Grp manifold could lave big advantages
Page 19
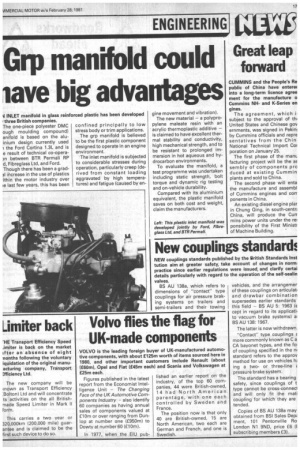
If you've noticed an error in this article please click here to report it so we can fix it.
plastic has been developed The one-piece polyester DMC ough moulding compound) anifold is based on the aluinium design currently used
the Ford Cortina 1.3L and is e result of technical co-opera3n between BTR Permali RP d, Fibreglass Ltd, and Ford.
Though there has been a grad31 increase in the use of plastics ithin the motor industry over ie last few years, this has been confined principally to low stress body or trim applications.
The grp manifold is believed to be the first plastic component designed to operate in an engine environment.
The inlet manifold is subjected to considerable stresses during operation, particularly creep (derived from constant loading aggravated by high temperatures) and fatigue (caused by en gine movement and vibration).
The new material — a polypropylene maleate resin with an acrylic thermoplastic additive — is claimed to have excellent thermal stability and conductivity, high mechanical strength, and to be resistant to prolonged immersion in hot aqueous and hydrocarbon environments.
To evaluate the manifold, a test programme was undertaken including static strength, bolt torque and dynamic rig testing and on-vehicle durability.
Compared with its aluminium equivalent, the plastic manifold saves on both cost and weight, claim the manufacturers.