chamferred edges, whose 45deg edge angle can make precise dimensioning of a patch difficult, especially when time is of the essence.
A portable rebating machine, of the kind found in most woodwork or joinery shops, can be used to cut out the joint step in one operation. But Matthews' team of 15 body repairers have found such a machine cumbersome to use, high up on a vertical body side which, adjacent
to a hole, is inclined to deflect under side pressure.
Instead, a circular saw, set to make a depth of cut equal to half thickness, is normally employed first. A sharp hand chisel is then used to gouge out the rebate step in the plywood. It sounds unduly laborious but some of Matthews' men, with years of woodworking experience behind them, can cut the rebates around the edges of a typical repair hole and its matching patch in a few minutes.
Chiselling inevitably leaves a rougher more uneven joint surface but this is not a shortcoming if polyester resin bonding is subsequently applied. The surface irregularities provide a better "key" for the adhesive.
Another advantage of rebating than chamferring toe joints is that the width of rebate (that is the joint overlap) can be varied according to the scale of the repair — in other words the size of the patch/insert.
Small inserts of up to, say 0.5m2 in area will derive adequate strength from a joint overlap of only 40nana or so. For larger patches the lap should be as wide as 80mm. And if a complete roof-to-floor section of panel has to be renewed, Terry Matthews recommends a 150mmwide overlap to ensure retention of bending and buckling strength in the sidewall and hence in the complete bodyshell.
As recommended in the TPI manual, T. F. Matthews clamps repair joints in the half hour or so while the resin is curing. For solid plywood (dry-freight) panels, stout wood screws do the job adequately. The company has found, however, that instead of removing the screws and inserting dowels after the resin has hardened, it is easier to leave them in place (with resin effectively anchoring them in position).
Then, rather than excavating a "trough" along the joint line on either face of the repaired panel with a disc sander, a rotary grinding tool can be used. Both ends of the screws are thus simply ground away to the depth of the trough, into which resin and glass mat is placed to fill the depression and bring the level of material proud of the surrounding panel face. By this means the screws, while serving to strengthen the joint are completely buried (out of sight) inside the repair.
Terry Matthews warns of the presence of dampness in any panel repair. The adhesion of modern chemical resins depends on the panel materials — plywood, gip skin and, where relevant, foam insulation core — being completely dry. If the work is being carried out in a well-equipped body shop like Matthews' at Huntingdon, high-capacity hot-air blowers are available to remove the Jampness which, in the winter months ..specially, is likely to have penetrated the panel because of the damage.
However, if the repair has to be uniertaken in less-than-ideal circum stances, where dampness cannot be positively eradicated, all is not lost. It is iuite feasible to use a water-based woodworking glue — of which Cascotnite Ls the best-known proprietary brand in place of the modern resins. In Matthews' experience such a glued repair joint, properly done, will last the life of a typical body.
Surprisingly perhaps, Matthews sees DO additional problems in dealing with in sulated (ie foam sandwich) panelled bodies which come in for damage to be rectified. The same jointing technique is adopted, with a new piece of panel to the same specification being inserted, using rebated joints stepped to the halfthickness line. That means the joint step could be as much as 50mm.
Foam cores in pre-manufactured body panels, many of them of Continental origin, are now predominantly of high density polyurethane. If the "k" factor insulating properties are to be retained to new body standard, it is important that the foam core of any repair insert matches that of the surrounding panel.
And the joint, where foam meets foam, should be cut to give a close tolerance fit. Air spaces, whether left as small voids, or filled with resin or glue, detract from the repaired panel's heat barrier qualities.
There is such a wide variety of insulated panelling now in use by reefer manufacturers that care must be taken to see that repair inserts or patches are cut from a "compatible" piece of material. For example, some foam-sandwich panels have one or both GRP-faced laminates backed with a strengthening layer of ply wood, mainly to improve resistance to impact damage. Others, increasingly, have the GRP surface laminate bonded direct to the foam core.
Core thickness is a less important consideration than the inner and outer skin' construction. Provided a strong, weatherproof and visually acceptable bond can be made at the panel edges, the filling can have a central "slice" of an avail able piece of repair panel removed to reduce its thickness (say from 100 to 50mm). A properly set-up bench saw should be used however to ensure a smooth cut and hence avoid air gaps. That slice might then be usable at a later date to increase the thickness of another patch. I/ Since it was launched some seven years ago, the MAN-VW 8.136 (nominally 8 tonnes, 101kW (136hp) has become a popular non-HGV chassis with both drivers and fitters. It is a straightforward design, with nothing radical in its servicing, though there are quite a few points on which some operators' fitters are a little cloudy if they are unfamiliar with the chassis.
Some are relatively minor things like, for example, forgetting that there is a filter in the side of the fuel lift pump. It isn't all that obvious because it's partly hidden by the exhaust — mind your fingers when you take it out — and if it becomes blocked it can be a puzzling minor fault to trace. Another possible source of head scratching could be minor faults with the fuel cut-off solenoid or the combined inlet manifold heater and fuel injector for cold starting. If either of these, or their associated wiring, give trouble, the engine probably won't start.
When dealing with the air side of the air-over-hydraulic brakes it is important from the safety point of view to remember the pressure differential in the air system. Unlike many trucks which store their air at working pressure, the 8.136 stores air in the tanks at 16 bar, and the unloader valve is set to this pressure. Then there are reducer valves to bring it down to the more usual working pressure of 8 bar.
If you are tackling a clutch or gearbox job, there's an essential step, which we were unable to photograph because the clutch fork aperture in the hellhousing is masked by the chassis. You must take off the clutch slave cylinder and lever out the clutch fork before you pull the gearbox back, else it won't come free.
These, and other points which make for easier servicing on the 8.136, were shown to us by Geoff Record, one of MAN's field engineers, .at Cordwallis Commercials (Maidenhead) Ltd, Cordwallis Street, Maidenhead, in Berkshire, where an 8.136 was going through its PDI check.
• by Peter Wallage