The only way
Page 39
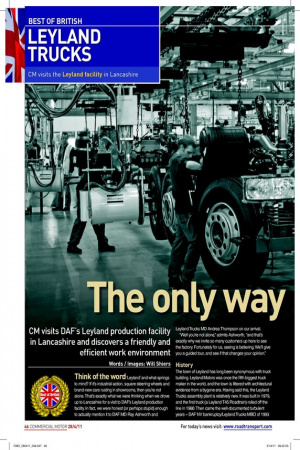
Page 40
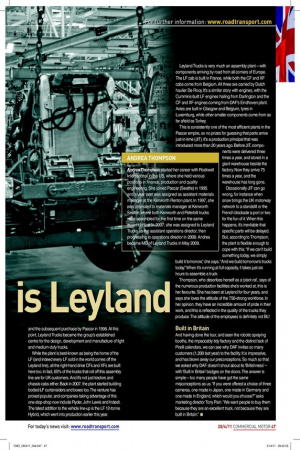
If you've noticed an error in this article please click here to report it so we can fix it.
CM visits DAF’s Leyland production facility in Lancashire and discovers a friendly and efficient work environment
Words / Images: Will Shiers
Think of the word ‘Leyland’ and what springs to mind? If it’s industrial action, square steering wheels and brand-new cars rusting in showrooms, then you’re not alone. That’s exactly what we were thinking when we drove up to Lancashire for a visit to DAF’s Leyland production facility. In fact, we were honest (or perhaps stupid) enough to actually mention it to DAF MD Ray Ashworth and
Leyland Trucks MD Andrea Thompson on our arrival.
“Well you’re not alone,” admits Ashworth, “and that’s exactly why we invite so many customers up here to see the factory. Fortunately for us, seeing is believing. We’ll give you a guided tour, and see if that changes your opinion.”
History
The town of Leyland has long been synonymous with truck building. Leyland Motors was once the fifth biggest truck maker in the world, and the town is littered with architectural evidence from a bygone era. Having said this, the Leyland Trucks assembly plant is relatively new. It was built in 1979, and the first truck (a Leyland T45 Roadtrain) rolled off the line in 1980. Then came the well-documented turbulent years – DAF NV bankruptcy/Leyland Trucks MBO of 1993 and the subsequent purchase by Paccar in 1998. At this point, Leyland Trucks became the group’s established centre for the design, development and manufacture of light and medium-duty trucks.
While the plant is best-known as being the home of the LF (and indeed every LF sold in the world comes off the Leyland line), all the right-hand drive CFs and XFs are built here too. In fact, 65% of the trucks that roll off this assembly line are for UK customers. And it’s not just tractors and chassis cabs either. Back in 2007, the plant started building bodied LF curtainsiders and boxes too. The venture has proved popular, and companies taking advantage of this one-stop-shop now include Ryder, John Lewis and Indesit. The latest addition to the vehicle line-up is the LF 12-tonne Hybrid, which went into production earlier this year. Leyland Trucks is very much an assembly plant – with components arriving by road from all corners of Europe. The LF cab is built in France, while both the CF and XF cabs come from Belgium. All three are carried by Dutch haulier De Rooy. It’s a similar story with engines, with the Cummins-built LF engines hailing from Darlington and the CF and XF engines coming from DAF’s Eindhoven plant. Axles are built in Glasgow and Belgium, tyres in Luxemburg, while other smaller components come from as far afield as Turkey.
This is consistently one of the most efficient plants in the Paccar empire, so no prizes for guessing that parts arrive just-in-time (JIT). It’s a production principal that was introduced more than 20 years ago. Before JIT, components were delivered three times a year, and stored in a giant warehouse beside the factory. Now they arrive 75 times a year, and the warehouse has long gone.
Occasionally JIT can go wrong, for instance when snow brings the UK motorway network to a standstill or the French blockade a port or two for the fun of it. When this happens, it’s inevitable that specific parts will be delayed. But, according to Thompson, the plant is flexible enough to cope with this. “If we can’t build something today, we simply build it tomorrow,” she says. “And we build tomorrow’s trucks today.” When it’s running at full capacity, it takes just six hours to assemble a truck.
Thompson, who describes herself as a ‘plant rat’, says of the numerous production facilities she’s worked at, this is her favourite. She has been at Leyland for four years, and says she loves the attitude of the 750-strong workforce. In her opinion, they have an incredible amount of pride in their work, and this is reflected in the quality of the trucks they produce. The attitude of the employees is definitely not BL!
Built in Britain
And having done the tour, and seen the robotic spraying booths, the impeccably tidy factory and the distinct lack of Pirelli calendars, we can see why DAF invites so many customers (1,200 last year) to the facility. It is impressive, and has blown away our preconceptions. So much so that we asked why DAF doesn’t shout about its ‘Britishness’ – with ‘Built in Britain’ badges on the doors. The answer is simple – too many people have got the same misconceptions as us. “If you were offered a choice of three cameras, one made in Japan, one made in Germany and one made in England, which would you choose?” asks marketing director Tony Pain. “We want people to buy them because they are an excellent truck, not because they are built in Britain.” ■