Expertise at the sharp end
Page 108
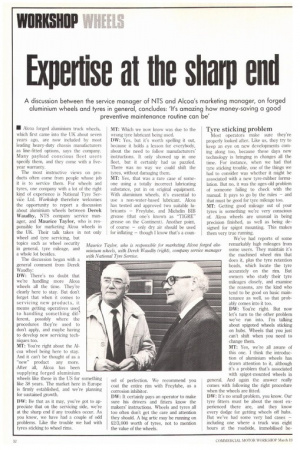
Page 109
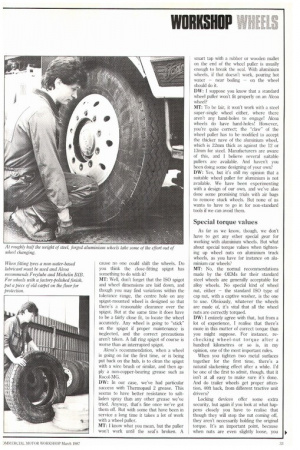
Page 110
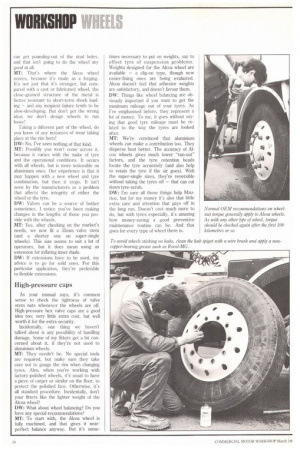
If you've noticed an error in this article please click here to report it so we can fix it.
A discussion between the service manager of NTS and Alcoa's marketing manager, on forged aluminium wheels and tyres in general, concludes: 'It's amazing how money-saving a good preventive maintenance routine can be'
Maurice T minium w with Natio El Alcoa forged aluminium truck wheels, which first came into the UK about seven years ago, are now included by most leading heavy-duty chassis manufacturers as line-fitted options, says the company. Many payload conscious fleet users specify them, and they come with a fiveyear warranty.
The most instructive views on products often come from people whose job it is to service them. For wheels and tyres, one company with a lot of the right kind of experience is National Tyre Service Ltd. Workshop therefore welcomes the opportunity to report a discussion about aluminium wheels between Derek Waudby, NTS company service manager, and Maurice Taylor, who is responsible for marketing Alcoa wheels in the UK. Their talk takes in not only wheel and tyre servicing, but topics such as wheel security in general, tyre mileage, and a whole lot besides.
The discussion began with a general comment from Derek Waudby:
DW: There's no doubt that we're handling more Alcoa wheels all the time. They're clearly here to stay. But don't forget that when it comes to servicing new products, it means getting operatives used to handling something dif-,` fcrcnt, possibly where the procedures they're used to don't apply, and maybe having to develop new servicing techniques too.
MT: You're right about the Alcoa wheel being here to stay. And it can't be thought of as a "new" product any more. After all, Alcoa has been supplying forged aluminium wheels like these in the US for something like 38 years. The market here in Europe is firmly established, and we're planning for sustained growth.
DW: Be that as it may, you've got to appreciate that on the servicing side, we're at the sharp end if any troubles occur. As you know, we have had a couple of odd problems. Like the trouble we had with tyres sticking to wheel rims. MT: Which we now know was due to the wrong tyre lubricant being used.
DW: Yes, but it's worth spelling it out, because it holds a lesson for everybody, about the need to follow manufacturers' instructions. It only showed up in one fleet, but it certainly had us puzzled. There was no way we could shift the tyres, without damaging them.
MT: Yes, that was a rare case of someone usinga totally incorrect lubricating substance, put in on original equipment. With aluminium wheels, it's essential to use a non-water-based lubricant. Alcoa has tested and approved two suitable lubricants — Freytube, and Michelin BIB grease (that one's known as "TIGRE" grease on the Continent). Another point, of course — only dry air should be used for inflating — though I know that's a coun sel of perfection. We recommend you coat the entire rim with Freylube, as a corrosion inhibitor.
DW: It certainly pays an operator to make sure his drivers and fitters know the makers' instructions. Wheels and tyres all too often don't get the care and attention they should. A big artic may be running on £2/3,000 worth of tyres, not to mention the value of the wheels.
Tyre sticking problem
Most operators make sure they're properly looked after. Like us, they try to keep an eye on new developments coming along too, because these days new technology is bringing in changes all the time. For instance, when we had that tyre sticking trouble, one of the things we had to consider was whether it might be associated with a new tyre-rubber formulation. But no, it was the ages-old problem of someone failing to check with the manual. It pays to go by the rules — and that must be good for tyre mileage too.
MT: Getting good mileage out of your tyres is something we're very conscious of. Alcoa wheels are unusual in being precision finished, as well as being designed for spigot mounting. This makes them very true running.
We've had reports of some remarkably high mileages from some users. They maintain it's the machined wheel rim that does it, plus the tyre retention heads, which locate the tyre accurately on the rim. But owners who study their tyre mileages closely, and examine the reasons, are the kind who tend to be good on basic maintenance as well, so that probably comes into it too.
DW: You're right. But now • let's turn to the other problem we've run into. I'm talking about spigoted wheels sticking on hubs. Wheels that you just can't shift when you need to change them.
MT: Yes, we're all aware of this one. I think the introduction of aluminium wheels has drawn attention to it, although it's a problem that's associated with spigot-mounted wheels in general. And again the answer really comes with following the right procedure when the wheels are fitted.
DW: It's no small problem, you know. Our tyre fitters must be about the most experienced there are, and they know every dodge for getting wheels off hubs. But we've had some very bad cases — including one where a truck was eight hours at the roadside, immobilised be
When fitting tyres a non-water-based lubricant must be used and Akoa recommends Freylube and Michelin BIB. For wheels with a factoq-polished finish, put a piece of old carpet on the floor for protection. cause no one could shift the wheels. Do you think the close-fitting spigot has something to do with it?
MT: Well, don't forget that the ISO spigot and wheel dimensions are laid down, and though you may find variations within the tolerance range, the centre hole on any spigot-mounted wheel is designed so that there's a reasonable clearance over the spigot. But at the same time it does have to be a fairly close fit, to locate the wheel accurately. Any wheel is going to "stick" on the spigot if proper maintenance is neglected, and the correct precautions aren't taken. A full ring spigot of course is worse than an interrupted spigot.
Alcoa's recommendation, when a wheel is going on for the first time, or is being put back on the hub, is to clean the spigot with a wire brush or similar, and then apply a non-copper-bearing grease such as Rocol-MG.
DW: In our case, we've had particular success with Thermopaul 2 grease. This seems to have better resistance to saltladen spray than any other grease we've tried. Anyway, that's fine once we've got them off. But with some that have been in service a long time it takes a lot of work with a wheel puller.
MT: I know what you mean, but the puller won't work until the seal's broken. A smart tap with a rubber or wooden mallet on the end of the wheel puller is usually enough to break the seal. With aluminium wheels, if that doesn't work, pouring hot water — near boiling — on the wheel should do it.
DW: I suppose you know that a standard wheel puller won't fit properly on an Alcoa wheel?
MT: To be fair, it won't work with a steel super-single wheel either, where there aren't any hand-holes to engage! Alcoa wheels do have hand-holes! However, you're quite correct; the "claw" of the wheel puller has to be modified to accept the thicker nave of the aluminium wheel, which is 22rnm thick as against the 12 or 13mm for steel. Manufacturers are aware of this, and I believe several suitable pullers are available. And haven't you been doing some designing of your own? DW: Yes, but it's still my opinion that a suitable wheel puller for aluminium is not available. We have been experimenting with a design of our own, and we've also done some promising trials with air bags to remove stuck wheels. But none of us wants to have to go in for non-standard tools if we can avoid them.
Special torque values
As far as we know, though, we don't have to get any other special gear for working with aluminium wheels. But what about special torque values when tightening up wheel nuts on aluminium truck wheels, as you have for instance on aluminium car wheels?
MT: No, the normal recommendations made by the OEMs for their standard steel wheels are generally acceptable for alloy wheels. No special kind of wheel nut, either — the standard ISO type of cap nut, with a captive washer, is the one to use. Obviously, whatever the wheels are made of, it's vital that all the wheel nuts are correctly torqued.
DW: I entirely agree with that, but from a lot of experience, F realise that there's more in this matter of correct torque than you might suppose. For instance, rechecking wheel-nut torque after a hundred kilometres or so is, in my opinion, one of the most important rules.
When you tighten two metal surfaces together for the first time, there's a natural slackening effect after a while. I'd be one of the first to admit, though, that it isn't at all easy to make sure it's done. And do trailer wheels get proper attention, 401t back, from different tractive unit drivers?
Locking devices offer some extra security, but again if you look at what happens closely you have to realise that though they will stop the nut coming off, they aren't necessarily holding the original torque. It's an important point, because when nuts are even slightly loose, you can get pounding-out of the stud holes, and that isn't going to do the wheel any good at all.
MT: That's where the Alcoa wheel scores, because it's made as a forging. It's not just that it's stronger, but compared with a cast or fabricated wheel, the close-grained structure of the metal is better resistant to short-term shock loading — and any incipient failure tends to be slow-developing. But don't get the wrong idea; we don't design wheels to run loose!
Taking a different part of the wheel, do you know of any instances of wear taking place at the rim horn?
DW: No, I've seen nothing of that kind. MT: Possibly you won't come across it, because it varies with the make of tyre and the operational conditions. It occurs with all wheels, but is more noticeable on aluminium ones. Our experience is that it may happen with a new wheel and tyre combination, but then it stops. It isn't seen by the manufacturers as a problem that affects the integrity of either the wheel or the tyre.
DW: Valves can be a source of bother sometimes. I notice you've been making changes in the lengths of those you provide with the wheels.
MT: Yes, after checking on the market's needs, we now fit a 35nun valve stem (and a shorter one on super-single wheels). This size seems to suit a lot of operators, but it does mean using an extension for inflating inner duals.
DW: If extensions have to be used, my advice is to go for solid ones. For this particular application, they're preferable to flexible extensions.
High-pressure caps
As your manual says, it's common sense to check the tightness of valve stem nuts whenever the wheels are off. High-pressure hex valve caps are a good idea too: very little extra cost, but well worth it for the extra security.
Incidentally, one thing we haven't talked about is any possibility of handling damage. Some of my fitters get a bit concerned about it, if they're not used to aluminium wheels.
MT: They needn't be. No special tools are required, but make sure they take care not to gouge the rim when changing tyres. Also, when you're working with factory-polished wheels, it's usual to have a piece of carpet or similar on the floor, to protect the polished face. Otherwise, it's all standard procedure. Incidentally, don't your fitters like the lighter weight of the Alcoa wheel?
DW: What about wheel balancing? Do you have any special recommendations?
MT: To start with, the Alcoa wheel is fully machined, and that gives it nearperfect balance anyway. But it's some times necessary to put on weights, say to offset tyre of suspension problems. Weights designed for the Alcoa wheel are available — a clip-on type, though new easier-fixing ones are being evaluated. Alcoa doesn't feel that adhesive weights are satisfactory, and doesn't favour them. DW: Things like wheel balancing are obviously important if you want to get the maximum mileage out of your tyres. As I've emphasised before, they represent a lot of money. To me, it goes without saying that good tyre mileage must be related to the way the tyres are looked after.
MT: We're convinced that aluminium wheels can make a contribution too. They disperse heat better. The accuracy of Alcoa wheels gives much lower "run-out" factors, and the tyre retention beads locate the tyre accurately (and also help to retain the tyre if the air goes). With the super-single sizes, they're reversible without taking the tyres off — that can cut down tyre-scrub.
DW: I'm sure all those things help Maurice, but for my money it's also that little extra care and attention that pays off in the long run. Doesn't cost much more to do, but with tyres especially, it's amazing how money-saving a good preventive maintenance routine can be. And that goes for every type of wheel there is.