Bulk Transport Cuts
Page 78
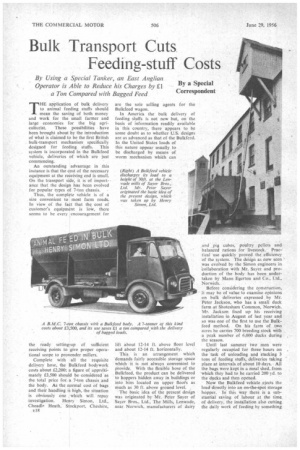
Page 79
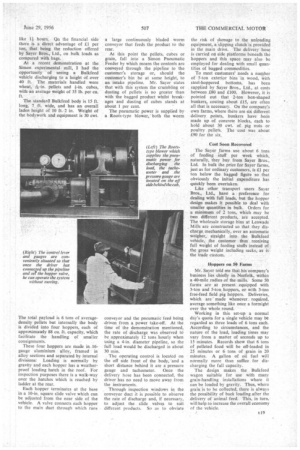
If you've noticed an error in this article please click here to report it so we can fix it.
Feeding-stuff Costs
By Using a Special Tanker, an East Anglian Operator is Able to Reduce his Charges by El a Ton Compared with Bagged Feed
• By a Special Correspondent
THE application of bulk delivery to animal feeding stuffs should mean the saving of both money and work for the small farmer and large economies for the big agriculturist. These possibilities have been brought about by the introduction of what is claimed to be the first British bulk-transport mechanism specifically designed for feeding stuffs. This system is incorporated in the Bulkfeed vehicle, deliveries of which are just commencing.
An outstanding advantage in this instance is that the cost of the necessary equipment at the receiving end is small. On the transport side, it is of importance that the design has been evolved for popular types of 7-ton chassis. •
Thus, the complete vehicle is of a size convenient to most farm roads. In view of the fact that the cost of customer's equipment is low, there seems to he every encouragement for
the ready setting-up of sufficient receiving points to give proper operational scope to provender millers.
Complete with all the requisite delivery hose, the Bulkfeed bodywork costs about £2,200; a figure of approlimately £3,500 should be considered as the total price for a 7-ton chassis and the body. As the normal cost of bags and their handling is high, the situation is obviously one which will repay
• investigation. Henry Simon, Ltd., Cheadlf. Heath, Stockport, Cheshire, EIS are the sole selling agents for the Bulkfeed wagon.
In America the bulk delivery of feeding shills is not new but, on the basis of information readily available in this country, there appears to be some doubt as to whether U.S. designs are as advanced as that of the Bulkfeed.
In the United States loads of this nature appear usually to be discharged by means of worm mechanism which can lift about 12-14 ft. above floor level and about 12-14 ft. horizontally.
This is an arrangement which demands fairly accessible storage space which it is not always convenient to provide. With the flexible hose of the Bulkfeed, the product can be delivered to hoppers hidden away in buildings or into bins located on upper flooi.s as much as 30 ft. above ground level.
The basic idea of the present design was originated by Mr. Peter Sayer of Sayer Bros., Ltd., The Mills, Lenwade, near Norwich. manufacturers of dairy
and pig cubes, poultry pellets and balanced rations for livestock. Practical use quickly proved the efficiency of the System. The design as now seen was evolved by the Simon engineers in 'collaboration with Mr. Sayer and production of the body has been undertaken by Mann Egerton and Co., Ltd., Norwich.
Before considering the construction, it may be of value to examine opinions on bulk deliveries expressed by Mr. Peter Jackson, who has a small duck farm at Shotesham Common, Norwich. Mr. Jackson fixed up his receiving installation in August of last year and so was one of the first to use the Bulkfeed method. On his farm of two acres he carries 700 breeding stock with a peak number of 6,000 ducks during the season.
Until last summer two men were regularly occupied for three hours on the 'task of unloading and stacking 3 tons of feeding stuffs, deliveries taking place at intervals of about 10 days. All the bags were kept in a meal shed, from which they had to be carried 200 yd. to the ducks and then opened.
Now the Bulkfeed vehicle ejects the load directly into an on-the-spot storage hopper. In this way there is a substantial saving of labour at the time of delivery; the installation also cutting the daily work of feeding by something like 11 hours. Qn the financial side there is a direct advantage of £1 per ton, that being the reduction offered by Sayer Bros., Ltd., on bulk loads as compared with bags.
At a recent demonstration at the Simon experimental mill, I had the opportunity of seeing a Bulkfeed vehicle discharging to a height of over 40 ft. The materials handled were wheat, A-in. pellets and cubes, with an average weight of 35 lb. per cu. ft.
The standard Bulkfeed body is 15 ft. long, 7 ft. wide, and has an overall laden height of 10 ft. 2 in. Weight of the body work and equipment is 30 cwt.
The total payload is 6 tons of averagedensity pellets but internally the body is divided into four hoppers, each of approximately 88 cu. ft. capacity, which facilitate the handling of smaller consignments.
These four hoppers are made in 16gauge aluminium alloy, framed in alloy sections and separated by internal divisions. Loading is normally by gravity and each hopper has a weatherproof loading hatch in the roof. For inspection purposes there is a walk-way over the hatches which is reached by ladder at the rear.
Each hopper terminates at the base in a 10-in, square slide valve which can be adjusted from the near side of the vehicle. A valve connects each hopper to the main duct through which runs a large continuously bladed worm conveyor that feeds the product to the rear.
At this point the pellets, cubes or grain, fall into a Simon Pneumatic Feeder by which means the contents are conveyed through the pipeline to the customer's storage or, should the customer's bin be at some height, to an intake pipeline. Mr. Sayer states that with this system the crumbling or dusting of pellets is no greater than with the bagged product whilst breakages and dusting of cubes stands at about I per cent.
The pneumatic power is supplied by a Roots-type blower, both the worm conveyor and the pneumatic feed being driven from a power take-off. At the time of the demonstration mentioned, the rate of discharge was observed to be approximately 12 tons hourly when using a 4-in, diameter pipeline, so the full load would be discharged in about 30 min.
The operating control is located on the off side front of the body, and a short distance behind it are a pressure gauge and tachometer. Once the delivery hose has been connected, the driver has no need to move away from the instruments.
Through inspection windows in the conveyor duct it is possible to observe the rate of discharge and, if necessary, to adjust the slide valves to suit different products. So as to obviate
the risk of damage to the unloading equipment, a slipping clutch is provided in the main drive. The delivery hose is carried on side platforms beneath the hoppers and this space may also be employed for dealing with small quantities of bagged commodities.
To meet customers' needs a number of 5-ton exterior bins in wood, with steel-hoppered bottoms, has been supplied by Sayer Bros., Ltd., at costs between £80 and £100. However, it is pointed out that 2-ton box-shaped bunkers, costing about £15, are often all that is necessary. On the company's own farms, where there are six different delivery points, bunkers have been made up of concrete blocks, each to hold about 30 cwt. of pig nuts or poultry pellets. The cost was about £90 for the six.
Cost Soon Recovered
The Sayer .farms use about 6 tons of feeding stuff per week which, naturally, they buy from Sayer Bros., Ltd. In bulk the price for Sayer farms, just as for ordinary customers, is £1 per ton below the bagged figure so that obviously the initial expenditure has quickly been overtaken.
Like other transport users Sayer Bros., Ltd., have a preference for dealing with full loads, but the hopper design makes it possible to deal with smaller quantities in bulk. Orders for a minimum of 2 tons, which may be two different products, are accepted. The wholesale storage bins at Lenwade Mills arc constructed so that they discharge mechanically, over an automatic weigher, straight into the Bulkfeed vehicle, the customer thus receiving full weight of feeding stuffs instead of the gross weight including sacks, as is the trade custom.
Hoppers on 50 Farms Mr. Sayer told me that his company's business lies chiefly in Norfolk, within a 40-mile radius of the mills. Some 50 farms are at present equipped with 3-ton and 5-ton. hoppers, or with 3-ton free-feed field pig hoppers. Deliveries, which are made whenever required. average something like once a fortnight over the whole round.
Working in this set-up a normal day's quota for a single vehicle may be regarded as three loads of 6 tons each. According to circumstances, and the nature of the load, loading times may vary from a matter of seconds up to 15 minutes. Records show that 6 tons of pelleted food will be off-loaded in 25 minutes or 6 tons of grain in 20 minutes. A gallon of oil fuel will normally more than suffice for discharging the full capacity.
The design makes the Bulkfced wagon suitable for use with many grain-handling installations where it can be loaded by gravity. Thus, where grain is to he collected, there is alway s the possibility of back loading after the delivery of animal feed. This, in turn, %sill help to increase the overall economy of the vehicle.