Safer, lighter, frp tankert show their manic
Page 48
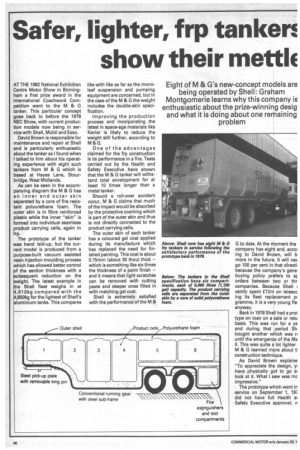
Page 49
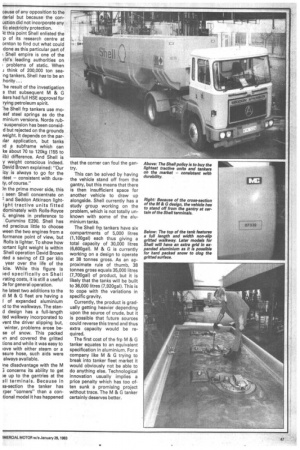
If you've noticed an error in this article please click here to report it so we can fix it.
Eight of M & G's new-concept models are being operated by Shell: Graham Montgomerie learns why this company is enthusiastic about the prize-winning desig and what it is doing about one remaining problem
AT THE 1982 National Exhibition Centre Motor Show in Birmingham a first prize award in the International Coachwork Competition went to the M & G tanker. This particular concept goes back to before the 1978 NEC Show, with current production models now being in service with Shell, Mobil and Esso.
David Brown is responsible for maintenance and repair at Shell and is particularly enthusiastic about the tanker as I found when I talked to him about his operating experience with eight such tankers from M & G which is based at Hayes Lane, Stourbridge, West Midlands.
As can be seen in the accompanying diagram the M & G has an inner and outer skin separated by a core of fire resistant polyurethane foam. The outer skin is in fibre reinforced plastic while the inner "skin" is formed into individual seamless product carrying cells, again in frp.
The prototype of the tanker was hand laid-up, but the current model is produced from a purpose-built vacuum assisted resin injection moulding process which has allowed better control of the section thickness with a subsequent reduction on the weight. The latest example in the Shell fleet weighs in at 4,81 Okg compared with the 4,800kg for the lightest of Shell's aluminium tanks. This compares like with like as far as the monoleaf suspension and pumping equipment are concerned, but in the case of the M & G the weight includes the double-skin specification.
Improving the production process and incorporating the latest in space-age materials like Kevlar is likely to reduce the weight still further, according to M & G.
One of the advantages claimed for the frp construction is its performance in a fire. Tests carried out by the Health and Safety Executive have shown that the M & G tanker will withstand total envelopment for at least 10 times longer than a metal tanker.
Should a roll-over accident occur, M & G claims that much of the impact would be absorbed by the protective coaming which is part of the outer skin and thus is not directly connected to the product carrying cells.
The outer skin of each tanker has a coloured gel coat applied during its manufacture which has replaced the need for finished painting. This coat is about 0.75mm (about 30 thou) thick — which is something like six times the thickness of a paint finish — and it means that light scratches can be removed with cutting paste and deeper ones filled in with matching gel coat.
Shell is extremely satisfied with the performance of the M & G to date. At the moment the company has eight and, accol ing to David Brown, will b more in the future. It will ne% go 100 per cent in that directii because the company's gene buying policy prefers to sr orders between two or thr companies. Because Shell cently spent £12m on telescc ing its fleet replacement pr gramme, it is a very young fie anyway.
Back in 1978 Shell had a pro1 type on loan on a sale or retu basis. This was run for a ye and during that period Shl bought another which was n until the emergence of the Ma II. This was quite a lot lighter M & G learned more about tl construction technique.
As David Brown explaine "To appreciate the design, yi have physically got to go al look at it. What I saw was mc impressive."
The prototype which went in service on September 1, 19-i did not have full Health ai Safety Executive approval; n
cause of any opposition to the aerial but because the conaction did not incorporate any tic electricity protection.
kt this point Shell enlisted the p of its research centre at brnton to find out what could done as this particular part of Shell empire is one of the rld's leading authorities on problems of static. When J think of 200,000 ton seang tankers, Shell has to be an hority
he result of the investigation s that subsequent M & G 'kers had full HSE approval for rying petroleum spirit.
he Shell frp tankers use moeaf steel springs as do the minium versions. Norde rub suspension has been considd but rejected on the grounds rveight. It depends on the parilar application, but tanks )d a subframe which can ke about 70 to 120kg (155 to ilb) difference. And Shell is y weight conscious indeed. David Brown explained: "Our icy is always to go for the itest — consistent with duraty, of course."
)n the prime mover side, this ; seen Shell concentrate on and Seddon Atkinson lightight tractive units fitted dominately with Rolls-Royce engines in preference to Cummins E290. Shell has nd precious little to choose ween the two engines from a formance point of view, but Rolls is lighter. To show how )ortant light weight is within Shell operation David Brown )ted a saving of E3 per kilo year over the life of the icle. While this figure is ;ed specifically on Shell rating costs, it is still a useful de for general operation.
he latest two additions to the II M & G fleet are having a I of expanded aluminium :d to the walkways. The stand design has a full-length ted walkway incorporated to vent the driver slipping but, winter, problems arose bese of snow. This packed vn and covered the gritted tions and while it was easy to love with either steam or a ssure hose, such aids were always available.
lne disadvantage with the M 3 concerns its ability to get
;e up to the gantries at the all terminals. Because in ss-section the tanker has
rper "corners" than a contional model it has happened
that the corner can foul the gantry.
This can be solved by having the vehicle stand off from the gantry, but this means that there is then insufficient space for another vehicle to draw up alongside. Shell currently has a study group working on the problem, which is not totally unknown with some of the aluminium tanks.
The Shell frp tankers have six compartments of 5,000 litres (1,100gal) each thus giving a total capacity of 30,000 litres (6,600gal). M & G is currently working on a design to operate at 38 tonnes gross. As an approximate rule of thumb, 38 tonnes gross equals 35,000 litres (7,700gal) of product, but it is likely that the tanks will be built to 36,000 litres (7,920ga1). This is to cope with the variations in specific gravity.
Currently, the product is gradually getting heavier depending upon the source of crude, but it is possible that future sources could reverse this trend and thus extra capacity would be required.
The first cost of the frp M & G tanker equates to an equivalent specification in aluminium. For a company like M & G trying to break into tanker fleet market it would obviously not be able to do anything else. Technological innovation usually implies a price penalty which has too often sunk a promising project without trace. The M & G tanker certainly deserves better.