COMPUTERS IN TRANSPORT
Page 48
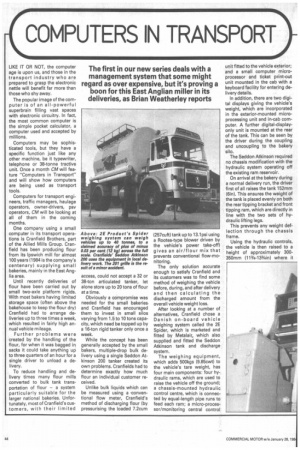
Page 49
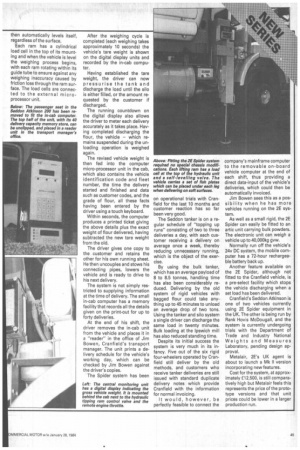
If you've noticed an error in this article please click here to report it so we can fix it.
The first in our new series deals with a management system that some might regard as over expensive, but it's proving a boon for this East Anglian miller in its deliveries, as Brian Weatherley reports
LIKE IT OR NOT, the computer age is upon us, and those in the transport industry who are prepared to grasp the electronic nettle will benefit far more than those who shy away.
The popular image of the computer is of an all-powerful superbrain filling vast spaces with electronic circuitry. In fact, the most common computer is the simple pocket calculator, a computer used and accepted by millions.
Computers may be sophisticated tools, but they have a specific function just like any other machine, be it typewriter, telephone or 38-tonne tractive unit. Once a month CM will feature "Computers in Transport" and will show how computers are being used as transport tools.
Computers for transport engineers, traffic managers, haulage operators, owner-drivers, psv operators, CM will be looking at all of them in the coming months.
One company using a small computer in its transport operations is Cranfield Brothers, part of the Allied Mills Group. Cranfield has been producing flour from its Ipswich mill for almost 100 years (1984 is the company's centenary) supplying small bakeries, mainly in the East Anglia area.
Until recently deliveries of flour have been carried out by small two-axle platform rigids. With most bakers having limited storage space (often above the bakehouse to keep the flour dry) Cranfield had to arrange deliveries up to three times a week, which resulted in fairly high annual vehicle mileage.
Further problems were created by the handling of the flour, for when it was bagged in sacks it could take anything up to three quarters of an hour for a single driver to unload a delivery.
To reduce handling and delivery times many flour mills converted to bulk tank transportation of flour — a system particularly suitable for the larger national bakeries, Unfortunately, most of Cranfield's customers, with their limited access, could not accept a 32 or 38-ton articulated tanker, let alone store up to 20 tons of flour at a time.
Obviously a compromise was needed for the small bakeries. and Cranfield has encouraged them to invest in small silos varying from 1.5 to 10 tons capacity, which need be topped up by a 16-ton rigid tanker only once a week.
While the concept has been generally accepted by the small bakers, multiple-drop bulk delivery using a single Seddon Atkinson 200 tanker created its own problems. Cranfields had to determine exactly how much flour an individual customer received.
Unlike bulk liquids which can be measured using a -conventional flow meter, Cranfield's method of discharging flour (by pressurising the loaded 7.2cum (257cuft) tank up to 13.1psi using a Rootes-type blower driven by the vehicle's power take-off) gives an air/flour mix that prevents conventional flow-monitoring.
The only solution accurate enough to satisfy Cranfield and its customers was to find some method of weighing the vehicle before, during, and after delivery and then calculating the discharged amount from the overall vehicle weight loss.
After looking at a number of alternatives, Cranfield chose a Danish on-board vehicle weighing system called the 2E Spider, which is marketed and fitted by Metalair, which also supplied and fitted the Seddon Atkinson tank and discharge system.
The weighing equipment, which adds 500kgs (9.85cwt) to the vehicle's tare weight, has four main components: four hydraulic rams, which are used to raise the vehicle off the ground; a chassis-mounted hydraulic control centre, which is connected by equal-length pipe runs to feed each ram; a micro-processor/monitoring central control unit fitted to the vehicle exterior; and a small computer microprocessor and ticket print-out unit mounted in the cab with a keyboard facility for entering delivery details.
In addition, there are two digital displays giving the vehicle's weight, which are incorporated in the exterior-mounted microprocessing unit and in-cab com puter. A further digital-display only unit is mounted at the rear of the tank. This can be seen by the driver during the coupling and uncoupling to the bakery silo.
The Seddon Atkinson required no chassis modification with the hydraulic system operating off the existing ram reservoir.
On arrival at the bakery during a normal delivery run, the driver first of all raises the tank 152mm (6in). This ensures the weight of the tank is placed evenly on both the rear tipping bracket and front tipping ram, which are directly in line with the two sets of hydraulic lifting legs.
This prevents any weight deflection through the chassis frame.
Using the hydraulic controls, the vehicle is then raised to a height of approximately 300350mm (113/4-133/4in) where it then automatically levels itself, regardless of the surface.
Each ram has a cylindrical load cell in the top of its mounting and when the vehicle is level the weighing process begins, with each ram rotating within its guide tube to ensure against any weighing inaccuracy caused by friction loss through the ram surface. The load cells are connected to the external microprocessor unit. After the weighing cycle is completed (each weighing takes approximately 10 seconds) the vehicle's tare weight is shown on the digital display units and recorded by the in-cab computer.
Having established the tare weight, the driver can now pressurise the tank and discharge the load until the silo is either filled, or the amount requested by the customer if discharged.
The running countdown on the digital display also allows the driver to meter each delivery accurately as it takes place. Having completed discharging the flour, the vehicle — which remains suspended during the unloading operation is weighed again.
The revised vehicle weight is then fed into the computer micro-processor unit in the cab, which also contains the vehicle identification code and fleet number, the time the delivery started and finished and data such as customer codes, and the grade of flour, all these facts having been entered by the driver using a touch keyboard.
Within seconds, the computer produces a printed ticket giving the above details plus the exact weight of flour delivered, having subtracted the new tare weight from the old.
The driver gives one copy to the customer and retains the other for his own running sheet. He then uncouples and stows his connecting pipes, lowers the vehicle and is ready to drive to his next delivery.
The system is not simply restricted to supplying information at the time of delivery. The small in-cab computer has a memory facility that records all the details given on the print-out for up to forty deliveries.
At the end of his shift, the driver removes the in-cab unit from the vehicle and places it in a "reader" in the office of Jim Bowen, Cranfield's transport manager. The unit prints a delivery schedule for the vehicle's working day, which can be checked by Jim Bowen against the driver's copies.
The Spider system has been on operational trials with Cranfield for the last 10 months and customer reaction has so far been very good.
The Seddon tanker is on a regular schedule of "topping up runs" consisting of two to three deliveries a day, with each customer receiving a delivery on average once a week, thereby reducing unnecessary running, which is the object of the exercise.
By using the bulk tanker, which has an average payload of 8 to 8.5 tonnes, handling time has also been considerably reduced. Delivering by the old system of rigid vehicles with bagged flour could take anything up to 45 minutes to unload an average drop of two tons. Using the tanker and silo system a single driver can discharge the same load in twenty minutes. Bulk loading at the Ipswich mill has also reduced standing time.
Despite its initial success the system is very much in its infancy. Five out of the six rigid four-wheelers operated by Cranfield still deliver by the old methods, and customers who receive tanker deliveries are still issued with standard duplicate delivery notes which provide Cranfield with the information for normal invoicing.
It would, however, be perfectly feasible to connect the company's mainframe computer to the removable on-board vehicle computer at the end of each shift, thus providing a direct data-input of the vehicle's deliveries, which could then be automatically invoiced.
Jim Bowen sees this as a possibility when he has more vehicles running on the 2E system.
As well as a small rigid, the 2E Spider can easily be fitted to an artic unit carrying bulk powders. The electronic unit can weigh a vehicle up to 40,000kg gvw, Normally run off the vehicle's 24v DC system, the mobile computer has a 72-hour rechargeable battery back up.
Another feature available on the 2E Spider, although not fitted to the Cranfield vehicle, is a pre-select facility which stops the vehicle discharging when a set load has been delivered.
Cranfield's Seddon Atkinson is one of two vehicles currently using 2E Spider equipment in the UK. The other is being run by Rank Hovis McDougall, and the system is currently undergoing trials with the Department of Trade and Industry National Weights and Measures Laboratory, pending design approval.
Metalair, 2E's UK agent is about to launch a Mk II version incorporating new features.
Cost for the system, at approximately £12,500, is still comparatively high but Metalair feels this represents the price of the prototype versions and that unit prices could be lower in a larger production run.