A Compression Starter for Oil and Petrol Engines
Page 37
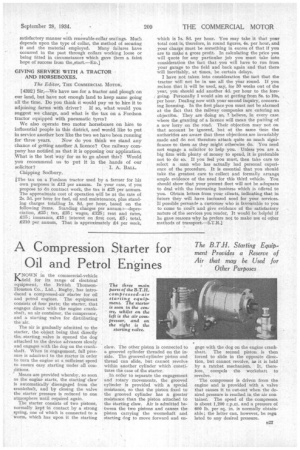
If you've noticed an error in this article please click here to report it so we can fix it.
KNOWN in the commercial-vehicle field for its range of electrical equipment, the British ThomsonHouston Co., Ltd., Rugby, has introduced a compressed-air starter for oil and petrol engines. The equipment consists of four parts; the starter, that engages direct with the engine crankshaft, an air container, the compressor, and a starting valve for distributing the air.
The air is gradually admitted to the starter, the object being that directly the starting valve is opened the dog attached to the device advances slowly and engages with the dog on the crankshaft. When in engagement, full pressure is admitted to the starter in order to turn the engine at a sufficient speed to ensure easy starting under all conditions.
Means are provided whereby, so soon as the engine starts, the starting claw. is automatically disengaged from the crankshaft, and by closing the valve the starter pressure is reduced to one atmosphere until required again.
The starter consists of two pistons, normally kept in contact by a strong spring, one of which is connected to a worm, which has upon it the starting claw. The other piston is connected to a grooved cylinder threaded on the inside. The grooved-cylinder piston and thread can slide, but cannot revolve within another cylinder which constitutes the case of the starter.
In order to separate the engagement and rotary movements, the grooved cylinder is provided with a special resistance, so that the piston fixed to the grooved cylinder has a greater resistance than the piston attached to the starting claw. Air is admitted between the two pistons and causes the piston carrying the wormshaft and starting dog to move forward and en gage with the dog on the engine crank. shalt. The second piston is then forced to slide in the opposite direction, but cannot revolve, as it is held by a ratchet mechanism. It, therefore, compels the workshatt to revolve.
The compressor is driven from the engine and is provided with a valve that causes it to cut-out when the desired pressure is reached in the air container. The speed of the compressor is about 1,200 r.p.m. and a pressure of 600 lb. per sq. in. is normally obtainable; the latter can, however, be regu latecl to any desired pressure.