Even better cab than Di-Series
Page 36
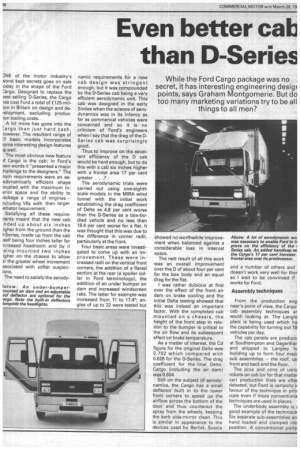
Page 37
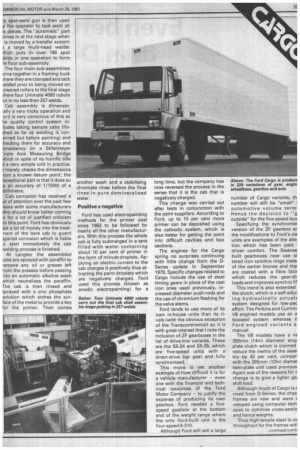
Page 38
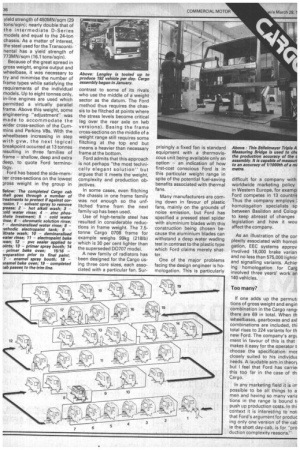
If you've noticed an error in this article please click here to report it so we can fix it.
While the Ford Cargo package was no secret, it has interesting engineering desigt points, says Graham Montgomerie. But do too many marketing variations try to be all things to all men?
DNIE of the motor industry's Norst kept secrets goes on sale -oday in the shape of the Ford :argo. Designed to replace the 3est selling D-Series, the Cargo las cost Ford a total of £125 milion in Britain on design and detelopment, excluding producion tooling costs.
A lot more has gone into the :argo than just hard cash, iowever. The resultant range of ?7 basic models incorporates ;ome interesting design features is well.
The most obvious new feature if Cargo is the cab; in Ford's iwn words it "presented a major :hallenge to the designers." The nain requirements were an aeodynamically efficient shape .oupled with the maximum inerior space and the ability to lackage a range of engines ncluding V8s with their larger achator requirement.
Satisfying all these requirelents meant that the new cab nded up about six inches igher from the ground than the I-Series, made up from the cab self being four inches taller for -icreased headroom and by it eing mounted two inches igher on the chassis to allow )r. the greater wheel movement ssociated with softer suspenions.
The need to satisfy the aerody namic requirements for a new cab design was stringent enough, but it was compounded by the D-Series cab being a very efficient aerodynamic unit. This cab was designed in the early Sixties when the science of aerodynamics was in its infancy as far as commercial vehicles were concerned and so it is no criticism of Ford's engineers when I say that the drag of the DSeries cab was surprisingly good.
Thus to improve on the excellent efficiency of the D cab would be hard enough, but to do this with a cab six inches higher with a frontal area 17 per cent greater . .?
The aerodynamic trials were carried out using one-eighth scale models in the MIRA wind tunnel with the initial work establishing the drag coefficient of Delta as 4.8 per cent worse than the D-Series as a box-bodied vehicle and no less than 18.4 per cent worse for a flat. It was thought that this was due to the difference in corner radii, particularly at the front.
Four basic areas were investigated to come up with an imp rovem ent. These were increased radii on the vertical front corners, the addition of a flared section at the rear (a spoiler collar in Ford terminology), the addition of an under bumper air dam and increased windscreen rake. The latter for example was increased from 11 to 17.4'; angles of up to 22 were tested but showed no worthwhile improvement when balanced against a considerable loss in internal space.
The nett result of all this work was an overall improvement over the D of about four per cent for the box body and an equal drag for the flat.
I was rather dubious at first over the effect of the front air dam on brake cooling and the initial Delta testing showed that this was indeed an important factor. With the completed cab mounted on a chassis, the height of the front step in relation to the bumper is critical to the air flow and its subsequent effect on brake temperature.
As a matter of interest, the Cd figure for the original Delta was 0.702 which compared with 0.628 for the D-Series. The drag coefficient for the final DeltaCargo (including the air dam) was 0.604.
Still on the subject of aerodynamics, the Cargo has a small deflector built in to the lower front corners to speed up the airflow across the bottom of the door and thus counteract the spray from the wheels, keeping the kerb side-mirror clean. This is similar in appearance to the devices used by Berliet, Scania and a number of others and doesn't work very well for ther so I wait to be convinced if works for Ford.
Assembly techniques From the production eng neer's point of view, the Cargo' cab assembly techniques ar worth looking at. The Langle plant is being used which ha the capability for turning out 19 vehicles per day.
The cab panels are produce at Southampton and Dagenhar and shipped to Langley fo building up to form four majo sub assemblies — the roof, cal front and back and the floor.
The pros and cons of using robots on cab (or for that matter car) production lines are ofter debated, but Ford is certainly it favour of the technique in prin ciple even if more conventiona techniques are used in places.
The underbody assembly is good example of the technique Six separate sub-assemblies arE hand loaded and clamped int( position. A conventional porta le spot-weld gun is then used y the operator to tack weld all ix pieces. The "automatic" part omes in at the next stage when is moved by a transfer system a large multi-head welder /Filch puts in over 180 spot ields in one operation to form le floor sub-assembly.
The four main sub-assemblies ome together in a framing buck /here they are clamped and tack /elded prior to being moved on owered rollers to the final stage Mere four Unimate 4000 robots lot in no less than 257 welds.
Cab assembly is dimensioally a very tricky operation and ord is very conscious of this as he quality control system inludes taking sample cabs (finshed as far as welding is conerned but before painting) and hecking them for accuracy and onsistency on a Stifelmeyer -Hole Axis Measuring Bridge vhich in spite of its horrific title
s a very simple unit in practice.
t merely checks the dimensions rom a known datum point; the rxceptional part is that it does so o an accuracy of 1/100th of a nillimetre.
Cab corrosion has received a ot of attention over the past few /ears with some manufacturers vho should know better coming n for a lot of justified criticism Ml this point. Ford has obviously aut a lot of money into the treat-nent of the bare cab to guard against corrosion which is liable .o start immediately the cab Nelding process is finished.
At Langley the assembled :abs are sprayed with paraffin to -emove any oil or grease left 'rpm the presses before passing nto an automatic alkaline wash Nhich neutralises the paraffin, the cab is then rinsed and sprayed with a zinc phosphate solution which etches the surface of the metal to provide a key for the primer. Then comes
another wash and a stabilising chromate rinse before the final rinse in pure demineralised water.
Positive .v negative Ford has used electropainting methods for the primer coat since 1963 to be followed by nearly all the other manufacturers. With this process the whole cab is fully submerged in a tank filled with water containing about 10 per cent of primer in the form of minute droplets. Applying an electric current to the cab charges it positively thus attracting the paint droplets which are negatively charged. Ford used this process (known as anodic electropainting) for a long time, but the company has now reversed the process in the sense that it is the cab that is negatively charged.
This change was carried out after tests in conjunction with the paint suppliers. According to Ford, up to 10 per cent more primer can be deposited using the cathodic system, which is also better for getting the paint into difficult cavities and box sections.
The engines for the Cargo spring no surprises continuing with little change from the DSeries update in September 1979. Specific changes related to Cargo include the use of steel timing gears in place of the cast iron ones used previously, increased diameter push-rods and the use of chromium flashing for the valve stems.
Ford tends to use more of its own in-house units than its rivals (with the obvious exception of the Transcontinental) so it is with great interest that I note the inclusion of ZF gearboxes in the list of drive-line variants. These are the S5-24 and S5-35, which are five-speed units with a direct-drive top gear and fully synchronised.
This move is yet another example of how difficult it is for a vehicle manufacturer — even one with the financial and technical resources of the Ford Motor Company — to justify the expense of producing its own gearbox. Ford needed a fivespeed gearbox at the bottom end of the weight range where the only Ford-built unit is the four-speed '4-310.
Although Ford will sell a large number of Cargo variants, th number will still be "small" i automotive volume term: Hence the decision to "g outside" for the five-speed box Specifying the synchromes. version of the ZF gearbox ar the modifications to Ford's ovs units are examples of the atte tion which has been paid driver comfort. The Swanse built gearboxes now use si tered iron synchro rings instei of the earlier bronze and the: are coated with a fibre facir which reduces the gear-sh loads and improves synchro lif This trend is also extended the clutch, which is a self-adju: ing hydraulically actuate system designed for low-pec effort. The Perkins and Cummi: V8 erigined models use an a boosted system whereas tl Ford engined variants a manual.
The V8 models have a nE 350mm (14in) diameter sing plate clutch which is claimed reduce the inertia of the asser bly by 40 per cent, compar with the 305mm (12in) diamer twin-plate unit used previous Again one of the reasons for t change is to give a ligher gei shift load.
Although much of Cargo is c rived from D-Series, the chas: frames are new and were c veloped using computer tech ques to optimise cross-sectio and hence weights.
Thus high-tensile steel is us throughout for the frames witl yield strength of 450MN/sqm (29 tons/sqin); nearly double that of the intermediate D-Series models and equal to the 24-ton chassis. As a matter of interest, the steel used for the Transcontinental has a yield strength of 773MN/sqm (16.1 tons/sqin).
Because of the greatspread in gross weight, engine output and wheelbase, it was necessary to try and minimise the number of frame types while satisfying the requirements of the individual models. Up to eight tonnes only, in-line engines are used which permitted a virtually parallel frame. Above this weight, some engineering "adjustment" was made to accommodate the wider cross-section of the Cummins and Perkins V8s, With the wheelbases increasing in step with gvw, the next logical breakpoint occurred at 13 tonnes resulting in three families of frame shallow, deep and extra deep, to quote Ford terminology.
Ford has based the side-member cross-sections on the lowest gross weight in the group in Below: The completed Cargo cab ;hell goes through a number of treatments to protect if against cor-osion. 1 solvent spray to remove 7rease; 2 hot alkali wash; 3 ;old water rinse; 4 zinc phos 'hate treatment; 5 cold water
-inse; 6 chromatic solution rinse; 7 demineralised water rinse; 8 :athodic electropaint tank; 9 iltrate wash; 10 demineralised vater rinse; 11 electro paint bake
yen; 12 pvc sealer applied to oints; 13 primer spray booth; 14
primer bake overt; 15/16 -2reparation prior to final paint;
'7 enamel spray booth; 18 ?namel bake oven; 19 completed :ab passes to the trim line.
contrast to some of its rivals who use the middle of a weight sector as the datum. The Ford method thus requires the chassis to be flitched at points where the stress levels become critical (eg over the rear axle on Iwb versions). Basing the frame cross-sections on the middle of a weight range still requires some flitching at the top end but means a heavier than necessary frame at the bottom.
Ford admits that this approach is not perhaps "the most technically elegant solution" but argues that it meets the weight, complexity and production objectives.
In some cases, even flitching the chassis in one frame family was not enough so the unflitched frame from the next family up has been used.
Use of high-tensile steel has resulted in considerable reductions in frame weight. The 7.5tonne Cargo 0708 frame for example weighs 99kg (2181b) which is 30 per cent lighter than the superseded D0707 model.
A new family of radiators has been designed for the Cargo using three core sizes, each associated with a particular fan. Sur prisingly a fixed fan is standard equipment with a thermoviscous unit being available only an option an indication of how first-cost conscious Ford is in this particular weight range in spite of the potential fuel-saving benefits associated with thermal fans.
Many manufacturers are coming down in favour of plastic fans, mainly on the grounds of noise emission, but Ford has specified a pressed steel spider with aluminium blades with this construction being chosen because the aluminium blades can withstand a deep water wading test in contrast to the plastic type which Ford claims merely shatter.
One of the major problems facing the design engineer is homologation. This is particularly difficult for a company with worldwide marketing policy in Western Europe, for exampl Ford competes in 13 countriE Thus the company employs homologation specialists sp between Basildon and Cologr to keep abreast of changes legislation and how it wou affect the company.
As an illustration of the cor plexity associated with homol, gation, EEC systems approv involved 18,000 brake varian and no less than 575,000 lightir and signalling variants. Achie ing homologation for Carg involved three years' work an 140 vehicles.
Too many?
If one adds up the permuti tions of gross weight and engin combination in the Cargo rang( there are 69 in total. When th wheeibases, gearboxes and axl combinations are included, thi total rises to 224 variants for th new Ford. The company's argL ment in favour of this is that makes it easy for the operator t choose the specification MO5 closely suited to his individua needs. A laudable aim in theory but I feel that Ford has carriel
this too far in the case of th, Cargo.
In any marketing field it is in possible to be all things to a men and having so many varia tions in the range is bound ti push up production costs. In thi context it is interesting to not that Ford's argument for produc ing only one version of the cab ie the short day-cab, is for "pro duction complexity reasons."