BUILDING THE BO LONDON'S BUSES.
Page 50
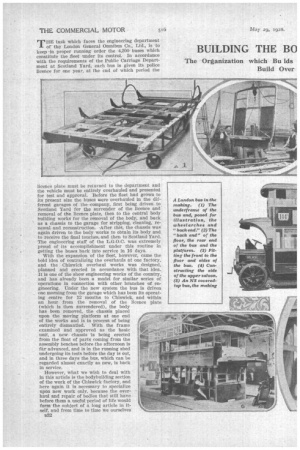
Page 51
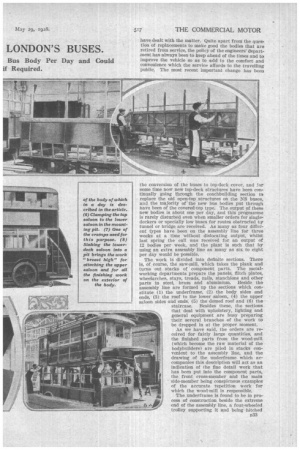
Page 52
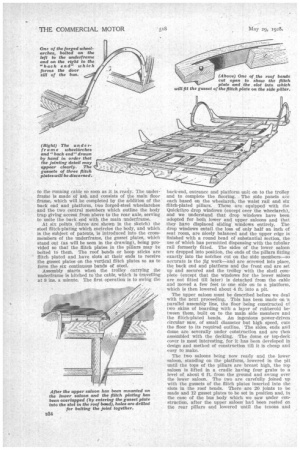
Page 53
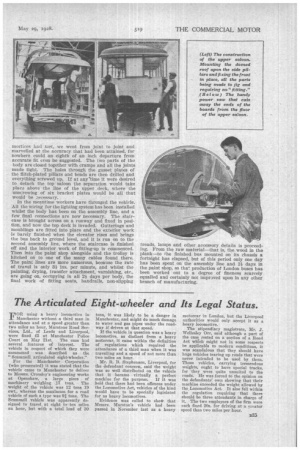
If you've noticed an error in this article please click here to report it so we can fix it.
The Organization which Bu ids Build Over Bus Body Per Day and Could if Required.
THE task which faces the engineering department of the London General Omnibus Co., Ltd., is to keep ,in proper running order the 4,200 buses which constitute the fleet under its control. In accordance with the requirements of the Public Carriage Department at Scotland Yard, each bus is given its police licence for one year, at the end of which period the
licence plate must be returned to the department and the vehicle must be entirely overhauled and presented for test and approval. Before the fleet had grown to its present size the buses were overhauled in the different garages of the company, first being driven to Scotland Yard for the surrender of the licence and removal of the licence plate, then to the central body building works for the removal of the body, and back as a chassis to the garage for stripping, cleaning, renewal and reconstruction. -After this, the chassis was again driven to the body works to obtain its body and to receive the final touches, and then to Scotland Yard. The engineering staff of the L.G.O.C. was extremely proud of its accomplishment under this routine in getting the buses back into service in 16 days, With the expansion of the fleet, however, came the bold idea of centralizing the overhauls at one factory, and the Chiswick overhaul works was designed, planned and erected in accordance with that idea. It is one of the show engineering works of the country, and has already been a model for similar series of operations in connection with other branches of engineering. Under the new system the bus is driven one morning from the garage which has been its operating centre for 12 months to Chiswick, and within an hour from the removal of the licence plate (which is then surrendered), the body has been removed, the chassis placed upon the moving platform at one end of the works and is in process of being entirely dismantled. With the frame examined and approved as the basic unit, a new chassis is being erected from the float of parts coming from the assembly benches before the afternoon is far advanced, and is in the running shed undergoing its tests before the day is out, and in three days the bus, which can be regarded almost exactly as new, is back in service.
However, what we wish to deal with in this article is the bodybuilding section of the work of the Chiswick factory, and here again it is necessary to specialize upon new work only, because the overhaul and repair of bodies that still have before them a useful period of life would form the subject of a long article in itself, and from time to time we ourselves Ba2 have dealt with the matter. Quite apart from the question of replacements to make good the bodies that are retired from service, the policy of the engineers' department has always been to keep ahead of the times and to improve the vehicle so as to add to the comfort and convenience which the service affords to the travelling public. The most recent important change has been the conversion of the buses to top-deck cover, and for some time now new top-deck structures have been continually going through the coachbuilding section to replace the old open-top structures on the NS buses, and the majority of the new bus bodies put through nave been of the covered-top type. The output of these new bodies is about one per day, and this programme is rarely disturbed even when smaller orders for singledeckers or specially low buses for routes obstructed by tunnel or bridge are received. As many as four different types have been on the assembly line for three weeks at a time without dislocating output, whilst last spring the call was received for an output of 12 bodies per week, and the plant is such that by using an extra assembly line as many as six to eight per day would be possible.
The work is divided into definite sections. There is, of course, the saw-mill, which takes the plank and turns out stacks of component. parts. The metalworking departments prepare the panels, flitch plates, wheelarches, stays, treads, rails, stanchions and other parts in steel, brass and aluminium. Beside the assembly line are formed up the sections which constitute (1) the underframe, (2) the body sides and ends, (3) the roof to the lower saloon, (4) the upper saloon sides and ends, (5) the domed roof and (6) the staircase. Besides these, the sections that deal with upholstery, lighting and general equipment are busy preparing their several branches of the work to be dropped in at the proper moment.
As we have said, the orders are received for fairly large quantities, and the finished parts from the wood-mill (which become the raw material of the bodybuilders) are piled in stacks convenient to the assembly line, and the drawing of the underframe which accompanies this description will act as an indication of the fine detail work that has been put into the component parts, the front cross-member and the main side-member being conspicuous examples of the accurate repetition work for which the wood-mill is responsible.
The underframe is found to be in process of construction beside the extreme end of the assembly line, a four-wheeled trolley supporting it and being hitched
to the running cable so soon as it is ready. The underfraine is made of 'asli and consists of the main floor frame, which will be completed by the addition of the• back end and platfOrm, two forged-steel wheelarches and the two central members which outline the body trap giving access from above to the rear axle, serving to unite the back end with the main underframe.
At six points (three are shown in the sketch) the steel flitch-plating which encircles the body, and which is the subject of patents, is introduced into the crossmembers of the underframe, the gusset plates,, which stand out (as will be seen in the drawing), being provided so that the flitch plates in the pillars may be bolted to them. The roof bends or hoop sticks are flitch plated and have slots at their ends to receive the gusset plates on the vertical flitch plates so as to form the six continuous bands of steel.
Assembly starts when the trolley carrying the underframe is hitched to the cable, which is travelling at 8 ins, a minute. The first operation is to swing the back-end, entrance and platform unit on to the trolley and to complete the flooring. The side panels are each based on the wheelarch, the waist rail and six ilitch-plated pillars. These are equipped with the Quickthro drop windows (except over the wheelarch), and we understand that drop windows have been adopted for both lower and upper saloons and that they have displaced sliding windows entirely. The drop windows entail the loss of only half an inch of seat room, are nicely balanced and the upper edge is finished with a round bead of substantial section, the use of which has permitted dispensing with the tubular rail formerly fitted. The sides of the lower saloon are dropped into position, the ends of the pillars fitting exactly into the notches cut on the side merebers—so accurate is the jig work—and are screwed into place, the back end and platform and the front end are set up and secured and the trolley with the shell complete (except that the windows for the lower saloon are not fitted till later) is detached from the cable and moved a few feet to one side on to a platform, which is then lowered about 4 ft. into a pit.
The upper saloon must be described before we deal with the next proceeding. This has been made on 'a parallel assembly line, the floor being constructed of two skins of boarding with a layer of rubberoid between them, built on to the main side members and the flitch-plated bends. An ingenious power-driven circular saw, of small diameter but high speed, cuts the floor to its required outline. The sides, ends and dome are severally under construction and are then assembled with the decking. The dome or top-deck cover is most interesting,' for it has been developed in design and method of construction till it is cheap and easy to make.
The two saloons being now ready and the lower saloon, standing on the platform, lowered in the pit until the tops of the pillars are breast high, the top saloon is lifted in a cradle having four grabs to a level of about 6 ft. from the ground and swung over the lower saloon. The two are carefully joined up with the gussets of the flitch plates inserted into the slots in the roof bends. There are 20 joints to be made and 12 gusset plates to be set in position and, in the case of the bus body which we saw under construction, after the upper saloon had been rested on the rear pillars and lowered until the tenons and mortices had met, we went from joint to joint and marvelled at the accuracy that had been attained, for nowhere could an eighth of an inch departure from accurate fit even be suggested. The two parts of the body are closed together with cramps and all the joints made tight. The holes through the gusset plates of the flitch-plated pillars and bends are then drilled and everything screwed up. If at any time it were desired to detach the top saloon the separation would take place above the line of the upper deck, where the unscrewing of six bracket plates would be all that would be necessary.
In the meantime workers have thronged the vehicle. All the wiring for the lighting system has been installed whilst the body has been on the assembly line, and a few final connections are now necessary. The staircase is brought across on a runway and fixed in position, and now the top deck is invaded. Gutterings and mouldings are fitted into place and the exterior work is barely finished when the elevator rises and brings tile bus back to ground level, and it is run on to the second assembly line, where the staircase is finished off and the interior work of fitting-up is commenced. Then into the paint shop alongside and the trolley is hitched on to one of the many cables found there. The paint lines are more numerous, because the rate of travel is only 3i ins, per minute, and whilst the painting, drying, transfer attachment, varnishing, etc., are going on, occupying in all 21 days per body, the final work of fitting seats, handrails, non-slipping treads, lamps and other accessory details is proceeding. From the raw material—that is, the wood in the plank—to the finished bus mounted on its chassis a fortnight has elapsed, but of this period only one day has been spent on the assembly line and 21 days in the paint shop, so that production of London buses has been worked out to a degree of fineness scarcely equalled and certainly not impr3ved upon in any other branch of manufacturing.