Aircraft Practice in
Page 35
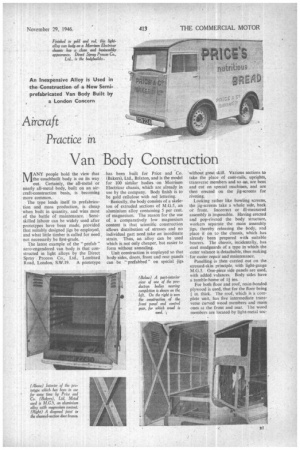
Page 36
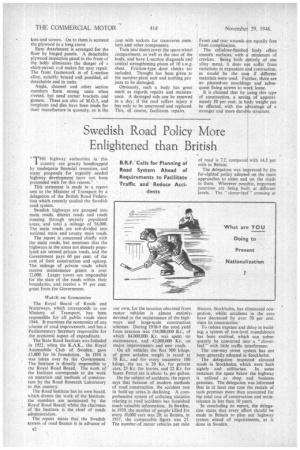
If you've noticed an error in this article please click here to report it so we can fix it.
Van Body Construction
MANY people hold the view that the coachbuilt body is on its way out. Certainly, the all-metal or nearly all-metal body, built on an aircraft-construction basis, is becoming more common.
The type lends itself to prefabrication and mass production, is cheap when built in quantity, and wins most of the battle of maintenance. Semiskilled labour can be widely used after prototypes have been made, provided that suitably designed jigs be employed, and what little timber is called for need not necessarily be first-grade.
The latest example of the " prcfab " acro-engendered van body is that constructed in light alloys by the Direct Spray Process Co., Ltd., Lombard Road, London, S.W.19. A prototype has been built for Price and Co. (Bakers), Ltd., Brixton, and is the model for 100 similar bodies on Morrison Electricar chassis, which are already in use by the company. Body finish is to be gold cellulose with red lettering.
Basically, the body consists of a skeleton of extruded sections of M.G.5, an aluminium alloy containing 5 per cent. of magnesium. The reason for the use of a comparatively low magnesium content is that scientific construction allows distribution of stresses and no individual part need take an inordinate strain. Thus, an alloy can be used which is not only cheaper, but easier to form without annealing.
Unit construction is employed so that body sides, doors, front and rear panels can be " prefabbed " on special jigs without great skill. Various sections to take the place of cant-rails, uprights, transverse members and so on, are bent and cut on special machines, and are then erected on the jig-screens for riveting.
Looking rather like bowling screens, the jig-screens take a whole side, back or front. Incorrect or ill-measured assembly is impossible. Having erected and pop-riveted the body structure, workers separate the main assembly jigs, thereby releasing the body, and place it on to the chassis, which has already been prepared with suitable bearers. The chassis, incidentally, has steel mudguards of a type in which the outer valance is detachable, thus making for easier repair and maintenance.
Panelling is then carried out on the stressed-skin principle, with light-gauge M.G.5. One-piece side panels are used, with added valances. Body sides have a tumble-home of 1 ins.
For both floor and roof, resin-bonded plywood is used, that for the floor being f; in. thick. The roof, which is a complete unit, has five intermediate transverse curved wood members and main ones at the front and rear. ihe wood members are located by light-metal soc kets and screws. On to them is screwed the plywood in a long curve.
Easy detachment is arranged for the floor by hinged panels. A detachable plywood inspection panel in the front of the bddy eliminates the danger of a short-circuit and makes for easy repair. The front framework is of L-section alloy, suitably braced and panelled, all detachable and in units.
Angle, channel and other section members form strong units when riveted, but need corner brackets and gussets. ,These are also of M.G.5, and templates and dies have been made for their manufacture in quantity, as is the case with sockets for transverse members and other components.
Twin rear doors cover the spare-wheel compartment, as well as the rear of the body, and have L-section diagonals and central strengthening plates of 10 s.w.g. sheet. Friction-type door checks arc included. Thought has been given to the number-plate unit and nothing projects to be damaged.
Obviously, such a body has great merit as regards repairs and maintenance. A damaged side can be renewed in a day; if 'the roof suffers injury It has only to be unscrewed and replaced. This, of course, facilitates repairs. Front and rear wounds are equally free from complication.
The cellulose-finished body offers smooth surfaces; with al minimum of crevices. Being built entirely of one alloy metal, it does not suffer from variations in expansion and contraction. as would be the case if different materials were used. Further, there are no planted-on mouldings and subsequent fixing screws to work loose.
It is claimed that by using this type of construction, a saving of approximately 50 per cent. in body weight can be effected, with the advantage of a stronger and more durable structure.