255. —Repairing Cracked Valve-cap Bridge on Tylor Engine.
Page 26
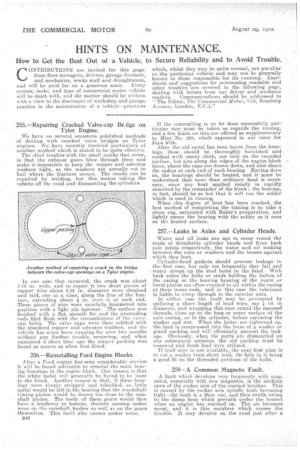
Page 27
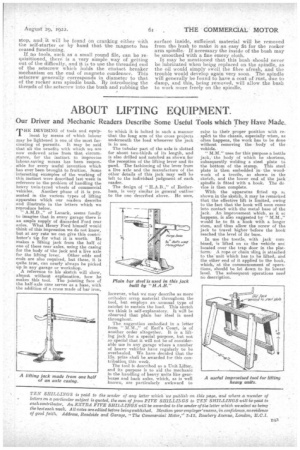
If you've noticed an error in this article please click here to report it so we can fix it.
We have on several occasions published methods, of dealing with cracked valve bridges on Tylcsr engines. We have recently received particulars oi another method which is stated to be quite effective.
The chief trouble' with the small cracks that occur, is that the exhaust gases blow through them and make it impossible to keep the copper and asbestos 'washers tight, as the washers are actually cut in half where the fracture occurs. The cracks. can be repaired by welding, but this means taking the vehicle off the road and dismantling the cylinders.
In one case that occurred, the crack was about 1-18 in. wide, and to repair it two short pieces of copper wire about 3-32 in. diameter were obtained and laid, one at a time, adong the line of the frac
ture, extending about in. over it at each end. These pieces of wire were carefully hammered into position with a light pin hammer. The surface was finished with a flat, smooth file and the protruding ends filed flush with the circumference of the valve cap holes. The valve caps were then refitted with the standard copper and asbestos washers, and the, vehicle has since been running for over two months without any further trouble occurring, and when examined short time ago the, conper packing was found as secure as when first fitted.
256.—Remetalling Ford Engine Blocks.
After a Ford engine has seen considerable service it will be found advisable to remetal the main bearing housings in the engine block. One reason is that the white metal will generally be found to be loose in the block. Another reason is that, if these hearings were simply stripped and rebedded, so little metal would be left in the bearing that the crankshaft timing pinion would he drawn too close to the camshaft pinion. The teeth of these gears would then have a tendency to bottom, thereby causing undue wear on the camshaft bushes as well as on the gears themselves. This fault also causes undue noise. .
1342 If the remetalling is to be done successfully particular care must be taken as regards the tinning, and a few hints on this are offered as supplementary to Hint No. 228, which appeared in our issue for June 27th.
After the old metal has been burnt from the bearings, these should be thoroughly burnished and rubbed with emery cloth, not only on the rounded surface, but also along the edges of the engine block faces, where the caps are drawn down, and also about the radius at each end of each bearing. Having done, so, the bearings should be heated, and it must be understood that more than ordinary heat is necessary, since any heat applied locallY is rapidly absorbed by the remainder of the block ; the bearing, in fact, should be so hot that it will run the solder which is used in tinning. When this degree of heat -has been reached, the best method of completing the tinning is to take a clean rag, saturated with Baker's preparation, and lightly smear the bearing with the solder as it runs on the heated surface.
257.—Leaks in Axles and Cylinder Heads.
Water and oil leaks are apt to occur round the studs of detachable cylinder heads and from back axle joints respectively, the water and oil leaking between the nuta or washers and the bosses against whi eh they butt. Cylinder-head .gaskets should prevent leakage in the first case, but only too frequently they fail and water creeps up the stud holes in the head. With back axles the bolts or studs holding the halves of the casing or the bearing housing of the worm or bevel pinion are often exposed to oil within the casing at their inner ends, and in this case the lubricant is liable to creep through to the exterior nuts. In either case the fault may be prevented by utilizing a 'short length of lead wire, say irr. in diameter, and wrapping this once round the exposed threads, close up to the boss or outer surface of the axle casing, or to the cylinder, before replacing the washer and nut. When the latter are tightened up, the lead is compressed into the form of a washer or gland packing and will effectually prevent the leakage. Obviously, when the parts are dismantled on any subsequent occasion, the old packing must be removed and fresh lead wire utilized.
IF load wire is not 'available, the next best plan is to cut a washer from sheet lead, the hole in it being a good fit on the threaded portions Of the bolts.
258—A Common Magneto Fault.
A fault which develops very frequently with magnetos, esnecially with new magnetos, is the sticking open of the rocker arm of the contact breaker. This is caused by the rocker arm spindle bush becoming tight—the bush is a fibre one, and fibre swells owing to the damp heat which prevails under the bonnet when an engine has warmed up. The air becomes moist, and it is this moisture which causes the trouble. It may develnn on the road just after a August 29, 1922. • stop, and -it will be found on cranking either with the self-starter or by hand that the magneto has ceased functioning.
If no tools, such as a small round file, can be requisitioned, there is a very simple way of getting out of the difficulty, and it is to use the threaded end of the setscrew which holds the Contact 'breaker mechanism on the end of magneto condenser. This setscrew generally corresponds in diameter to that of the rocker arm spindle bush. By introducing the threads of the setscrew into the bush and rubbing the surface inside, sufficient material will be removed from the bush to make it an easy fit for the rocker arm spindle. If necessary the inside of the bush may be smoothed with a fine emery cloth. It may be mentioned that this bush should never be lubricated when bekig replaced on the spindle, as the oil would simply swell the fibre afresh, and the trouble would develop again very soon. The spindle will generally be found to have a coat of rust, due to damp, and this, being removed, will allow the bush to work more freely on the spindle.