AN A C
Page 48
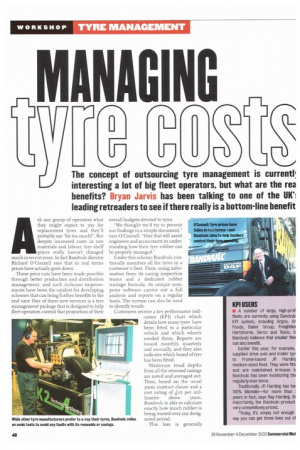
Page 49
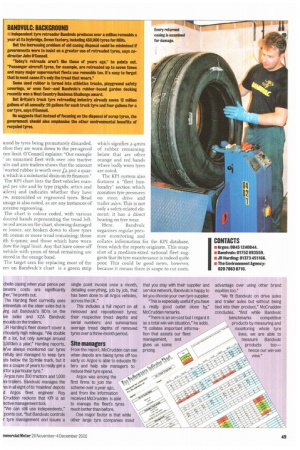
If you've noticed an error in this article please click here to report it so we can fix it.
NC
The concept of outsourcing tyre management is currentl! interesting a lot of big fleet operators, but what are the rea benefits? Bryan Jarvis has been talking to one of the UK' leading retreaders to see if there really is a bottom-line benefit Ask any group of operators what they might expect to pay for replacement tyres and they'll probably say "far too much!". But despite increased costs in raw materials and labour, tyre shelf prices really haven't changed much in recent years. In fact Bandvulc director Richard O'Connell says that in real terms prices have actually gone down.
These price cuts have been made possible through better production and distribution management, and such in-house improvements have been the catalyst for developing schemes that can bring further benefits to the end user. One of these new services is a tyre management package that is designed to help fleet operators control that proportion of their overall budgets devoted to tyres.
"We thought we'd try to present our findings in a simple document," says O'Connell. "One that will assist engineers and accountants in understanding how their tyre rubber can be properly managed."
Under this scheme Bandvulc continually monitors all the tyres in a customer's fleet. Then, using information from its casing inspection teams and a dedicated rubber wastage formula, its unique computer software carries out a full analysis and reports on a regular basis. The system can also be used to identify trends.
Customers receive a key performance indicators (KPI) chart which details how many tyres have been fitted to a particular vehicle and which wheels needed them. Reports are issued monthly, quarterly and annually, and they also indicates which brand of tyre has been fitted.
Maximum tread depths from all the returned casings are noted and averaged out. Then, based on the usual 3mm contract clause and a cost rating of Ito per millimetre above 3mm, Bandvulc is able to calculate exactly how much rubber is being wasted over any designated period.
This loss is generally
tused by tyres being prematurely discarded, !fore they are worn down to the pre-agreed nm limit. O'Connell explains: "Our example ' an unnamed fleet with over too tractive nits and 200 trailers shows that the amount wasted rubber is worth over £2,300 a guarr, which is a substantial drain on its finances." The KPI chart lists the fleet vehicles maned per site and by type (rigids, artics and ailers) and indicates whether they have 'ew, remoulded or regrooved tyres. Bead image is also noted, as are any instances of ccessive regrooving.
The chart is colour coded, with various >loured bands representing the tread left. he red areas on the chart, showing damaged re losses, are broken down to show tyres ith tomm or more tread remaining; those ith 6-9mm; and those which have worn !low the legal limit. Any that have come off vehicle with 5mm of tread remaining are ttered in the orange band.
The target area for replacing most of the res on Bandvulc's chart is a green strip which signifies 2-4min of rubber remaining; below that are other orange and red bands where badly worn tyres are noted.
The KPI system also features a "fleet husbandry" section which monitors tyre pressures on steer, drive and trailer axles. This is not only a safety-related element; it has a direct bearing on tyre wear.
Here. Bandvulc organises regular pressure monitoring and collates information for the KPI database from which the reports originate. This snapshot of a medium-sized national fleet suggests that its tyre maintenance is indeed quite poor. This could be good news, however, because it means there is scope to cut costs.