Automatic Trolleybus Acceleration Equipment
Page 53
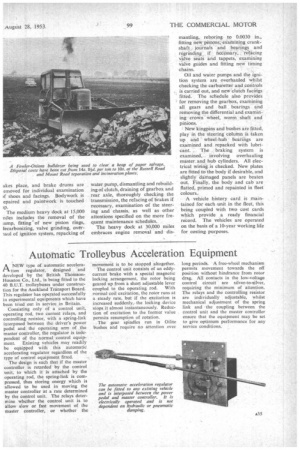
If you've noticed an error in this article please click here to report it so we can fix it.
ANEW type of automatic acceleration regulator, designed and developed by the British ThomsonHouston Co., Ltd., is being fitted to the 40 B.U.T. trolleybuses under construction for the Auckland Transport Board. This regulator has operated successfully in experimental equipments which have been tried out in service in Britain.
Consisting only Of a control unit, operating rod, two current relays, and controlling resistor, with a spring-link interposed between the driver's power pedal and the operating arm of the master controller, the regulator is independent of the normal control equipment. Existing vehicles may readily be equipped with this automatic accelerating regulator regardless of the type of control equipment fitted
The design is such that if the master controller is retarded by the control unit, to which it is attached by the operating rod, the spring-link is compressed, thus storing energy which is allowed to be used in moving the master controller at a rate determined by the control unit. The relays determine whether the control unit is to allow slow or fast movement of the master controller, or whether the
movement is to be stopped altogether.
The control unit consists of an eddycurrent brake with a special magnetic locking arrangement, the rotor being geared up from a short adjustable lever coupled to the operating rod. With normal coil excitation, the rotor runs at a steady rate, but if the excitation is increased suddenly,, the locking device stops it almost instantaneously. Reduction of excitation to the former value permits resumption of rotation.
The gear spindles run in Oilite bushes and require no attention over
long periods. A free-wheel mechanism permits movement towards the off position without hindrance from rotor drag. All contacts in the low-voltage control circuit are silver-to-silver, requiring the minimum of attention. The relays and the controlling resistor are individually adjustable, whilst mechanical adjustment of the spring link and the coupling between the control unit and the master controller ensure that the equipment may be set to give optimum performance for any service conditions.