Countering corrosion
Page 32
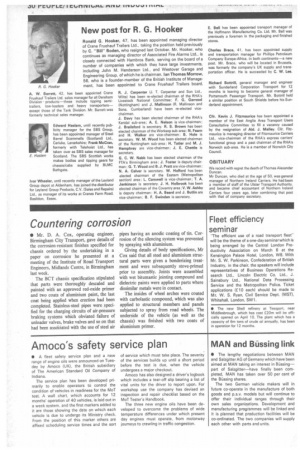
If you've noticed an error in this article please click here to report it so we can fix it.
• Mr. D. A. Cox. operating engineer, Birmingham City Transport, gave details of the corrosion-resistant finishes specified for chassis ordered by the undertaking in a paper on corrosion he presented at a meeting of the Institute of Road Transport Engineers, Midlands Centre, in Birmingham last week.
The BCT chassis specification stipulated that parts were thoroughly descaled and painted with an approved red-oxide primer and two coats of aluminium paint, the last coat being applied when erection had been completed. Stainless-steel pipes were specified for the charging circuits of air-pressure braking systems which obviated failure of unloader valves, brake valves and so on that had been assOciated with the use of steel air
pipes having an anodic coating of tin. Corrosion of the silencing system was prevented by spraying with aluminium.
Giving details of body specifications, Mr Cox said that all steel and aluminium structural parts were given a bonderizing treatment and were subsequently stove-primed prior to assembly. Joints were assembled with wet bitumastic jointing compound and dielectric paints were applied to parts where dissimilar metals were in contact.
The insides of wheel arches were coated with carbolastic compound, which was also applied to structural members and panels subjected to spray from road wheels. The underside of the vehicle (as well as the chassis) was finished with two coats of aluminium primer.