Conveyor Production Keeps Leylands at 1947 Prices
Page 34
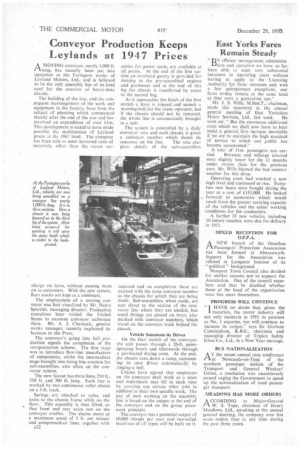
If you've noticed an error in this article please click here to report it so we can fix it.
A MOVING conveyor, nearly 1,000 ft. I-Along, has recently been put into operation at the Farington works of Leyland Motors, Ltd., and is believed to be the only assembly line of its kind . used for the erection of heavy-duty chassis.
The building of the line, and the consequent rearrangement of the work and equipment in the factory, have been the subject of planning which commenced shortly after the end of the war and has involved an expenditure of over Lim. This development is stated to have made possible the stabiltzation of Leyland prices at the 1947 level. The company has been able to meet increased costs of materials, other than the recent stir charge on tyres, without passing them on to customers. With the new system, floor stocks are kept at a minimum.
The employment of a moving conveyor was first visualized by Mr. Henry Spurrier, managing director. Production executives later visited the United States to examine conveyor technique there. Mr. A J. Chamock, general works manager, recently explained its features to the Press.
The conveyor's going into full production signals the completion of the reorganization scheme. The first stage was to introduce flow-line manufacture of components, whilst the intermediate stage brought into being line erection for sub-assemblies, also often on the conveyor system.
The new layout has three lines, 250 ft., 350 ft. and 300 ft. long. Each line is worked by two continuous roller chains on a 3-ft. track. • • Springs are attached to axles, and axles to the chassis frame while on the floor, This assembly is then lifted, so that front and rear axles rest on the conveyor cradles. The chains move at a maximum speed of 5 ft. per minute and compressed-air lines, together with A32 cables for power tools, arc available at all points. At the end of the first section an overhead gantry is provided for moving in the pre-assembled engines and gearboxes and at the end of this leg the chassis is transferred by crane to the second ling.
As it approaches the finish of the first stretch a lever is tripped and sounds a warning-bell for the crane operator, but if the chassis should not be removed. the whole line is automatically brought to a halt The system is controlled by a daily conveyor rota and each chassis is given a conveyor number which shows its sequence on the line. The rota also gives details of the sub-assemblies required and on completion these arc marked with the same conveyor number as the chassis for which they are being made, Sub-assemblies, when ready, are sent direct to the section of the conveyor line where they are needed, but small fittings are placed on trays, also marked with conveyor numbers, which travel on the conveyor track behind the chassis.
Vehicle Summons its Driver On the final stretch of the conveyor, the unit passes through a 20-ft. paintspraying booth and afterwards through a gas-heated drying oven. At the end. the chassis runs down a ramp, summoning its own driver automatically by ringing-a bell.
Unions have agreed that employees on the conveyor shall work as a team and individuals may fill in slack time by carrying out certain other jobs in addition to their own specific work. The pay of men working on the assembly line is based on the output at the end of the conveyor and on the group piecework principle. The conveyor has a potential output of 10,000 chassis per year and two-axled machines of all types will be built on it.