SECOND TIME AROUND
Page 84
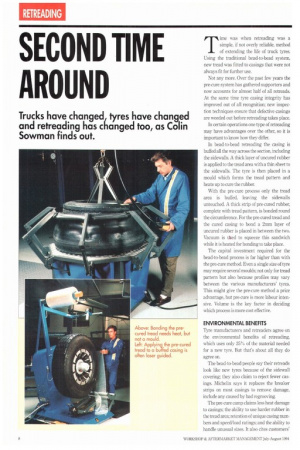
Page 85
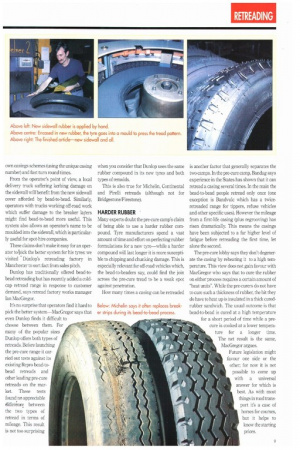
If you've noticed an error in this article please click here to report it so we can fix it.
Trucks have changed tyres have changed and retreading has dianged too, as Cohn Sowman finds out.
Time was when retreading was a simple, if not overly reliable, method of extending the life of truck tyres. Using the traditional bead-to-bead system, new tread was fitted to casings that were not always fit for further use.
Not any more, Over the past few years the pre-cure system has gathered supporters and now accounts for almost half of all retreads. At the same time tyre casing integrity has improved out of all recognition; new inspection techniques ensure that defective casings are weeded out before retreading takes place.
In certain operations one type of retreading may have advantages over the other, so it is important to know how they differ.
In bead-to-bead retreading the casing is buffed all the way across the section, including the siciewalls. A thick layer of uncured rubber is applied to the tread area with a thin sheet to the sidewails. The tyre is then placed in a mould which forms the tread pattern and heats up to cure the rubber.
With the pre-cure process only the tread area is buffed, leaving the sidewalls untouched. A thick strip of pre-cured rubber, complete with tread pattern, is bonded round the circumference. For the pre-cured tread and the cured casing to bond a 2rnm layer of uncured rubber is placed in between the two. Vacuum is tked to squeeze this sandwich while it is heated for bonding to take place.
The capital investment required for the bead-to-bead process is far higher than with the pre-cure method. Even a single size of tyre may require several moulds; not only for tread pattern but also because profiles may vary between the various manufacturers' tyres. This might give the pre-cure method a price advantage, but pre-cure is more labour intensive. Volume is the key factor in deciding which process is more cost effective.
ENVIRONMENTAL BENEFITS
Tyre manufacturers and retreaders agree on the environmental benefits of retreading, which uses only 25% of the material needed for a new tyre. Hut that's about all they do agree on.
The bead-to-bead people say their retreads look like new tyres because of the sidewall covering; they also claim to reject fewer casings. Michelin says it replaces the breaker strips on most casings to remove damage, include any caused by bad regrooving.
The pre-cure camp claims less heat damage to casings; the ability to use harder rubber in the tread area; retention of unique casing numbers and speed/load ratings; and the ability to handle unusual sizes. It also cites customers' own casings schemes (using the unique casing number) and fast turn round times, From the operator's point of view, a local delivery truck suffering kerbing damage on the sidewall will benefit from the new sidewall cover afforded by bead-to-bead. Similarly, operators with trucks working off-road work which suffer damage to the breaker laYers might find bead-to-bead more useful. This system also allows an operator's name to be moulded into the sidewall, which is particularly useful for spot-hire companies.
These claims don't make it easy for an operator to i)ick the better system for his tyres; we visited Dunlop's retreading factory in Manchester to sort fact from sales pitch.
Dunlop has traditionally offered bead-tobead retreading but has recently added a coldcap retread range in response to customer demand, says retread factory works manager Ian MacGregor, It's no surprise that operators find it hard to pick the better system—MacGregor says that even Dunlop finds it difficult to choose between them. For many of the popular sizes Dunlop offers both types of retreads. Before launching the pre-cure range it carried out tests against its existing Repro bead-tobead retreads and other leading pre-cure retreads on the market. These tests found no appreciable difference between the two types of retread in terms of mileage. This result is not too surprising when you consider that Dunlop uses the same rubber compound in its new tyres and both types of remolds, This is also true for Michelin, Continental and Pirelli retreads (although not for Bridgestone/Firestone).
HARDER RUBBER •
Many experts doubt the pre-cure camp's claim of being able to use a harder rubber compound. Tyre manufacturers spend a vast amount of time and effort on perfecting rubber formulations for a new tyre—while a harder compound will last longer it is more susceptible to chipping and chunking damage. This is especially relevant for off-road vehicles which, the bead-to-headers say, could find the join across the pre-cure tread to be a weak spot against penetration.
How many times a casing can be retreaded is another factor that generally separates the two camps. In the pre-cure camp, Bandag says experience in the States has shown that it can retread a casing several times. In the main the bead-to-bead people retread only once (one exception is Bandvulc which has a twiceretreaded range for tippers, refuse vehicles and other specific uses). However the mileage from a first-life casing (plus regrooving) has risen dramatically. This means the casings have been subjected to a far higher level of fatigue before retreading the first time, let alone the second.
The pre-cure lobby says they don't degenerate the casing by reheating it to a high temperature. This view does not gain favour with MacGregor who says that to cure the rubber on either process requires a certain amount of "heat units". While the pre-curers do not have to cure such a thickness of rubber, the bit they do have to heat up is insulated in a thick curedrubber sandwich. The usual outcome is that bead-to-bead is cured at a high temperature for a short period of time while a precure is cooked at a lower temperature for a longer time. The net result is the same, MacGregor argues.
Future legislation might favour one side or the other; for now it is not possible to come up with a universal answer for which is best. As with most things in road transport it's a case of horses for courses, but it helps to know the starting prices.