FOTOMPAYffO r gl I 8 i 0 MDTS
Page 76
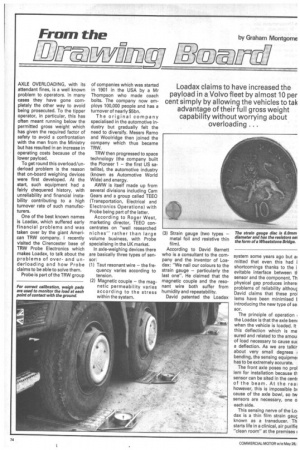
Page 77
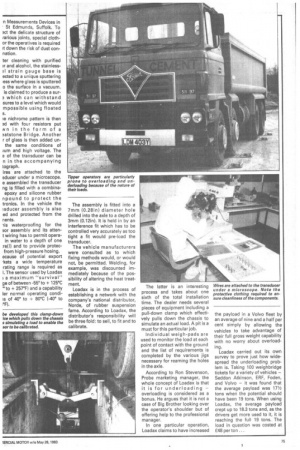
If you've noticed an error in this article please click here to report it so we can fix it.
AXLE OVERLOADING, with its attendant fines, is a well known problem to operators. In many cases they have gone completely the other way to avoid being prosecuted. To the tipper operator, in particular, this has often meant running below the permitted gross weight which has given the required factor of safety to avoid a confrontation with the men from the Ministry but has resulted in an increase in operating costs because of the lower payload.
To get round this overload/underload problem is the reason that on-board weighing devices were first developed. At the start, such equipment had a fairly chequered history, with unreliability and financial instability contributing to a high turnover rate of such manufacturers.
One of the best known names is Loadax, which suffered early financial problems and was taken over by the giant American TRW company. I recently visited the Cirencester base of TRW Probe Electronics which makes Loadax, to talk about the problems of overand underloading and how Probe claims to be able to solve them.
Probe is part of the TRW group of companies which was started in 1901 in the USA by a Mr Thompson who made coach bolts. The company now employs 100,000 people and has a turnover of nearly $5bn.
The original company specialised in the automotive industry but gradually felt the need to diversify. Messrs Ramo and Woolridge then joined the company which thus became TRW.
TRW then progressed to space technology (the company built the Pioneer 1 — the first US satellite), the automotive industry (known as Automotive World Wide) and energy.
AWW is itself made up from several divisions including Cam Gears and a group called TEEO (Transportation, Electrical and Electronics Operations) with Probe being part of the latter.
According to Roger West, marketing director, TEE° concentrates on "well researched niches" rather than large volume business, with Probe specialising in the UK market.
In axle-weighing devices there are basically three types of sensor: (1) Taut resonant wire — the frequency varies according to tension.
(2) Magnetic couple — the magnetic permeability varies according to the stress within the system. (3) Strain gauge (two types — metal foil and resistive thin film).
According to David Barnett who is a consultant to the company and the inventor of Loadax: "We nail our colours to the strain gauge — particularly the last one". He claimed that the magnetic couple and the resonant wire both suffer from humidity and repeatability.
David patented the Loadax system some years ago but a( mitted that even this had i shortcomings thanks to the i evitable interface between tt sensor and the component. Th physical gap produces inhere problems of reliability althouc David claims that these prol lems have been minimised t introducing the new type of se so r, The principle of operation the Loadax is that the axle ben( when the vehicle is loaded. It this deflection which is me sured and related to the amou of load necessary to cause suc a deflection. As we are talkir about very small degrees I bending, the sensing equipmei has to be extremely accurate.
The front axle poses no prol lem for installation because th sensor can be sited in the centr of the beam. At the real however, this is impossible IN cause of the axle bowl, so tw sensors are necessary, one o each side.
This sensing nerve of the Lo. dax is a thin film strain gauc known as a transducer. Th starts life in a clinical, air purifie "clean room" at the premises ( n Measurements Devices in
St Edmunds, Suffolk. To 3ct the delicate structure of various joints, special clothor the operatives is required it down the risk of dust connation.
ter cleaning with purified :r and alcohol, the stainless:I strain gauge base is ected to a unique sputtering ass where glass is sputtered o the surface in a vacuum. is claimed to produce a sura which can withstand sures to a level which would mpossible using floated S.
ie nichrome pattern is then ?.d with four resistors put /tin in the form of a 3atstone Bridge. Another r of glass is then added unthe same conditions of J urn and high voltage. The
e of the transducer can be n in the accompanying tograph.
ires are attached to the sducer under a microscope.
e assembled the transducer ng is filled with a combineepoxy and silicone rubber npound to protect the tronics. In the vehicle the tsducer assembly is also ed and protected from the nents.
us waterproofing for the sor assembly and its attent wiring has to permit operain water to a depth of one .re(I) and to provide protecfrom high-pressure hosing. ecause of potential export .kets a wide temperature rating range is required as I. The sensor used by Loadax ; a maximum "survival"
ge of between -55° to + 125°C '° to + 257°F) and a capability ler normal operating condiis of 40° to + 80°C (-40° to The assembly is fitted into a 7mm (0.28in) diameter hole drilled into the axle to a depth of 3rnm (0.12in). It is held in by an interference fit which has to be controlled very accurately as too tight a fit would pre-load the transducer.
The vehicle manufacturers were consulted as to which fixing methods would, or would not, be permitted. Welding, for example, was discounted immediately because of the possibility of altering the heat treatment.
Loadax is in the process of establishing a network with the company's national distributor, Norde, of rubber suspension fame. According to Loadax, the distributor's responsibility will be three fold: to sell, to fit and to calibrate. The latter is an interesting process and takes about one sixth of the total installation time. The dealer needs several pieces of equipment including a pull-down clamp which effectively pulls down the chassis to simulate an actual load. A pit is a must for this particular job.
Individual weigh-pads are used to monitor the load at each point of contact with the ground and the list of requirements is completed by the various jigs necessary for reaming the holes in the axle.
According to Ron Stevenson, Probe marketing manager, the whole concept of Loadax is that it is for underloading — overloading is considered as a bonus. He argues that it is not a case of Big Brother looking over the operator's shoulder but of offering help to the professional manager.
In one particular operation, Loadax claims to have increased the payload in a Volvo fleet by an average of nine and a half per cent simply by allowing the vehicles to take advantage of their full gross weight capability with no worry about overloading.
Loadax carried out its own survey to prove just how widespread the underloading problem is. Taking 100 weighbridge tickets for a variety of vehicles — Seddon Atkinson, ERF, Foden, and Volvo — it was found that the average payload was 171/2 tons when the potential should have been 19 tons. When using Loadax, the average payload crept up to 18.3 tons and, as the drivers get more used to it, it is reaching the full 19 tons. The load in question was costed at £48 per ton ...