WELDING AND WELDING EQUIPMENT.
Page 101
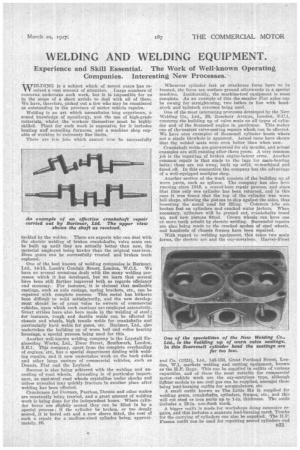
Page 102
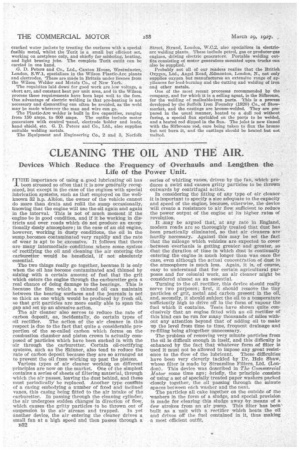
If you've noticed an error in this article please click here to report it so we can fix it.
Experience and Skill Essential. The Work of Well-known Operating Companies. Interesting New Processes.
WELDING is a subject which of recent years has received a vast amount of attention. Large numbers of concerns undertake such work, but it is impossible for us in the scope of a short article to deal with all of them. We have, therefore, picked out a few who may be considered as outstanding in the province of motor vehicle repairs.
Welding is an art which necessitates long experience, a sound knowledge of metallurgy, and the use of high-grade materials, whilst the 'workers themselves must be highly skilled. Plant for such work is expensive, for it includes heating ante annealing furnaces, and a machine shop capable of working to extremely fine limits.
There are few jobs which cannot now be successfully tackled by the welder. There are experts who can deal with the electric welding of broken crankshafts, valve seats can be built up until they are actually better than new, the material employed being harder than the original cast-iron. Even gears can be successfully treated and broken teeth replaced.
One of the best known of welding companies is Barimar, Ltd., 14-18, Lamb's Conduit Street, London, W.0.1. We have on several occasions dealt with the many welding processes which it has developed, but we learn that several have been still further improved both as regards efficiency and economy. For instance, it is claimed that malleable castings, such as axle casings, spring brackets, etc.' can be repaired with complete success. This metal has hitherto been difficult to weld satisfactorily, and the new development should be of great value to owners of commercial vehicles, upon which such castings are-employed extensively. Great strides have also been made in the welding of steel ; for instance, tough and ductile welds can be effected in chassis and wheels, high tensile welds for crankshafts and particularly hard welds for gears, etc. Barimar, Ltd., also undertakes the building up of worn ball and roller bearing housings, a special process being used for this.
Another well-known welding company is the Laystall Engineering Works, Ltd., Ewer Street, Southwark, London, S.E.1. This company, apart from the complete overhauling of engines, etc., has a special department dealing with welding repairs, and it now undertakes work on the back axles and other large casings of commercial vehicles, such as Dennis, Fiat and the Leyland.
Success is also being achieved with the welding and annealing of road wheels. Annealing is of particular importance, as cast-steel road wheels crystallize under shocks and unless annealed may quickly fracture in another place after welding has been effected.
Crankcases for Dorman, Peerless, Dennis and other makes are constantly being treated, and a great amount of welding work is being done for the independent buses. Where cylinder bores are slightly scored they can be filled in by a special process ; if the cylinder be broken, or too deeply scored, it is bored out and a new sleeve fitted, the cost of such a repair for a medium-sized cylinder being, approximately, £6. Whenever cylinder feet or crankcase faces have to be treated, the faces are surface ground afterwards in a special machine. Incidentally, the machine-tool equipment is most complete. As an example of this the smaller Fiat axles can be swung for straightening, two lathes in line with headstock and tailstock reversed being used.
One of the inost interesting processes developed by the New Welding Co., Ltd., 26, Rosebery Avenue, London, ].C.1, concerns the building up of valve seats on all types of cylinder and of the Scammell engine in particular. This makes one of the/neatest valve-seating repairs which can be effected. We have seen examples of Scammell cylinder heads where not a single blowhole is apparent. Ictual tests have shown that the welded seats were even better than when new.
Crankshaft welds are guaranteed for six months, and actual examples are still running after three years. A very common job is the repairing of broken engine-bearer arms. Another common repair is that made to the lugs for main-bearing bolts; these are cut away, built up solid, re-machined and faced off. In this connection the company has the advantage of a well-equipped machine shop.
Another section of the work consists of the building up worn parts, such as splines. The company has also been running since 1919, a scored-bore repair process, and since that time only one cylinder has been returned, and in this case it was found that the top of the cylinder was worn bell shape, allowing the pistons to slap against the sides, thus loosening the metal used for filling. Common jobs are broken feet on cylinders and cracked water jackets. When necessary, cylinders will be ground out, crankshafts trued up, and new pistons fitted. Crown wheels can have one or more teeth rebuilt by electric welding. Successful repairs are also being made to the cracked spokes of steel wheels, and hundreds of chassis frames have been repaired.
With regard to welding equipment, this takes two main forms, the electric arc and the oxy-acetylene. Harvey-Frost and Co. (19311, Ltd., 148-150, Great Portland Street-, London W.1, markets welding and cutting equipment, known as the II.F. Rego. This can be supplied in outfits of various capacities, and of these the most suitable for commercial motor -vehicle work are the oxy-acetylene type, although lighter models to use coal gas can be supplied, amongst these being lead-burning outfits for accumulators, etc. A small outfit known as The Little Six is supplied for welding gears, crankshafts, cylinders, frames, etc. and this will cut steel or iron parts up to 1-in. thickness. The outfit includes a 19-in, non-flash torch.
A bigger outfit is made for workshops doing extensive repairs, and this includes a separate lead-burning torch. Trucks for the carrying of cylinders can also be supplied. The H.F. Fuseon outfit can be used for repairing scored cylinders and
cracked water jackets by treating the surfaces with a special fusible metal, whilst the Tent is a small but efficient set, working on acetylene only, and chiefly for soldering, heating, and light brazing jobs. The complete Tent outfit can be carried in one hand.
G. D. Peters and Co., Ltd., Caxton House, Westminster, London, S.W.1, specializes in the Wilson Plastic-Arc plants and electrodes. These are made in Britain under licence from the Wilson Welder and Metals Co., of New York.
The requisites laid down for good work are low voltage, a short arc, and constant heat per unit area, and in the Wilson process these requirements have been kept well to the fore. One advantage of electric welding is that pre-heating is net necessary and dismantling can often be avoided, as the weld may be made wherever the man and wino can go.
The Plastic-Arc welder is built in five capacities, ranging from 10 amps. to 600 amps. The outfits include motor generators with control *panel, electrode bolder and leads, hand shield, etc. G. D. Peters and Co., Ltd., also supplies suitable welding metals.
The Equipment and Engineering Co., 2 and 3, Norfolk Street, Strand, London, W.C.2, also specializes in electricarc welding plants. These include petrol, gas or producer-gas engines, driving electric generators. Portable welding outfits consisting of motor generators mounted upon trucks can also be supplied.
Probably not all of our readers realize that the British Oxygen, Ltd., Angel Road, iEdmonton, London, N., not only supplies oxygen but manufactures an extensive range of appliances for lead-burning and the cutting and welding of iron and other metals.
One of the most recent processes recommended by the company, and for which it is a selling agent, is the Sifbronze, for the welding of malleable-iron parts. This is a process developed by the Suffolk Iron Foundry 4,1920) Co., of Stowmarket, and the castings are bronze-welded. They are prepared in the usual manner, heated to a dull red without fusing, a special flux sprinkled an the parts to be welded, and a heated rod dipped in the flux. The joint is now tinned with the Sifbronze rod, care being taken to flux the bronze but not burn it, and the castings should be heated but not melted.