There's more to choosing a compressor than you might think. Chris Graham investigates. Positive approach
Page 44
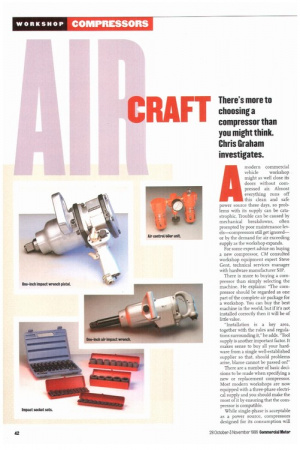
Page 45
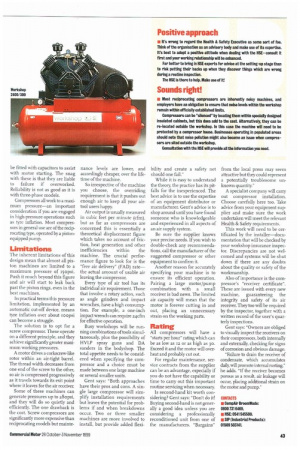
If you've noticed an error in this article please click here to report it so we can fix it.
• It's wrong to regard the !teeth & Safety Executive as some sort of foe. Think of the organisation as an advisory body and make use of its expertise. It's best to adopt a positive attitude when dealing with the HSE—consult It first and your working relationship will be enhanced.
Far better to bring in HS E experts for advice at the setting-up stage than to risk putting their backs up when they discover things which are wrong during a routine inspection.
The USE is there to help. Make use of it!
Sounds right!
• Most reciprocating compressors are inherently noisy machines, and employers have an obligation to ensure that noise levels within the workshop remain within officially established limits.
Compressors can be "silenced" by locating them within specially designed insulated cabinets, but this does add to the cost. Alternatively, they can be re-located outside the workshop. In this case the machine will need to be protected by a compressor house. Businesses operating in populated areas should note that noise pollution might also become an issue when compressors are sited outside the workshop.
Consultation with the USE will provide all the information you need.
Amodern commercial
vehicle workshop might as well close its doors without compressed air. Almost everything runs off this clean and safe power source these days, so problems with its supply can be catastrophic. Trouble can be caused by mechanical breakdowns, often prompted by poor maintenance levels—compressors still get ignored— or by the demand for air exceeding supply as the workshop expands.
For some expert advice on buying a new compressor, CM consulted workshop equipment expert Steve Gent, technical services manager with hardware manufacturer SIP.
There is more to buying a compressor than simply selecting the machine. He explains: "The compressor should be regarded as one part of the complete air package for a workshop. You can buy the best machine in the world, but if it's not installed correctly then it will be of little value.
"Installation is a key area, together with the rules and regulations surrounding it," he adds. "Tool supply is another important factor. It makes sense to buy all your hardware from a single well-established supplier so that, should problems arise, blame cannot be passed on!"
There are a number of basic decisions to be made when specifying a new or replacement compressor. Most modern workshops are now equipped with a three-phase electrical supply and you should make the most of it by ensuring that the compressor is compatible.
While single-phase is acceptable as a power source, compressors designed for its consumption will
be fitted with capacitors to assist with motor starting. The snag with these is that they are liable to failure if overworked. Reliability is not as good as it is with three-phase models.
Compressors all work to a maximum pressure—an important consideration if you are engaged in high-pressure operations such as tyre inflation. Most compressors in general use are of the reciprocating type, operated by a pistonequipped pump.
Limitations
The inherent limitations of this design mean that almost all piston machines are limited to a maximum pressure of r5opsi. Push it much beyond this figure and air will start to leak back past the piston rings, even in the best machines.
In practical terms this pressure limitation, implemented by an automatic cut-off device, means tyre inflation over about toopsi can become a struggle.
The solution is to opt for a screw compressor These operate on a different principle, and they achieve significantly greater maximum working pressures.
A motor drives a corkscrew-like rotor within an air-tight barrel. The thread width decreases from one end of the screw to the other, so air is compressed progressively as it travels towards its exit point where it leaves for the air receiver
Some of these machines can generate pressures up to 28opsi, and they will do so quietly and efficiently. The one drawback is the cost. Screw compressors are significantly more expensive than reciprocating models but mainte
nance levels are lower, and accordingly cheaper, over the lifetime of the machine.
So irrespective of the machine you choose, the overriding requirement is that it pushes out enough air to keep all your airtool users happy.
Air output is usually measured in cubic feet per minute (cfm), but as far as compressors are concerned this is essentially a theoretical displacement figure which takes no account of friction, heat generation and other inefficiencies within the machine. The crucial performance figure to look for is the "free air delivery" (FAD) rate— the actual amount of usable air leaving the compressor.
Every type of air tool has its individual air requirement. Those that involve a rotary action, such as angle grinders and impact wrenches, have a high consumption. For example, a one-inch impact wrench can require 24cfm for effective operation.
Busy workshops will be running combinations of tools simultaneously, plus the possibility of HVLP spray guns and DA sanders in the bodyshop. The total appetite needs to be considered when specifying the compressor and a choice must be made between one large machine or several smaller units.
Gent says: "Both approaches have their pros and cons. A single large compressor will simplify installation requirements but leaves the potential for problems if and when breakdowns occur. Two or three smaller machines are more involved to install, but provide added flexi
bility and create a safety net should one fail."
While it is easy to understand the theory, the practice has its pitfalls for the inexperienced. The best advice is to use the expertise of an equipment distributor or manufacturer. Gent's advice is to shop around until you have found someone who is knowledgeable and experienced in all aspects of an air supply system.
Be sure the supplier knows your precise needs. If you wish to double-check any recommendations, call the manufacturer of the suggested compressor or other equipment to confirm it.
Another reason for accurately specifying your machine is to ensure its efficient operation. Pairing a large motor/pump combination with a small receiver is bad news. The limited air capacity will mean that the motor is forever cutting in and out, placing an unnecessary strain on the working parts.
Rating
All compressors will have a "starts per hour" rating which can be as low as 12 or as high as 30. Exceed it and the motor will overheat and probably cut out.
For regular maintenance, service contracts from the supplier can be an advantage, especially if you do not have the capability or time to carry out this important routine servicing when necessary.
Is second-hand kit worth considering? Gent says: "Don't do it! Buying second-hand is not generally a good idea unless you are considering a professionally reconditioned unit from one of the manufacturers. "Bargains" from the local press may seem attractive but they could represent a potentially troublesome unknown quantity."
A specialist company will carry out compressor installation. Choose carefully here too. Take advice from your equipment supplier and make sure the work undertaken will meet the relevant Health & Safety requirements.
This work will need to be certificated by the installer—documentation that will be checked by your workshop insurance inspector. Discrepancies are not welcomed and systems will be shut down if there are any doubts about the quality or safety of the workmanship.
Also of importance is the compressor's "receiver certificate". These are issued with every new machine, guaranteeing the integrity and safety of its air receiver They too will be required by the inspector, together with a written record of the user's quarterly inspections.
Gent says: "Owners are obliged to visually inspect the receivers on their compressors, both internally and externally, checking for signs of corrosion and obvious damage.
"Failure to drain the receiver of condensate, which accumulates wffi promote internal rusting," he adds. "If the receiver becomes porous as a result, air leakage will occur, placing additional strain on the motor and pump."
CONTACTS
• CompAir BroomWade: 0800 731 6469.
• USE: 0541 545500.
• SIP (industrial Products): 01509 503141.