Petrol Measurenkent and Engine Lubrication.
Page 17
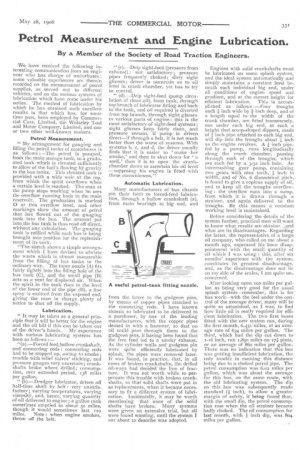
Page 18
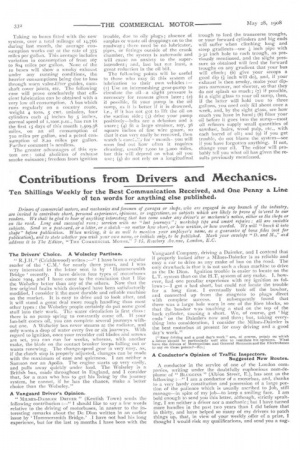
If you've noticed an error in this article please click here to report it so we can fix it.
By a Member of the Society of Road Traction Engineers.
We have received the following interesting communication from an engineer who has charge of motorbuses : some valuable experiences are therein recorded on the measurement of petrol supplies, as served out to different vehicles, and on the various systems of lubrication which have come under his notice. The method of lubrication by which he has obtained such excellent results is that which has, for some time past, been employed by Commercial Cars, Limited, the Wolseley Tool and Motor Company, Limited, and one or two other well-known makers.
Petrol Measurement.
"My arrangement for gauging and filling the petrol tanks of motorbuses is as follows :—The petrol is pumped, from the main storage tank, to a graduated tank which is elevated sufficiently to allow of the fuel's flowing by gravity to the bus tanks. This elevated tank is provided with a wide weir at the top, from which the spirit overflows when a certain level is reached. The man at the pump stops working when he sees the overflow running back to the main reservoir. The graduation is marked CP at this overflow level, and other markings show the amount of petrol that has flowed out of the gauging tank into the bus. The amount put into the bus tank is thus read off direct, without any calculation. The gauging tank is refilled while each bus is being brought into position for the replenishment of its tank.
"The sketch shows a simple arrangement which I have devised to obviate the waste which is almost inseparable from the filling of bus tanks in the ordinary way. The taper nozzle (A) fits fairly tightly into the filling hole of the bus tank (C), and the small pipe (B) acts as a vent for displaced air. When the spirit in the tank rises to the level of the lower end of the pipe (B), a fine spray is emitted from the exposed end, giving the man in charge plenty of notice to shut off the supply.
Lubrication.
" It may be taken as a general principle that it will be better for the engine and the oil bill if this can be taken out of the driver's hands. My experience with various lubricating systems has been as follows :
(a).—Forced feed,hoIlow crankshaft, and connecting rods : connecting rods had to be stopped up, owing to smoke; trouble with relief valves' sticking, and pressure gauges very uncertain ; crankshafts broke where drilled; consumption, over extended period, 138 miles per gallon.
"(b).—Dredger lubricator, driven off half-time shaft by belt : very unsatisfactory; varying temperatures, varying viscosity, and, hence, varying quantity of oil delivered to engine • a gallon tank sometimes emptied in about so miles, though it would sometimes last 520 miles. Note ; when engine smokes, throw off the belt.
" (c).—Drip sight-feed (pressure from exhaust) : not satisfactory; pressure pipes frequently choked; dirty sight glasses; driver is uncertain as to oil level in crank chamber, yet has to try to control.
" (d).—Drip sight-feed (pump circulation of clean oil), from tank, through top branch of lubricator fitting and back to the tank, and oil required is diverted from top branch, through sight glasses to various parts of engine : this is the most satisfactory of sight-feed systems ; sight glasses keep fairly clean, and pressure certain, if pump is driven direct—if through a belt, it is not much better than the worst of systems. With systems b, c, and d, the driver usually finds that it is easier to ' make her smoke,' and then to shut down for a spell,' than it is to open the crankchamber doors to ascertain his oil level —supposing his engine is fitted with these conveniences."
Automatic Lubrication,
Many manufacturers of bus chassis pin their faith to forced-feed lubrication, through a hollow crankshaft (a), from main bearings to big end, and from the latter to the gudgeon pins, by means of copper pipes attached to the connecting rods. I have known chassis so lubricated to be delivered to a purchaser, by one of the leading manufacturers, with the copper pipes dented in with a hammer, so that no oil could pass through them to the gudgeon pins, it having been found that the free feed led to a smoky exhaust. As the cylinder walls and gudgeon pin were quite efficiently lubricated by splash, the pipes were removed later. It was found, in practice, that, in all cases of broken crankshafts, the drilled oil-ways had decided the line of fracture. It was not worth while to perpetuate this trouble with broken crankshafts, so that solid shafts were put in as replacements, when it became necessary to fit a different system of lubrication. Incidentally, it may be worth mentioning that none of the solid shafts have broken. Many systems were given an extensive trial, but all were found wanting, until the system I am about to describe was adopted.
Engines with solid crankshafts must be lubricated on some splash system, and the ideal system automatically and simply maintains a constant level beneath each individual big end, under all conditions of engine speed and gradient, and at the correct height for efficient lubrication. This is accomplished as follows :—Four troughs each .1. inch wide by inch deep, and of a length equal to the width of the crank chamber, are fitted transversely, one under each big end, at such a height that scoop-shaped dippers, made of inch pipe attached to each big end, will dip into the troughs about 4 inch as the engine revolves. A inch pipe, fed by a pump, runs longitudinally along the crank chamber, passing through each of the troughs, which are each fed by a 3-32 inch hole. An intermeshing gear pump, containing two gears with nine teeth, a inch in width, and of No. 6 diametrical pitch, is found to give a copious supply of oil,. and to keep all the troughs overflowing: the overflow runs into a sump, from which it is drawn through a strainer, and again delivered to the troughs. By this means a constant working level is maintained.
Before considering the details of the. system further, practical men will. want to know what results are obtaine and what are its disadvantages. Regarding the latter, the representative of a large oil company, who called on me about a month ago, expressed his keen disappointment with the small quantity of oil which I was using : this, after six months' experience with the system, constitutes its greatest disadvantage, and, as the disadvantage does not lie on my side of the scales, I am quite unconcerned.
After looking upon too miles per gallon as being very good for the usual splash system—remember, this is for bus work—with the feel under the control of the average driver, many will be quite as astonished, as I was, to find how little oil is really required for efficient lubrication. The two first buses fitted with the new system ran, during the first month, 6,451 miles, at an average rate of 634 miles per gallon. The third, which had the dip cut down to 1-16 inch, ran 1,890 miles on I7a pints, or an average of 86o miles per gallon_ There was no indication that this bus was getting insufficient lubrication, the only trouble in running this distance being due to a choked petrol pipe. The petrol consumption was 6.02 miles per gallon, which was about the average for this bus, on the same route, with the old lubricating system. The dip on this bus was subsequently made standard (I inch), to allow a greater margin of safety, it being found that, with the small dip, the petrol consumption rose when the oil strainer became badly choked. The oil consumption for last month, with -1 inch dip, was 804 miles per gallon. Taking to buses fitted with the new system, over a total mileage of 14,766 during last month, the average consumption works out at the rate of 375 rniles per gallon. This average includes variation in consumption of from 167 to 804 miles per gallon. None of the to buses will show a smoky exhaust under any running conditions, the heavier consumptions being due to loss through worn valve-lifter guides, camshaft cover joints, etc. The following case will prove oonclusively that efficient lubrication can be obtained with a very low oil consumption. A bus which runs regularly on a country route, weight 4 tons, 5 cwt. unladen, four cylinders each 41 inches by 5 inches, normal speed of t,toor.p.m., has run in the first 15 days of this month 1,509.38 miles, on an oil consumption of 710 miles per gallon, and a petrol consumption of 8.20 miles per gallon. Further comment is needless.
The greater advantages of this system are : total abolition of exhaust smoke nuisance; freedom from ignition trouble, clue to oily plugs ; absence of surplus or waste oil droppings on to the roadway ; there need be no lubricator, pipes, or fittings outside of the crank chamber, the system is automatic and will cause no anxiety to the superintendent; and, last but not least, a great reduction in the oil bill.
The following points will be useful to those who may fit this system of lubrication to their own vehicles :(r) Use an intermeshing gear-pump to circulate the oil—a slight pressure is necessary for reasons given later; (2) if possible, fit your pump in the oil sump, as it is better if it is drowned, i.e., if it has not got to lift the oil on the suction side; (3) drive your pump positively—belts are a delusion and a snare; (4) fit a large strainer, say, 36 square inches of fine wire gauze, so that it can very easily be removed, then watch it carer,.::-; for month– you will soon find out how often it requires cleaning, usually 2.,000 to 3,000 miles, but this will depend on what oil you use; (5) do not rely on a longitudinal
trough to feed the transverse troughs, or your forward cylinders and big ends will suffer when climbing long and steep gradients—use 1 inch pipe with 3-32 inch hole to each trough, as previously mentioned, and the slight pressure so obtained will feed the forward troughs on any gradient that your bus will climb; (6) give your scoops a good dip inch will do), and, if your exhaust is then smoky, make your dippers narrower, not shorter, so that they do not splash so much ; (7) if possible, fit a sight glass to your oil sump, then, if the latter will hold two to three gallons, you need only fill about once a week, and, by the sight glass, see how much you have in hand; (8) filter your oil before it goes into the sump—most oil refiners supply small quantities of sawdust, hairs, wood pulp, etc., with each barrel of oil ; and (9) if you get trouble, do not blame the system—see if you have forgotten anything. If not, change your oil. The editor will probably tell you what oil has given the results previously mentioned.