State of the art
Page 21
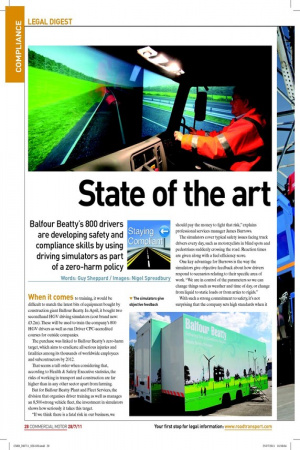
Page 23

If you've noticed an error in this article please click here to report it so we can fix it.
Balfour Beatty’s 800 drivers are developing safety and compliance skills by using driving simulators as part of a zero-harm policy
Words: Guy Sheppard / Images: Nigel Spreadbury When it comes to training, it would be dificult to match the latest bits of equipment bought by objective feedback
construction giant Balfour Beatty. In April, it bought two secondhand HGV driving simulators (cost brand new: £3.2m). These will be used to train the company’s 800 HGV drivers as well as run Driver CPC-accredited courses for outside companies.
The purchase was linked to Balfour Beatty’s zero-harm target, which aims to eradicate all serious injuries and fatalities among its thousands of worldwide employees and subcontractors by 2012.
That seems a tall order when considering that, according to Health & Safety Executive statistics, the risks of working in transport and construction are far higher than in any other sector apart from farming.
But for Balfour Beatty Plant and Fleet Services, the division that organises driver training as well as manages an 8,500-strong vehicle leet, the investment in simulators shows how seriously it takes this target.
“If we think there is a fatal risk in our business, we should pay the money to ight that risk,” explains professional services manager James Burrows.
The simulators cover typical safety issues facing truck drivers every day, such as motorcyclists in blind spots and pedestrians suddenly crossing the road. Reaction times are given along with a fuel eficiency score.
One key advantage for Burrows is the way the simulators give objective feedback about how drivers respond to scenarios relating to their speciic area of work. “We are in control of the parameters so we can change things such as weather and time of day, or change from liquid to static loads or from artics to rigids.” With such a strong commitment to safety, it’s not surprising that the company sets high standards when it comes to compliance. Divisional MD Steve Farmer says this is partly down to business reputation. “If things go wrong, you get a lot of coverage in everything you see. Compliance is about people going home from work in the same shape and itness they arrived in. That is the biggest beneit for us.” One example of the company’s innovative approach to compliance has been to issue area transport engineers with digital pens so that when they carry out safety inspections their reports can be immediately iled centrally and action taken if necessary.
“In the past there was a time lag between the vehicle inspection and putting the paper forms in the post,” says Farmer. “One of the reasons we have kept KPIs on was to ensure all compliance paperwork is up-to-date.” Rather than having to retrain engineers to enter the information on a computer, Farmer says the pens allow them to continue with hand-written reports.
Another innovation, introduced 18 months ago, has been developed in conjunction with bodybuilders and crane manufacturers. It involves itting load cells to tipper grabber operations so that when a crane has loaded the vehicle to its designated weight, any additional loading is stopped. Farmer says this avoids situations where drivers can be pressurised to go over the limit. And if the vehicle continues to be loaded by another means, this will be communicated to the trafic ofice via telematics.
The company plans to strengthen its use of telematics to improve compliance on the road. Farmer says the technology has been used for operational necessities. “With a highways maintenance contract, for example, indicators will show the local authority where gritters have been and when they have been salt spreading.” One example of the new approach is to monitor tyre pressures remotely so that if they fall by more than 10%, the vehicle can be intercepted on the road to correct this. Farmer also wants to use telematics to build up a better picture of how drivers are performing, by keeping tabs on the incidence of harsh braking and acceleration.
“When people know that telematics are in the vehicle, it is enough for them to drive properly. When we see infringements, we do driver training.” But Farmer is wary of pushing the idea too far. “We have to ensure we’re doing it for the right reasons rather than being like Big Brother.” The company already has an effective tool for targeting drivers who need retraining. The driver risk index, developed by Cranield University, assesses a variety of factors that affect the way people drive, including their age, annual mileage, work-related stress levels and how focused they are on driving.
“If they come up with a high score across the board, we will put them straight on a course,” says Burrows. “We have been doing that for three years and have identiied approximately 25% of drivers as high risk.” So far, approximately 6,000 drivers have beneited, including about half of the irm’s HGV drivers.
Collision rates among these employees are said to have fallen 40%. ■