HARRINGTON CHASSISLESS 41-SEATER
Page 36
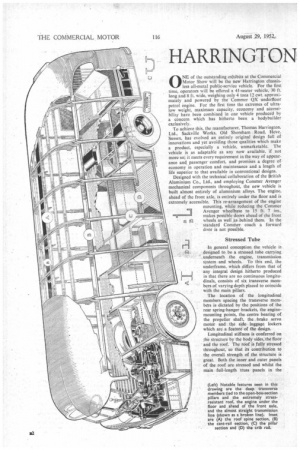
Page 37
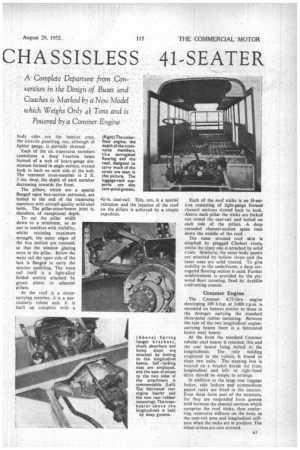
Page 38
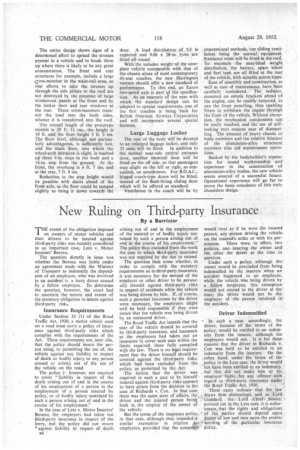
If you've noticed an error in this article please click here to report it so we can fix it.
ONE of the outstanding exhibits at the Commercial Motor Show will be the new Harrington 'chassisless all-metal public-service vehicle. For the first time, operators will be offered a 41-seater vehicle, 30 ft. long and 8 ft. wide, weighing only 4 tons 12 cwt. approximately and powered by the Commer QX underfloor petrol engine. For the first time the extremes of ultralow weight, maximum capacity, economy and accessibility have been combined in one vehicle produced by a concern which has hitherto been a bodybuilder exclusively.
To achieve this, the manufacturer, Thomas Harrington, Ltd., Sackville Works, Old Shoreham Road, Hove. Sussex, has evolved an entirely original design full of innovations and yet avoiding those qualities which make a product, especially a vehicle, unmarketable. The vehicle is as adaptable as any now available, if not more so; it meets every requirement in the way of appearance and passenger comfort, and promises a degree of economy in operation and maintenance and a length of life superior to that available in conventional designs.
Designed with the technical collaboration of the British Aluminium Co., Ltd., and employing Commer Avenger mechanical components throughout, the new vehicle is built almost entirely of aluminium alloys. The engine, ahead of the front axle, is entirely under the floor and is extremely accessible. This re-arrangement of the engine mounting, while reducing the Commer Avenger wheelbase to 15 ft. 7 ins., makes possible doors ahead of the front wheels as well as behind them. In the standard Commer coach a forward door is not possible.
In general conception the vehicle is designed to be a stressed tube carrying underneath the engine, transmission system and wheels. To this end, the underframe, which differs from that of any integral design hitherto produced in that there are no continuous longitudinals, consists of six transverse members,of varying depth placed to coincide with the main pillars.
The location of the longitudinal members spacing the transverse members is dictated by the positions of the rear spring-hanger brackets, the enginemounting points, the centre bearing of the propeller shaft, the brake servo motor and the side luggage lockers which are a feature of the design.
Longitudinal stiffness is conferred on the structure by the body sides; the floor and the roof. The roof is fully stressed throughout, so that its contribution to the overall strength of the structure is great. Both the inner and outer panels of the roof are stressed and whilst the main full-length truss panels in the
(Left) Notable features seen in this drawing are the deep transverse members tied to the open-box-section pillars and the extremely stresssesistant roof, the engine under the floor and ahead of the front axle, and the almost straight transmission line (shown as a broken line). Inset are (A) the roof spine section, (B) the cant-rail section, (C) the pillar section and (D) the crib rail.
body sides are the interior .ones, the exterior panelling, too, although of lighter gauge, is partially stressed.
Each of the six transverse members constitutes a deep I-section beam formed of a web of heavy-gauge aluminium formed in angle section, riveted back to back on each side of the web. The rearmost cross-member is 2 ft. 3 ins, deep, the depth of each member decreasing towards the front.
The pillars, which are a special flanged open box-section extrusion, are bolted to the end of the transverse members with aircraft-quality mild-steel bolts. The pillar-cross-bearer joint is, therefore, of exceptional depth.
To cut the pillar width down to a minimum, so as not to interfere with visibility, whilst retaining maximum strength, the outer edges of the box section are recessed, so that the window glazing nests in the pillar. Below the waist rail the open side of the box is flanged to carry the Interior panelling. The waist rail itself is a light-alloy folded section attached by gusset plates to adjacent pillars.
As the roof is a stresscarrying member, it is a particularly robust unit. It is built up complete with a.
Each of the roof sticks is an H-section consisting of light-gauge formed channel sections riveted back to back. Above each pillar the sticks are forked out round the cant-rail and bolted on each side of the pillars. A deep extruded channel-section spine runs down the middle of the roof.
The outer stressed roof skin is attached by plugged Chobert rivets, whilst the inner one is attached by solid rivets. Similarly, the outer body panels are attached by hollow rivets and the inner ones are solid riveted. To give stability to the underframe, a deep corrugated flooring section is used. Further reinforcement is provided by the plywood floor covering, fixed by Araldite cold-setting cement.
Commer Engine
The Commer 4.75-litre engine developing 109 b.h.p. at 3,000 r.p.m. is mounted on bearers similar to those in the Avenger carrying the standard three-point rubber mounting. Between the rear of the two longitudinal enginecarrying beams there is a fabricated heavy steel bearer.
At the front the standard Commer tubular steel bearer is retained, this and the rear bearer being bolted to the longitudinals. The only welding employed in the vehicle Is found in these two units. The steering box is located on a bracket beside the front longitudinal and leftor right-hand drive should be simple to arrange, In addition to the large rear luggage locker, side lockers and commodious parcel racks are fitted in the interior. Even these form part of the structure. for they are suspended from gussets held between the channel sections which comprise the roof sticks, thus conferring transverse stiffness on the body in the cant-rail area and longitudinal stiffness when the racks are in position. The wheel-arches are also stressed. The entire design shows signs of a determined effort to spread the stresses present in a vehicle and to break them up where there is likely to be any great concentration. The front and rear structures for example, include a large The overall length of the prototype models is 29 ft. 11 ins., the height is 10 ft. and the floor height 3 ft. 5 ins. The floor level, although not particularly advantageous, is sufficiently low, and the main floor, into which the wheel-arch intrusion is slight, is reached up three 9-in, steps in the body and a 14-in. step from the ground. At the front, the overhang is 6 ft. 7 ins. and 'at the rear, 7 ft. 9 ins. Reduction in the step height would be possible with doors ahead of the front axle, as the floor could be ramped slightly to bring it down towards the door. A load distribution of 3.5 is expected and 9.00 x 20-in. tyres are fitted all round. With the unladen weight of the complete vehicle comparable with that of the chassis alone of most contemporary 41-seat coaches, the new Harrington venture should offer a new standard of performance. To this end, an Eaton two-speed axle is part qf the specification. As an example or the ease with which the standard design can be adapted to special requirements, one of the first coaches is being built for British Overseas Airways Corporation and will incolvorate several special features. Large Luggage Locker The rear of the body will be devoted to an enlarged luggage locker, and only 35 seats will he fitted. In addition to the normal near-side central entrance door, another identical door will be fitted on the off side, so that passengers may alight on the left or right, as convenient, on aerodromes. For.B.O.A.C., hinged coach-type doors will be fitted, instead of the flush-fitting sliding door which will be offered as standard. Ventilation in the coach will be by conventional methods, top sliding ventilators being the normal equipment. Extractor vents will be fitted in the roof. To maintain the near-ideal weight distribution, the battery, spare wheel and fuel tank are all fitted at the rear of the vehicle, with suitable acceas traps: Ease of assembly and construction, as well as ease of maintenance, have been carefully considered.: The radiator, mounted on simple brackets ahead of' the engine, can be readily removed, as can the front panelling, thus enabling fitters to withdraw the engine through the front of the vehicle. Without exception, the mechanical components can be easily reached, and the use of selflocking nuts ensures ease of dismantling. The absence of heavy chassis or body members and the relative thinness of the aluminium-alloy structural members also aid maintenance operations. Backed by the bodybuilder's reputation for sound workmanship and experience in the construction of aluminium-alloy bodies, the new vehicle seems assured of a successful future. Operational experience will go far to prove the basic soundness of this truly chassisless design.