Setting the gold standard
Page 17
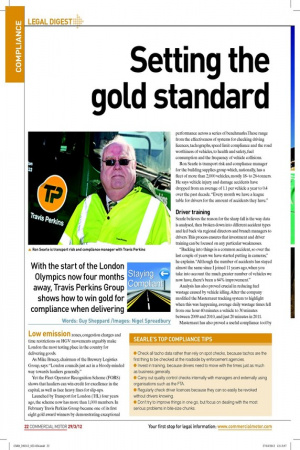
Page 19
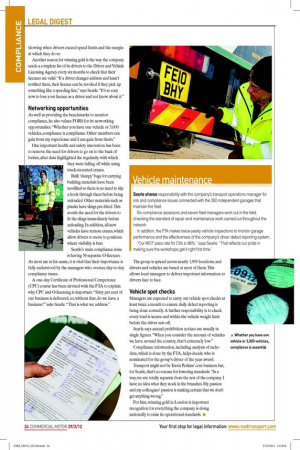
If you've noticed an error in this article please click here to report it so we can fix it.
With the start of the London Olympics now four months away, Travis Perkins Group shows how to win gold for compliance when delivering
Words: Guy Sheppard /Images: Nigel Spreadbury Low emission zones, congestion charges and time restrictions on HGV movements arguably make London the most testing place in the country for delivering goods.
As Mike Bracey, chairman of the Brewery Logistics Group, says: “London councils just act in a bloody-minded way towards hauliers generally.” Yet the Fleet Operator Recognition Scheme (FORS) shows that hauliers can win credit for excellence in the capital, as well as face heavy ines for slip-ups.
Launched by Transport for London (TfL) four years ago, the scheme now has more than 1,000 members. In February Travis Perkins Group became one of its irst eight gold award winners by demonstrating exceptional performance across a series of benchmarks.These range from the effectiveness of systems for checking driving licences, tachographs, speed limit compliance and the road worthiness of vehicles, to health and safety, fuel consumption and the frequency of vehicle collisions.
Ron Searle is transport risk and compliance manager for the building supplies group which, nationally, has a leet of more than 2,000 vehicles, mostly 18to 26-tonners. He says vehicle injury and damage accidents have dropped from an average of 1.1 per vehicle a year to 0.4 over the past decade. “Every month we have a league table for drivers for the amount of accidents they have.”
Driver training
Searle believes the reason for the sharp fall is the way data is analysed, then broken down into different accident types and fed back via regional directors and branch managers to drivers. This process ensures that investment and driver training can be focused on any particular weaknesses.
“Backing into things is a common accident, so over the last couple of years we have started putting in cameras,” he explains. “Although the number of accidents has stayed almost the same since I joined 11 years ago, when you take into account the much greater number of vehicles we now have, there’s been a 64% improvement.” Analysis has also proved crucial in reducing fuel wastage caused by vehicle idling. After the company modiied the Masternaut tracking system to highlight when this was happening, average daily wastage times fell from one hour 40 minutes a vehicle to 30 minutes between 2009 and 2010, and just 20 minutes in 2011.
Masternaut has also proved a useful compliance tool by showing when drivers exceed speed limits and the margin at which they do so.
Another reason for winning gold is the way the company sends a complete list of its drivers to the Driver and Vehicle Licensing Agency every six months to check that their licences are valid. “If a driver changes address and hasn’t notiied them, their licence can be revoked if they pick up something like a speeding ine,” says Searle. “It’s so easy now to lose your licence as a driver and not know about it.”
Networking opportunities
As well as providing the benchmarks to monitor compliance, he also values FORS for its networking opportunities. “Whether you have one vehicle or 3,000 vehicles, compliance is compliance. Other members can gain from my experience and I can gain from theirs.” One important health and safety innovation has been to remove the need for drivers to go on to the back of lorries, after data highlighted the regularity with which they were falling off while using truck-mounted cranes.
Bulk ‘dumpy’ bags for carrying building materials have been modiied so there is no need to slip a hook through them before being unloaded. Other materials such as planks have slings pre-itted. This avoids the need for the drivers to it the slings immediately before unloading. In addition, all new vehicles have remote cranes, which allow drivers to move to positions where visibility is best.
Searle’s main compliance issue is having 56 separate O-licences. As most are in his name, it is vital that their importance is fully understood by the managers who oversee day-to-day compliance issues.
A one-day Certiicate of Professional Competence (CPC) course has been devised with the FTA to explain why CPC and O-licensing is important. “Sixty per cent of our business is delivered, so, without that, do we have a business?” asks Searle. “That is what we address.” The group is spread across nearly 1,900 locations, and drivers and vehicles are based at most of them. This allows local managers to deliver important information to drivers face to face.
Vehicle spot checks
Managers are expected to carry out vehicle spot checks at least twice a month to ensure daily defect reporting is being done correctly. A further responsibility is to check every load is secure and within the vehicle weight limit before the driver sets off.
Searle says annual prohibition notices are usually in single igures. “When you consider the amount of vehicles we have around the country, that’s extremely low.” Compliance information, including analysis of tacho data, which is done by the FTA, helps decide who is nominated for the group’s driver of the year award.
Transport might not be Travis Perkins’ core business but, for Searle, that’s no excuse for lowering standards. “In a way, we are totally separate from the rest of the company. I have no idea what they stock in the branches. My passion and my colleagues’ passion is making certain that we don’t get anything wrong.”
For him, winning gold in London is important recognition for everything the company is doing nationally to raise its operational standards. n
SEARLE’S TOP COMPLIANCE TIPS
● Check all tacho data rather than rely on spot checks, because tachos are the first thing to be checked at the roadside by enforcement agencies.
● Invest in training, because drivers need to move with the times just as much as business generally.
● Carry out quality control checks internally with managers and externally using organisations such as the FTA.
● Regularly check driver licences because they can so easily be revoked without drivers knowing.
● Don’t try to improve things in one go, but focus on dealing with the most serious problems in bite-size chunks.
Vehicle maintenance
Searle shares responsibility with the company’s transport operations manager for risk and compliance issues connected with the 350 independent garages that maintain the fleet.
Six compliance assessors and seven fleet managers work out in the field, checking the standard of repair and maintenance work carried out throughout the network.
In addition, the FTA makes twice-yearly vehicle inspections to monitor garage performance and the effectiveness of the company’s driver defect reporting system.
“Our MOT pass rate for CVs is 98%,” says Searle. “That reflects our pride in making sure the workshops get it right first time.”