es watch recon
Page 91
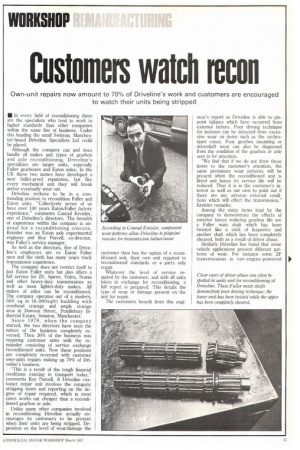
Page 92
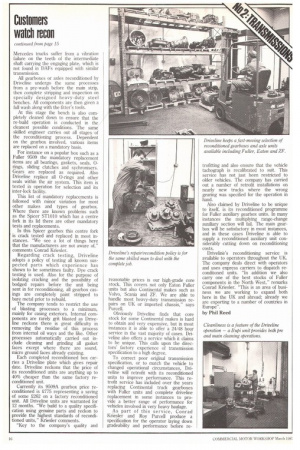
If you've noticed an error in this article please click here to report it so we can fix it.
Own-unit repairs now amount to 7CM of Driveline's work and customers are encouraged to watch their units being stripped
• In every field of reconditioning there are the specialists who tend to work to higher standards than other companies within the same line of business. Under this heading the small Swinton, Manchester-based Driveline Specialists Ltd could be placed.
Although the company can and does handle all makes and types of gearbox and axle reconditioning, Driveline's specialities are larger units, especially Fuller gearboxes and Eaton axles. In the UK these two names have developed a near bullet-proof reputation, but like every mechanical unit they will break and/or eventually wear out.
Driveline reckons to be in a commanding position to recondition Fuller and Eaton units. "Collectively seven of us have over 100 years Eaton/Fuller factory experience," comments Conrad Kreisler, one of Driveline's directors. The breadth of experience within the company is unusual for a reconditioning concern. Kreisler was an Eaton axle experimental engineer and Roy Purcell, co-director, was Fuller's service manager.
As well as the directors, five of Driveline's employees are ex Eaton Fuller men and the sixth has many years truck transmission experience.
The company does not restrict itself to just Eaton Fuller units but also offers a full service for ZF, Spicer, Volvo, Scania and other heavy-duty transmissions as well as most lighter-duty makes. All makes of axles can be reconditioned. The company operates out of a modern, 560 sq m (6,000sqft) building with overhead cranage and ample storage area in Dawson Street, Pendlebury Industrial Estate, Swinton, Manchester.
Since 1979, when the company started, the two directors have seen the nature of the business completely reversed. Then 30% of the business was repairing customer units with the remainder consisting of service exchange reconditioned units. Now these positions are completely reversed with customer own-units repairs making up 70% of Driveline's business.
"This is a result of the tough financial conditions existing in transport today," comments Roy Purcell. A Driveline customer repair unit involves the company stripping down and reporting on the degree of repair required, which in most cases works out cheaper than a reconditioned gearbox or axle.
Unlike many other companies involved in reconditioning Driveline actually encourages its customers to be present when their units are being stripped. Dependent on the level of wear/damage the customer then has the option of a reconditioned unit, their own unit repaired to reconditioned standards or a parts only repair.
Whatever the level of service required by the customer, and with all units taken in exchange for reconditioning, a full report is prepared. This details the type of wear or damage present on the unit for repair.
The customers benefit from this engi neer's report as Driveline is able to pinpoint failures which have occurred from external factors. Poor driving technique for instance can he detected from excessive wear on items such as the sychroniser cones. Poor gearbox mounting or driveshaft wear can also be diagnosed from the condition of the gearbox or axle sent in for attention.
"We fmd that if we do not draw these items to the customer's attention, the same premature wear patterns will be present when the reconditioned unit is fitted and hence its service life will be reduced. Thus it is in the customer's interest as well as our own to point out if there are any adverse external conditions which will effect the transmission," Kreisler remarks.
Among the many items kept by the company to demonstrate the effects of exterior forces reducing gearbox life are a Fuller main shaft which has been twisted like a stick of licquorice and another shaft which has been completely sheared, both as a result of driver abuse.
Similarly Driveline has found that some vehicle applications present different patterns of wear. For instance some ZF transmissions in vee-engine-powered Mercedes trucks suffer from a vibration failure on the teeth of the intermediate shaft carrying the engaging plate, which is not found in DAFs equipped with similar transmission.
All gearboxes or axles reconditioned by Driveline undergo the same processes from a pre-wash before the main strip, then complete stripping and inspection on specially designed heavy-duty .steel benches. All components are then given a full wash along with the fitter's tools.
At this stage the bench is also completely cleaned down to ensure that the re-build operation is conducted in the cleanest possible conditions. The same skilled engineer carries out all stages of the reconditioning process. Dependent on the gearbox involved, various items are replaced on a mandatory basis.
For instance on a popular box such as a Fuller 9509 the mandatory replacement Items are all bearings, gaskets, seals, 0rings, sliding clutches and sychronisers. Gears. are replaced as required. Also Driveline replace all 0-rings and other seals within the air system. This item is tested in operation for selection and its inter-lock facility.
This list of mandatory replacements is followed with minor variation for most other makes and types of gearbox. Where there are known problems such as the Spicer ST1010 which has a centre fork in its lid there are other mandatory tests and replacements.
In this Spicer gearbox this centre fork is crack tested and replaced in most instances. "We see a lot of things here that the manufacturers are not aware of," comments Conrad Kriesler.
Regarding crack testing, Driveline adopts a policy of testing all known suspected parts which experience has shown to be sometimes faulty. Dye crack testing is used. Also for the purpose of isolating cracking and the possibility of bodged repairs before the unit being sent in for reconditioning, all gearbox casings are completely paint stripped to bare metal prior to rebuild.
The company tends to restrict the use of blasting processes to a minimum, mainly for casing exteriors. Internal components are rarely grit blasted as Driveline reckons there is great difficulty in removing the residue of this process from internal oil ways and the like. Other processes automatically carried out include cleaning and grinding all gasket faces except where there are sound, micro ground faces already existing.
Each completed reconditioned box carries a Driveline plate which gives repair date. Driveline reckons that the price of its reconditioned units are anything up to 40% cheaper than the same factory reconditioned unit.
Currently its 9509A gearbox price reconditioned is 2775 representing a saving of some 2262 on a factory reconditioned unit. All Driveline units are warranted for 12 months. "We build to a quality specification using genuine parts and reckon to provide the highest standards of reconditioned units," Kriesler comments.
"Key to the company's quality and reasonable prices is our high-grade core stock. This covers not only Eaton Fuller units but also Continental makes such as Volvo, Scania and ZF. We are able to handle most heavy-duty transmission repairs on UK or imported chassis," says Purcell.
Obviously Driveline finds that core stock for some Continental makes is hard to obtain and very expensive, but in most instances it is able to offer a 24/48 hour service in the vast majority of cases. Driveline also offers a service which it claims to be unique. This calls upon the directors' factory experience of transmission specification to a high degree.
To correct poor original transmission specification, or to match the vehicle to changed operational circumstances, Driveline will retrofit with its reconditioned units to improve performance. This retrofit service has included over the years replacing Continental truck gearboxes with Fuller units and complete driveline replacement in some instances to provide a better range of performance for vehicles involved in very heavy haulage. As part of this service, Conrad Kriesler and Roy Purcell produce a specification for the operator laying down gradeability and performance before re trofitting and also ensure that the vehicle tachograph is recalibrated to suit. This service has not just been restricted to older vehicles. The company has carried out a number of retrofit installations on nearly new trucks where the wrong gearing was specified for the operation in hand.
Also claimed by Driveline to be unique to itself, is its reconditioned programme for Fuller auxiliary gearbox units. In many instances the multiplying range-change auxiliary section will fail. The main gearbox will be satisfactory in most instances, and in these cases Driveline is able to supply a reconditioned auxiliary unit considerably cutting down on reconditioning costs.
Driveline's reconditioning service is available to operators throughout the UK. The company deals direct with operators and uses express carriers to dispatch reconditoned units. "In addition we also carry one of the best stocks of Fuller components in the North West," remarks Conrad Kriesler. 'This is an area of business we are working to expand both here in the UK and abroad; already we are exporting to a number of countries in Europe".
by Phil Reed