Taking it to the limit in search of perfection
Page 34
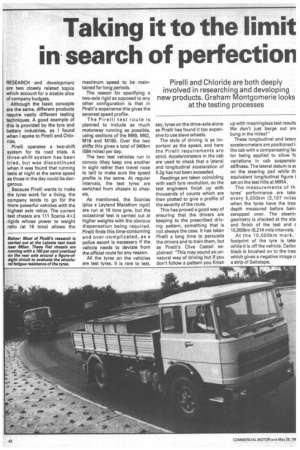
Page 35
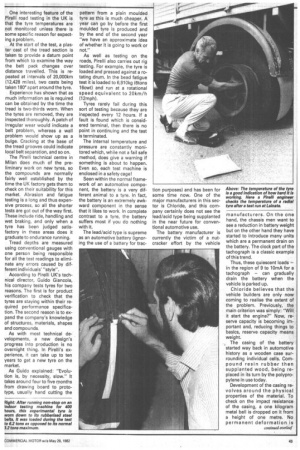
Page 36
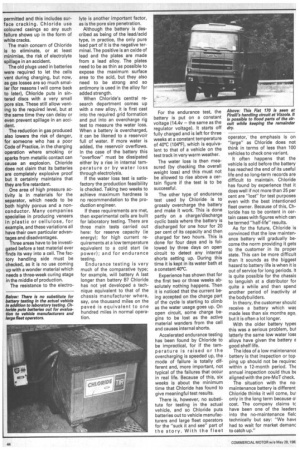
If you've noticed an error in this article please click here to report it so we can fix it.
RESEARCH and development are two closely related topics which account for a sizable slice of company budgets.
Although the basic concepts are the same, different products require vastly different testing techniques. A good example of this is provided by the tyre and battery industries, as I found when I spoke to Pirelli and Chloride.
Pirelli operates a two-shift system for its road trials. A three-shift system has been tried, but was discontinued when it was found that running tests at night at the same speed as those in the day could be dangerous.
Because Pirelli wants to make the tyres work for a living, the company tends to go for the more powerful vehicles with the highest axle ratios. The current test chassis are 111 Scania 4x2 rigids whose power to weight ratio (at 16 tons) allows the maximum speed to be maintained for long periods.
The reason for specifying a two-axle rigid as opposed to any other configuration is that in Pirelli's experience this gives the severest speed profile.
The Pirelli test route is planned to include as much motorway running as possible, using sections of the M69, M62, M18 and M180. Over the two shifts this gives a total of 940km (584 miles) per day.
The two test vehicles run in convoy (they keep one another in sight rather than travel nose to tail) to make sure the speed profile is the same. At regular intervals, the test tyres are switched from chassis to chassis.
As mentioned, the Scanias (plus a Leyland Marathon rigid) are run at 16 tons gvw, but the occasional test is carried out at higher weights with the obvious dispensation being required. Pirelli finds this time-consuming and over-complicated, as a police escort is necessary if the vehicle needs to deviate from the official route for any reason.
All the tyres on the vehicles are test tyres. It is rare to test, say, tyres on the drive-axle alone as Pirelli has found it too expensive to use slave wheels.
The style of driving is as important as the speed, and here the Pirelli requirements are strict. Accelerometers in the cab are used to check that a lateral and longitudinal acceleration of 0.2g has not been exceeded.
Readings are taken coinciding with each tyre revolution, so the test engineers finish up with thousands of counts which are then plotted to give a profile of the severity of the route.
This has proved a good way of ensuring that the drivers are keeping to the prescribed driving pattern, something that is not always the case. It has taken Pirelli a long time to persuade the drivers and to train them, but as Pirelli's Clive Castell explained: "This may sound an unnatural way of driving but if you don't follow a pattern you finish up with meaningless test results We don't just barge out an bung in the miles!"
These longitudinal and latera accelerometers are positioned ii the cab with a compensating fac tor being applied to allow fo variations in cab suspensio stiffness. The lateral datum is SE on the steering pad while th equivalent longitudinal figure i set on the test hills at MIRA.
The measurements of th tyres' performance are take every 5,000km (3,107 miles when the tyres have the trea depth measured before bein swopped over. The steerin geometry is checked at the stai and finish of the test and E 10,000km (6,214 mile intervals.
At the 10,0 00km mark, footprint of the tyre is take while it is off the vehicle. Carbo black is brushed on to the trea which gives a negative image o a strip of Sellotape. One interesting feature of the Pirelli road testing in the UK is that the tyre temperatures are not monitored unless there is some specific reason for expecting a problem.
At the start of the test, a plaster cast of the tread section is taken to provide a datum point from which to examine the way the belt pack changes over distance travelled. This is repeated at intervals of 20,000km (12,428 miles), two casts being taken 180° apart around the tyre.
Experience has shown that as much information as is required can be obtained by the time the tread is two-thirds worn. When the tyres are removed, they are inspected thoroughly. A patch of irregular wear would indicate a belt problem, whereas a wall problem would show up as a bulge. Cracking at the base of the tread grooves could indicate local belt separation, and so on.
The Pirelli technical centre in Milan does much of the preliminary work on new tyres, so the compounds are normally fairly well established by the time the UK factory gets them to check on their suitability for this market. Abrasion and fatigue testing is a long and thus expensive process, so all the shorter tests are got out of the way first. These include ride, handling and wet braking, and only when a tyre has been judged satisfactory in these areas does it graduate to endurance running.
Tread depths are measured using conventional gauges with one person being responsible for all the test readings to eliminate any errors caused by different individuals' "style".
According to Pirelli UK's technical director, Guido Giancola, his company tests tyres for two reasons. The first is for product verification to check that the tyres are staying within their required performance specification. The second reason is to expand the company's knowledge of structures, materials, shapes and compounds.
As with most technical developments, a new design's progress into production is no overnight thing. In Pirelli's experience, it can take up to ten years to get a new tyre on the market.
As Guido explained: "Evolution is, by necessity, slow." It takes around four to five months from drawing board to prototype, usually hand cutting the pattern from a plain moulded tyre as this is much cheaper. A year can go by before the first moulded tyre is produced and by the end of the second year "we have an approximate idea of whether it is going to work or not."
As well as testing on the roads, Pirelli also carries out rig testing. For example, the tyre is loaded and pressed against a rotating drum. In the bead fatigue test it is loaded to 6,910kg (6tons 16cwt) and run at a rotational speed equivalent to 20km/h (12mph).
Tyres rarely fail during this sort of testing because they are inspected every 12 hours. If a fault is found which is considered terminal, then there is no point in continuing and the test is terminated.
The internal temperature and pressure are constantly monitored which, while not a fail safe method, does give a warning if something is about to happen. Even so, each test machine is enclosed in a safety cage!
Seen within the normal framework of an automotive component, the battery is a very different animal to a tyre. In fact, the battery is an extremely awkward component in the sense that it likes to work. In complete contrast to a tyre, the battery suffers most if you do nothing with it.
The lead/acid type is supreme as an automotive battery (ignoring the use of a battery for trac tion purposes) and has been for some time now. One of the major manufacturers in this sector is Chloride, and this company certainly does not see the lead/acid type being supplanted in the near future for conventional automotive use.
The battery manufacturer is currently the victim of a nutcracker effort by the vehicle manufacturers. On the one hand, the chassis men want to see a reduction in battery weight but on the other hand they have started to introduce many units which are a permanent drain on the battery. The clock part of the tachograph is a classic example of this trend.
Thus, these quiescent loads — in the region of 9 to 10mA for a tachograph — can gradually drain the battery when the vehicle is parked up.
Chloride believes that the vehicle builders are only now coming to realise the extent of the problem. Previously, the main criterion was simply: "Will it start the engine?" Now, reserve capacity is becoming important and, reducing things to basics, reserve capacity means weight.
The casing of the battery started way back in automotive history as a wooden case surrounding individual cells. Compound resin rubbe.r then supplanted wood, being replaced in its turn by the polypropylene in use today.
Development of the casing revolves around the physical properties of the material. To check on the impact resistance of the casing, a one kilogram metal ball is dropped on it from a height of one metre. No permanent deformation is permitted and this includes surface cracking. Chloride use coloured casings so any such failure shows up in the form of white cracks.
The main concern of Chloride is to eliminate, or at least minimise, the risk of electrolyte spillage in an accident.
The old plugs used in batteries were required to let the cells vent during charging, but now, as gas losses are so much smaller (for reasons I will come back to later), Chloride puts in sintered discs with a very small pore size. These still allow venting to the required level, but at the same time they can delay or even prevent spillage in an accident.
The reduction in gas produced also lowers the risk of danger, for someone who has a poor Code of Practice, in the charging operation where smoking or sparks from metallic contact can cause an explosion. Chloride does not claim that its batteries are completely explosive proof but it certainly maintains that they are fire retardant.
One area of high pressure activity is in materials for the separator, which needs to be both highly porous and a nonconductor. Many companies specialise in producing veneers in plastic or cellulose, for example, and these variations all have their own particular advantages and disadvantages.
Three areas have to be investigated before a test material ever finds its way into a cell. The factory handling side must be checked, as it is no use coming up with a wonder material which needs a three-week curing stage in the middle of production.
The resistance to the electro lyte is another important factor, as is the pore size penetration.
Although the battery is described as being of the lead/acid type, in practice, the only pure lead part of it is the negative terminal. The positive is an oxide of lead and the plates are made from a lead alloy. The plates need to be as thin as possible to expose the maximum surface area to the acid, but they also need to be strong and so antimony is used in the alloy for added strength.
When Chloride's central research department comes up with a new alloy, it is first cast into the required grid formation and put into an overcharge rig test to measure the water loss. When a battery is overcharged, it can be likened to a reservoir full of water. If more water is added, the reservoir overflows. In the case of the battery this "overflow" must be dissipated either by a rise in internal temperature or by water loss through electrolysis.
If the water loss test is satisfactory the production feasibility is checked. Taking two weeks to achieve maximum hardness is no recommendation to the production engineer.
If these requirements are met, then experimental cells are built for laboratory testing. There are three main tests carried out here: for reserve capacity (ie energy); for high current requirements at a low temperature equivalent to a cold start (ie power); and for endurance testing.
Endurance testing is very much of the comparative type; for example, will battery A last longer than battery B? Chloride has not yet developed a technique equivalent to that of the chassis manufacturer where, say, one thousand miles on the payee is equivalent to one hundred miles in normal operation. For the endurance test, the battery is put on a constant voltage (14.4v — the same as the regulator voltage). it starts off fully charged and is left for three weeks at a constant temperature of 40°C (104°F), which is equivalent to that of a vehicle on the test track in very warm weather.
The water loss is then measured (by checking the overall weight loss) and this must not be allowed to rise above a certain figure if the test is to be successful.
The other type of endurance test used by Chloride is to grossly overcharge the battery and make it work. This is done partly on a charge/discharge cyclic basis where the battery is discharged for one hour for 20 per cent of its capacity and then charged for two hours. This is done for four days and is followed by three days on open circuit to detect any internal shorts setting up. During this time it is kept in its water bath at a constant 40°C.
Experience has shown that for the first two or three weeks absolutely nothing happens. Then it is noticed that the current being accepted on the charge part of the cycle is starting to climb as the water usage goes up. On open circuit, some charge begins to be lost as the active material wanders from the cell and causes internal shorts.
Accelerated endurance testing has been found by Chloride to be impractical, for if the temperature is raised or the overcharging is speeded up, the mode of failure is totally different and, more important, not typical of the failures that occur in real life. Because of this, six weeks is about the minimum time that Chloride has found to give meaningful test results.
There is, however, no substitute for testing in the actual vehicle, and so Chloride puts batteries out to vehicle manufacturers and large fleet operators for the "suck it and see" part of the story. With the fleet operator, the emphasis is on "large" as Chloride does not think in terms of less than 100 vehicles to check one variant.
It often happens that the vehicle is sold before the battery has reached the end of its useful life and so long-term records are difficult to maintain. Chloride has found by experience that it does well if not more than 25 per cent are "lost" for test purposes even with the best intentioned fleet owner. Because of this, Chloride has to be content in certain cases with figures which can be termed "half-life" results.
As for the future, Chloride is convinced that the low maintenance battery will gradually become the norm providing it gets to the customer in its proper state. This can be more difficult than it sounds as the biggest hazard to battery life is when it is out of service for long periods. It is quite possible for the chassis to languish at a distributor for quite a while and then spend another period of inactivity al the bodybuilders.
In theory, the customer should receive a battery which was made less than six months ago, but it is often a lot longer.
With the older battery types this was a serious problem, bui latterly the same low water loss alloys have given the battery a good shelf life.
The idea of a low maintenancE battery is that inspection or top. ping up should not be requirec within a 12-month period. ThE annual inspection could thus bE aligned with the pre-MoT check.
The situation with the nomaintenance battery is different Chloride thinks it will come, bui only in the long term because 01 cost. The company claims tc have been one of the leader; into the no-maintenance fielc technically but say: "We haw had to wait for market demanc to catch up."