THE DANGER OF THE LOST AXLE NUT.
Page 53
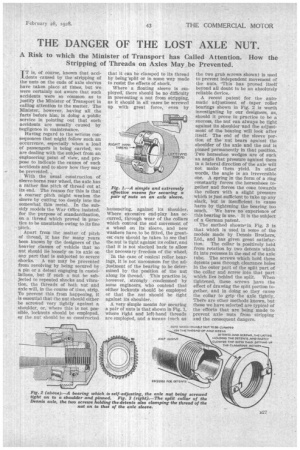
If you've noticed an error in this article please click here to report it so we can fix it.
A Risk to which the Minister of Transport has Called Attention. How the Stripping of Threads on Axles May be Prevented.
JT is, of course, known that accidents caused by the stripping of the nuts on the ends of axle sleeves have taken place at times, but we were certainly not aware that such accidents were so common as to justify the Minister of Transport in calling attention to the matter. The Minister, however, having all the facts before him, is doing a public service in pointing out that such accidents are usually caused by negligence in maintenance.
Having regard to the serious consequences that might follow such an occurrence, especially when a load of passengers is being carried, we are dealing with the subject from an engineering point of view, and propose to indicate the causes of such accidents and to show how they may be prevented.
With the usual construction of sleeve-borne rear wheel, the axle has a rather fine pitch of thread cut at its end. The reason for this is that a coarser pitch might weaken the sleeve by cutting too deeply into the somewhat thin metal. In the subsidy models the War Office insisted, for the purpose or standardization, on a thread which proved in practice to be unsuitable owing to its fine -pitch.
Apart from the matter of pitch of thread, it has for many years been known by the designers of the heavier classes of vehicle that no nut should lie loosely on its axle on any part that is subjected to severe shocks. A nut may be prevented from revolving by being secured by a pin or a detent engaging in caste!. lations, but if such a nut be subjected to repeated shocks and vibration, the threads of both nut and axle will, in the course of time, strip. To prevent this from happening, it is essential that the nut should either be screwed very tightly against a shoulder, or, where this is not possible, locknuts should be employed, or the nut should be so constructed
that it can be clamped to its thread by being'spHt or in some way made to resist the effects of shock.
Where a floating sleeve is employed, there should be no difficulty in preventing a nut from stripping, as it should in all cases be screwed up with great force, even by hammering, against its shoulder. Where excessive end-play has occurred, through wear of the collars which control the end movement of a wheel on its sleeve, and new washers have to be fitted, the greatest care should be taken to see that the nut is tight against its collar, and that it is not slacked back to allow the necessary freedom of the wheel.
In the case of conical roller bearings, it is not uncommon for the adjustment of the bearing to be determined by the position of the nut• along its thread. This practice is, however, strongly condemned by some engineers, who contend that either locknuts should be employed or that the nut should be tight against its shoulder.
A very simple means for securing a pair of nuts is that shown in Fig. I, where right and left-hand threads are employed, and a means (such as the two grub screws shown) is used to prevent independent movement of the nuts. 'This has proved itself beyond all doubt to be an absolutely reliable device.
A recent patent for the automatic adjustment of taper roller bearings shown in Fig. 2 is worth investigating by our designers, as, should it prove in practice to be a success, the nut can always be tight against its shoulder and the adjustment of the bearing will look after itself. The end of the sleeve portion of the nut bears against the shoulder of the axle and the nut is pinned permanently in that position. Two horseshoe wedges are of such an angle that pressure against them in a lateral direction of the axle will not make them yield. In other words, the angle is an irreversible one. A spring in the form of a ring constantly forces the horseshoes together and forces the cone towards the rollers with a slight pressure which is just sufficient to take up any slack, but is insufficient to cause harm by tightening the bearing too much. We have no experience of this bearing in use. It is the subject of a German patent.
The method shown.-in Fig. 3 is that which is used in some of the models made by Dennis Brothers, Ltd., and has given great satisfaction. The collar is positively held from rotation by two &tents which fit into recesses in the end of the axle tube. The screws which hold these &tents pass through clearance holes in the outer part of the split part of the collar and screw into that part which lies behind the split. When tightened, these screws have the effect of drawing the split portion together, and in doing so they cause the collar to grip the axle tightly. There are other methods known, hut those we have selected are typical of the efforts that are being made to prevent axle nuts from stripping and the consequent dangers,