New washers: new routines
Page 106
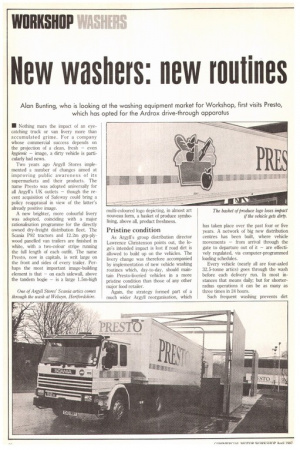
Page 107
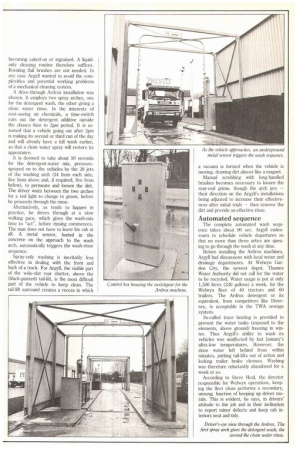
If you've noticed an error in this article please click here to report it so we can fix it.
Alan Bunting, who is looking at the washing equipment market for Workshop, first visits Presto, which has opted for the Ardrox drive-through apparatus
• Nothing mars the impact of an eyecatching truck or van livery more than accumulated grime. For a company whose commercial success depends on the projection of a clean, fresh — even hygienic — image, a dirty vehicle is particularly bad news.
Two years ago Argyll Stores implemented a number of changes aimed at improving public awareness of its supermarkets and their products. The name Presto was adopted universally for all Argyll's UK outlets — though the recent acquisition of Safeway could bring a policy reappraisal in view of the latter's already positive image.
A new brighter, more colourful livery was adopted, coinciding with a major rationalisation programme for the directly owned dry-freight distribution fleet. The Scania P92 tractors and 122m grp-plywood panelled van trailers are finished in white, with a two-colour stripe running the full length of each outfit. The name Presto, now in capitals, is writ large on the front and sides of every trailer. Perhaps the most important image-building element is that — on each sidewall, above the tandem bogie — is a large 1.5m-high
Pristine condition
As Argyll's group distribution director Lawrence Christenson points out, the logo's intended impact is lost if road dirt is allowed to build up on the vehicles. The livery change was therefore accompanied by implementation of new vehicle washing routines which, day-to-day, should maintain Presto-liveried vehicles in a more pristine condition than those of any other major food retailer.
Again, the strategy funned part of a much wider Argyll reorganisation, which has taken place over the past four or five years. A network of big new distribution centres has been built, where vehicle movements — from arrival through the gate to departure out of it — are effectively regulated, via computer-programmed loading schedules.
Every vehicle (nearly all are four-wded 32.5-tonne artics) goes through the wash before each delivery run. In most instances that means daily; but for shorterradius operations it can be as many as three times in 24 hours.
Such frequent washing prevents dirt becoming caked-on or ingrained. A liquidonly cleaning routine therefore suffices. Rotating flail brushes are not needed. In any case Arun wanted to avoid the complexities and potential working problems of a mechanical cleaning system.
A drive-through Ardrox installation was chosen. It employs two spray arches, one for the detergent wash, the other giving a clean water rinse. In the interests of cost-saving on chemicals, a time-switch cuts out the detergent additive outside the chosen 6am to 2prn period. It is assumed that a vehicle going out after 2pm is making its second or third run of the day and will already have a full wash earlier, so that a clean water spray will restore its appearance.
It is deemed to take about 50 seconds for the detergent-water mix, pressuresprayed on to the vehicles by the 38 jets of the washing arch (14 from each side, five from above and, if required, five from below), to permeate and loosen the dirt. The driver waits between the two arches for a red light to change to green, before he proceeds through the rinse.
Alternatively, as tends to happen in practice, he drives through at a slow walking pace, which gives the wash-mix time to "act", before rinsing commences. The man does not have to leave his cab at all. A metal sensor, buried in the concrete on the approach to the wash arch, automatically triggers the wash-rinse sequence.
Spray-only washing is inevitably less effective in dealing with the front and back of a truck. For Argyll, the visible part of the wide-slat rear shutter, above the (black-painted) tail-lift, is the most difficult part of the vehicle to keep clean. The tail-lift surround creates a recess in which a vacuum is formed when the vehicle is moving, drawing dirt almost like a magnet.
Manual scrubbing with long-handled brushes becomes necessary to loosen the rear-end grime, though the arch jets — their direction on the Argyll's installations being adjusted to increase their effectiveness after initial trials — then remove the dirt and provide an effective rinse.
Automated sequence
The complete automated wash sequence takes about 90 sec. Argyll endeavours to schedule vehicle departures so that no more than three artics are queuing to go through the wash at any time.
Before installing the Ardrox machines, Argyll had discussions with local water and drainage departments. At Welwyn Garden City, the newest depot, Thames Water Authority did not call for the water to be recycled. Water usage is put at only 1,500 litres (330 gallons) a week, for the Welwyn fleet of 40 tractors and 60 trailers. The Ardrox detergent or its equivalent, from competitors like Diversey, is acceptable in the TWA sewage system.
So-called trace heating is provided to prevent the water tanks (exposed to the elements, above ground) freezing in winter. Thus Argyll's ability to wash its vehicles was unaffected by last January's ultra-low temperatures. However, the rinse water left behind froze within minutes, putting tail-lifts out of action and locking trailer brake devises. Washing was therefore reluctantly abandoned for a week or so.
According to Steve Heal, the director responsible for Welwyn operations, keeping the fleet clean performs a secondary, unsung, function of keeping up driver morale. This is evident, he says, in drivers' attitude to the job and in their inclination to report minor defects and keep cab interiors neat and tidy.