Talking of Freightliners
Page 36
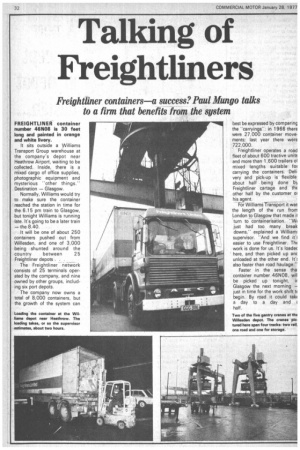
Page 37
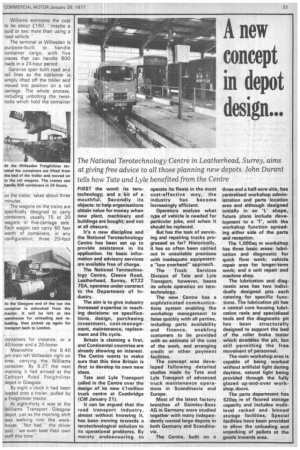
If you've noticed an error in this article please click here to report it so we can fix it.
Freightliner containers—a success? Paul Mungo talks to a firm that benefits from the system
FREIGHTLINER container number 46N08 is 30 feet long and painted in orange and white livery.
It sits outside a Williams Transport Group warehouse at the company's depot near Heathrow Airport, waiting to be collected. Inside, there is a mixed cargo of office supplies, photographic equipment and mysterious "other things." Destination — Glasgow.
Normally, Williams would try to make sure the container reached the station in time for the 6.15 pm train to Glasgow, but tonight Williams is running late. It's going to be a later train — the 8.40.
It will be one of about 250 containers pushed out from Willesden, and one of 3,000 being shunted around the country between 25 Freightliner depots . .
The Freightliner network consists of 25 terminals operated by the company, and nine owned by other groups, including six port depots.
The company now owns a total of 8,000 containers, but the growth of the system can
best be expressed by comparing the -carryings": in 1966 there were 27,000 container movements: last year there were 722,000.
Freightliner operates a road fleet of about 600 tractive units and more than 1,600 trailers ol mixed lengths suitable for carrying the containers. Delivery and pick-up is flexible: about half being done by Freightliner cartage and thE other half by the customer oi his agent.
For Williams. riansport it was the length of the run from London to Glasgow that made ii turn to containerisation. "Wr just had too many break downs," explained a William: supervisor. -And we find it'r easier to use Freightliner. Thc work is done for us. It's loadec here, and then picked up anc unloaded at the other end. It'; also faster than road haulage."
Faster in the sense tha container number 46N08, wil be picked up tonight, ir Glasgow the next morning — just in time for the work shift tr begin. By road it could tak( a day to a day and half.
Williams estimates the cost to be about £160, -maybe a quid or two more than using a road vehicle.'"
The terminal at Willesden is purpose-built to handle container cargo, with five cranes that can handle 800 loads in a 24-hour period.
Gantries span both road and rail lines so the container is simply lifted off the trailer and moved into position on a rail carriage_ The whole process, including unbolting the twistlocks which hold the container on the trailer, takes about three minutes.
The wagons on the trains are specifically designed to carry containers, usually 15 or 20 wagons in five-carriage sets. Each wagon can carry 60 feet worth of containers, in any configuration; three 20-foot containers for instance, or a 40-footer and a 20-footer_ Meanwhile . . the 8.40 pm train left Willesden right on time, carrying the Williams container. By 6.27 the next morning it had arrived at the Cathcart Road Freightliner depot in Glasgow.
By eight o'clock it had been loaded onto a trailer, pulled by a Freightliner tractor_ At eight-thirty it was at the 'Williams Transport Glasgow depot, lust as the morning shift was walking into the ware
house. Not bad," the driver said, -we even beat their own staff this time."
FIRST the word: its terotechnology; and a bit of a mouthful. Secondly its objects: to help organisations obtain value for money when new plant, machinery and buildings are bought; and not at all obscure.
Its a new discipline and the National Terotechnology Centre has been set up to provide assistance in its application. Its basic information and advisory services are available free of charge.
The National Terotechnology Centre, Cleeve Road, Le_atherhead, Surrey, KT22 7SA, operates under contract to the Department of Industry.
The aim is to give industry increased expertise in reaching decisions: on specifications, design, purchasing investment, cost-management, maintenance, replacement and life cycle.
Britain is claiming a first, and Continental countries are already showing an interest. The Centre wants to make sure that this time Britain is first to develop its own new ideas.
Tate and Lyle Transport called in the Centre over the design of its new El million truck centre at Coatbridge (CM January 21).
It can be argued that the road transport industry, almost without knowing it, has been moving towards a terotechnological solution to its operational problems. By merely endeavouring to operate its fleets in the most cost-effective way, the industry has become increasingly efficient.
Operators analyse what lype of vehicle is needed for particular jobs, and when it should be replaced.
But has the task of servicing and repairing trucks progressed as far? Historically, it has so often been carried out in unsuitable premises with inadequate equipment: a "low overhead" approach.
The Truck Services Division of Tate and Lyle Transport, however, bases its whole operation on terotechnology.
The new Centre has a sophisticated communications system enabling the workshop management to liaise quickly with all parties, including parts availability and finance, enabling customers to be provided with an estimate of the cost of the work, and arranging credit or other payment facilities_ The concept was developed following detailed studies made by Tate and Lyle Transport of advanced truck maintenance operations in Scandinavia and Europe.
Most of the latest factory branches of Daimley-Benz AG in Germany were studied together with many independently owned large depots in both Germany and Scandinavia.
The Centre, built on a three and a half-acre site, has centralised workshop administration and parts location area and although designed initially in an shape, future plans include development to a 'T', with the workshop function spreading either side of the parts and reception.
The 1,000sq m workshop has three basic areas: lubrication and diagnostic for quick flow work; vehicle repair area for longer-term work; and a unit repair and machine shop.
The lubrication and diagnostic area has two individually designed pits each catering for specific functions. The lubrication pit has a central core housing lubrication reels and specialised tools and the diagnostic pit has been structurally designed to support the bed of the roller brake tester which straddles the pit, but still permitting the free movement of personnel.
The main workshop area is capable of being worked without artificial light during daytime, natural light being provided through the fully glazed up-and-over workshop doors.
The parts department has 520sq m of floored storage capacity and includes multilevel racked and binned storage facilities. Special facilities have been provided to allow the unloading and unpacking of pallets at the goods inwards area.