Driving in the
Page 25
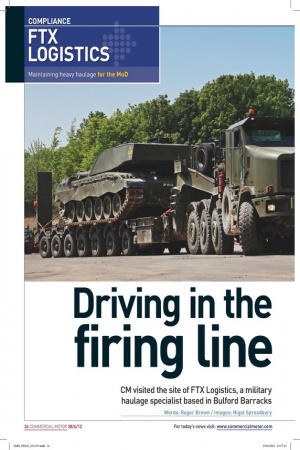
Page 26
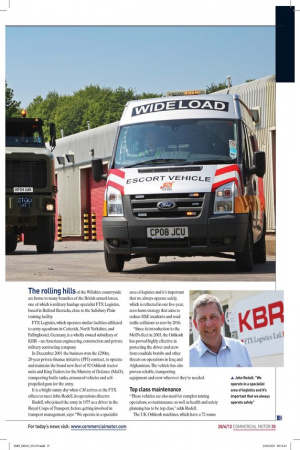
Page 27
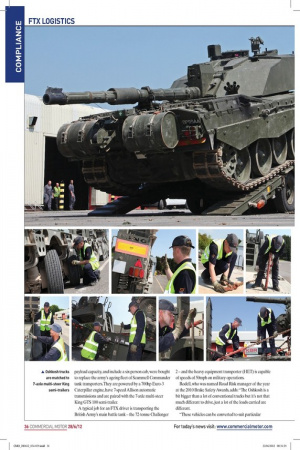
Page 28
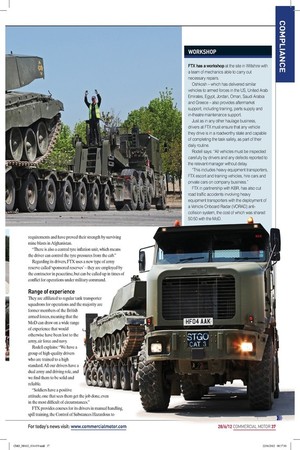
Page 29
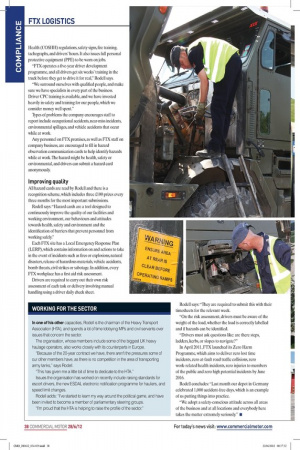
Page 30
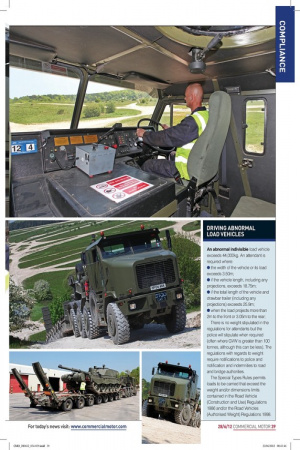
If you've noticed an error in this article please click here to report it so we can fix it.
firing line
CM visited the site of FTX Logistics, a military haulage specialist based in Bulford Barracks
Words: Roger Brown / Images: Nigel Spreadbury
The rolling hills of the Wiltshire countryside are home to many branches of the British armed forces, one of which is military haulage specialist FTX Logistics, based in Bulford Barracks, close to the Salisbury Plain training facility.
FTX Logistics, which operates similar facilities affiliated to army squadrons in Catterick, North Yorkshire, and Fallingbostel, Germany, is a wholly owned subsidiary of KBR – an American engineering, construction and private military contracting company.
In December 2001 the business won the £290m, 20-year private finance initiative (PFI) contract, to operate and maintain the brand new fleet of 92 Oshkosh tractor units and King Trailers for the Ministry of Defence (MoD), transporting battle tanks, armoured vehicles and selfpropelled guns for the army.
It is a bright sunny day when CM arrives at the FTX offices to meet John Rodell, its operations director.
Rodell, who joined the army in 1975 as a driver in the Royal Corps of Transport, before getting involved in transport management, says: “We operate in a specialist area of logistics and it’s important that we always operate safely, which is reflected in our five-year, zero-harm strategy that aims to reduce HSE incidents and road traffic collisions to zero by 2016.
“Since its introduction to the MoD’s fleet in 2003, the Oshkosh has proved highly effective in protecting the driver and crew from roadside bombs and other threats on operations in Iraq and Afghanistan. The vehicle has also proven reliable, transporting equipment and crew wherever they’re needed.
Top class maintenance
“These vehicles are also used for complex mining operations, so maintenance as well as health and safety planning has to be top class,” adds Rodell.
The UK Oshkosh machines, which have a 72-tonne payload capacity, and include a six-person cab, were bought to replace the army’s ageing fleet of Scammell Commander tank transporters. They are powered by a 700hp Euro-3 Caterpillar engine, have 7-speed Allison automatic transmissions and are paired with the 7-axle multi-steer King GTS 100 semi-trailer.
A typical job for an FTX driver is transporting the British Army’s main battle tank – the 72-tonne Challenger 2 – and the heavy equipment transporter (HET) is capable of speeds of 50mph on military operations.
Rodell, who was named Road Risk manager of the year at the 2010 Brake Safety Awards, adds: “The Oshkosh is a bit bigger than a lot of conventional trucks but it’s not that much different to drive, just a lot of the loads carried are different.
“These vehicles can be converted to suit particular requirements and have proved their strength by surviving mine blasts in Afghanistan.
“There is also a central tyre inflation unit, which means the driver can control the tyre pressures from the cab.” Regarding its drivers, FTX uses a new type of army reserve called ‘sponsored reserves’ – they are employed by the contractor in peacetime, but can be called up in times of conflict for operations under military command.
Range of experience
They are affiliated to regular tank transporter squadrons for operations and the majority are former members of the British armed forces, meaning that the MoD can draw on a wide range of experience that would otherwise have been lost to the army, air force and navy.
Rodell explains: “We have a group of high-quality drivers who are trained to a high standard. All our drivers have a dual army and driving role, and we find them to be solid and reliable.
“Soldiers have a positive attitude, one that sees them get the job done, even in the most difficult of circumstances.” FTX provides courses for its drivers in manual handling, spill training, the Control of Substances Hazardous to Health (COSHH) regulations, safety signs, fire training, tachographs, and drivers’ hours. It also issues full personal protective equipment (PPE) to be worn on jobs.
“FTX operates a five-year driver development programme, and all drivers get six weeks’ training in the truck before they get to drive it for real,” Rodell says.
“We surround ourselves with qualified people, and make sure we have specialists in every part of the business. Driver CPC training is available, and we have invested heavily in safety and training for our people, which we consider money well spent.” Types of problems the company encourages staff to report include occupational accidents, near-miss incidents, environmental spillages, and vehicle accidents that occur while at work.
Any personnel on FTX premises, as well as FTX staff on company business, are encouraged to fill in hazard observation communication cards to help identify hazards while at work. The hazard might be health, safety or environmental, and drivers can submit a hazard card anonymously.
Improving quality
All hazard cards are read by Rodell and there is a recognition scheme, which includes three £100 prizes every three months for the most important submissions.
Rodell says: “Hazard cards are a tool designed to continuously improve the quality of our facilities and working environment, our behaviours and attitudes towards health, safety and environment and the identification of barriers that prevent personnel from working safely.” Each FTX site has a Local Emergency Response Plan (LERP), which contains information on and actions to take in the event of incidents such as fires or explosions, natural disasters, release of hazardous materials, vehicle accidents, bomb threats, civil strikes or sabotage. In addition, every FTX workplace has a first aid risk assessment.
Drivers are required to carry out their own risk assessment of each task or delivery involving manual handling using a driver daily check sheet. Rodell says: “They are required to submit this with their timesheets for the relevant week.
“On the risk assessment, drivers must be aware of the weight of the load, whether the load is correctly labelled and if hazards can be identified.
“Drivers must ask questions like: are there steps, ladders, kerbs, or slopes to navigate?” In April 2011, FTX launched its Zero Harm Programme, which aims to deliver zero lost time incidents, zero at-fault road traffic collisions, zero work-related health incidents, zero injuries to members of the public and zero high potential incidents by June 2016.
Rodell concludes: “Last month our depot in Germany celebrated 1,000 accident-free days, which is an example of us putting things into practice.
“We adopt a safety-conscious attitude across all areas of the business and at all locations and everybody here takes the matter extremely seriously.” ■
WORKSHOP
FTX has a workshop at the site in Wiltshire with a team of mechanics able to carry out necessary repairs.
Oshkosh – which has delivered similar vehicles to armed forces in the US, United Arab Emirates, Egypt, Jordan, Oman, Saudi Arabia and Greece – also provides aftermarket support, including training, parts supply and in-theatre maintenance support.
Just as in any other haulage business, drivers at FTX must ensure that any vehicle they drive is in a roadworthy state and capable of completing the task safely, as part of their daily routine.
Rodell says: “All vehicles must be inspected carefully by drivers and any defects reported to the relevant manager without delay.
“This includes heavy equipment transporters, FTX escort and training vehicles, hire cars and private cars on company business.” FTX in partnership with KBR, has also cut road traffic accidents involving heavy equipment transporters with the deployment of a Vehicle Onboard Radar (VORAD) anticollision system, the cost of which was shared 50:50 with the MoD.
WORKING FOR THE SECTOR
In one of his other capacities, Rodell is the chairman of the Heavy Transport Association (HTA), and spends a lot of time lobbying MPs and civil servants over issues that concern the sector.
The organisation, whose members include some of the biggest UK heavy haulage operators, also works closely with its counterparts in Europe.
“Because of the 20-year contract we have, there aren’t the pressures some of our other members have, as there is no competition in the area of transporting army tanks,” says Rodell.
“This has given me a little bit of time to dedicate to the HTA.” Issues the organisation has worked on recently include raising standards for escort drivers, the new ESDAL electronic notification programme for hauliers, and speed limit changes.
Rodell adds: “I’ve started to learn my way around the political game, and have been invited to become a member of parliamentary steering groups.
“I’m proud that the HTA is helping to raise the profile of the sector.”
DRIVING ABNORMAL LOAD VEHICLES
An abnormal indivisible load vehicle exceeds 44,000kg. An attendant is required where: • the width of the vehicle or its load exceeds 3.50m; • if the vehicle length, including any projections, exceeds 18.75m; • if the total length of the vehicle and drawbar trailer (including any projections) exceeds 25.9m; • when the load projects more than 2m to the front or 3.05m to the rear; There is no weight stipulated in the regulations for attendants but the police will stipulate when required (often where GVW is greater than 100 tonnes, although this can be less). The regulations with regards to weight require notifications to police and notification and indemnities to road and bridge authorities.
The Special Types Rules permits loads to be carried that exceed the weight and/or dimensions limits contained in the Road Vehicle (Construction and Use) Regulations 1986 and/or the Road Vehicles (Authorised Weight) Regulations 1998.