Aluminium in Maintenance Work
Page 38
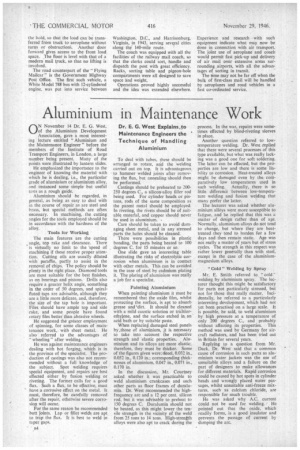
If you've noticed an error in this article please click here to report it so we can fix it.
Dr. E. G. West Explains,to Maintenance Engineers the Technique of Handling Aluminium
ON November 14 Dr. E. G. West, of the Aluminium Development Association, gave a most interesting lecture entitled "Aluminium and the Maintenance Engineer •• before the members of the Institute of Road Transport Engineers, in London, a large number being present. Many of the points were illustrated by lantern slides.
He emphasized the importance to the engineer of knowing the material with which he is dealing, i.e., the particular grade of aluminium or aluminium alloy, tind instanced some simple but useful tests as a rough guide.
Aluminium should be regarded, in general, as being as easy to deal with in the course of repair as are steel and brass, but special methods are often necessary. In machining, the cutting angles for the tools employed should be in accordance with the hardness of the alloy.
Tools for Working
The main features are the cutting angle top rake and clearance. There is virtually no limit to the -speed of machining if these receive proper attention. Cutting oils are usually diluted with paraffin, partly to assist in the removal of chips. The policy should be plenty in the right place. Diamond tools are most suitable for the best finishes, as on bearings and pistons. Drills also require a greater helix angle, something in the order of 50 degrees, and spiralfluted taps are advisable, although they are a little more delicate, and, therefore, the size of the tap hole is important. Files should have ample top and side rake, and some people have found rotary files better than abrasive wheels.
He suggested the greater employment of spinning, for some classes of maintenance work, with sheet metal. He also referred to the advantages of "wheeling" after welding.
He was against maintenance engineers dealing with hot forging, which is in the province of the specialist, The production of castings was also not recommended without a full knowledge of the subject. Spot welding requires special equipment, and repairs are best effected either by fusion welding or riveting. The former calls for a good flux. Such a flux, to be effective, must have a corrosive effect on the metal, It must, therefore, be carefully removed after the repair, otherwise severe corm
, slop will occur.
For the same reason he recommended butt joints. Lap or fillet welds are apt to trap the flux. It is best to weld in taper gaps, To deal with tubes, these should be arranged to rotate, and the 'welding carried out on top. It is advantageous to hammer welded joints after removing the flux, but annealing should then be performed.
Castings should be preheated to 200250 degrees C., a silicon-alloy filler rod being used. For cylinder heads or pistons, rods of the same composition as the parent metal should be employed. In riveting, the rivets should be of suitable material, and copper should never be used in aluminium.
Care should be taken to avoid damaging sheet metal, and in any stressed parts the holes should be cleaned.
There were possibilities in plastic bonding, the parts being heated to 100 degrees C. for 15 minutes or so.
One slide gave an interesting table illustrating the risks of electrolytic corrosion when aluminium is in contact with other metals. This can be avoided in the.case of steel by cadmium plating it. The plating of aluminium was really
a job for a specialist. .
Painting Aluminium
When painting aluminium it must be remembered that the oxide film, whilst protecting the surface, is apt to absorb grease and 'dirt. It should be cleaned with a mild caustic solution or tri6hlorethylene, and the surface etched in an acid bath or by suitable paste.
When replacing damaged steel panels by ,those of aluminium, it is necessary to take into account the respective
strength and 'elastic properties. Aluminium and its alloys are more elastic; therefore, they must be thicker. Some of the figures given were: Steel, 0.032 in., 0.052 in., 0.120 in.; corresponding thicknesses of aluminium, 0.047 in., 0.071 in., 0.170 in.
In the discussion, Mr. Courtney asked whether it was practicable to weld aluminium crankcases and such other parts as floor frames of duralumin. Dr. West recommended the highfrequency arc and a 12 per cent, silicon rod, but it was advisable to preheat to 150 degrees C. Duralumin should not be heated, as this might lower the tensile strength in the vicinity of the weld from 25 tons to 14 tons. High-strength alloys were also apt to crack during the
process. In the war, repairs were sometimes effected by blind-riveting sleeves in place.
Another question referred to lowtemperature welding. Dr. West replied that there were several processes of this type available, but what was really lacking was a good one for soft soldering. The latter can be effected, but the properties are low and there is some liability to corrosion. Heat-treated alloys might be damaged even by the comparatively low temperatures used in such welding. Actually, there is so little difference between low-temperature welding and fusion welding that many prefer the latter.
The lecturer was asked whether aluminium alloys were more susceptible to fatigue, and he replied that this was a matter of design rather than of age. Normally, aluminium alloys do not tend to change, but where they are heattreated they tend to harden for a few days and then remain static. Age was not really a matter of years but of stress cycles. The strength in this respect was rather lower generally than with steel, except in the case of the aluminiummagnesium alloys.
" Cold " Welding by Spray Mr. E. Smith referred to. "cold" welding by aluminium spray. The lecturer thought this might be satisfactory for parts not particularly stressed, but not for those that really matter. Incidentally, he referred to a particularly interesting development, which had not Yet been practised on a large scale. It is possible, he said, to weld aluminium by high pressure at a temperature of only 200 degrees C., and probably without affecting its properties. This method was used by Germany for aircraft radiators, and has been tried out in Britain for several years.
Replying to a question from Mr. Dack, Dr, West said that a common cause of corrosion in such parts as aluminium water jackets was the use of unsuitable alloys and a failure on the part of designers to make allowances for different materials. Rapid corrosion could be caused by hot spots in cylinder heads and wrongly placed water passages, whilst unsuitable anti-freeze mixtures, such as calcium chloride, are responsible for much trouble.
He was asked why A.C. current could not be used for welding. He pointed out that the oxide, which readily forms, is a good insulator and prevents the passage of current by damping the arc.